
Time-Series Database vs. Relational Database vs. Data Lake
The most important differences between relational databases, time-series databases, and data lakes and other data ...
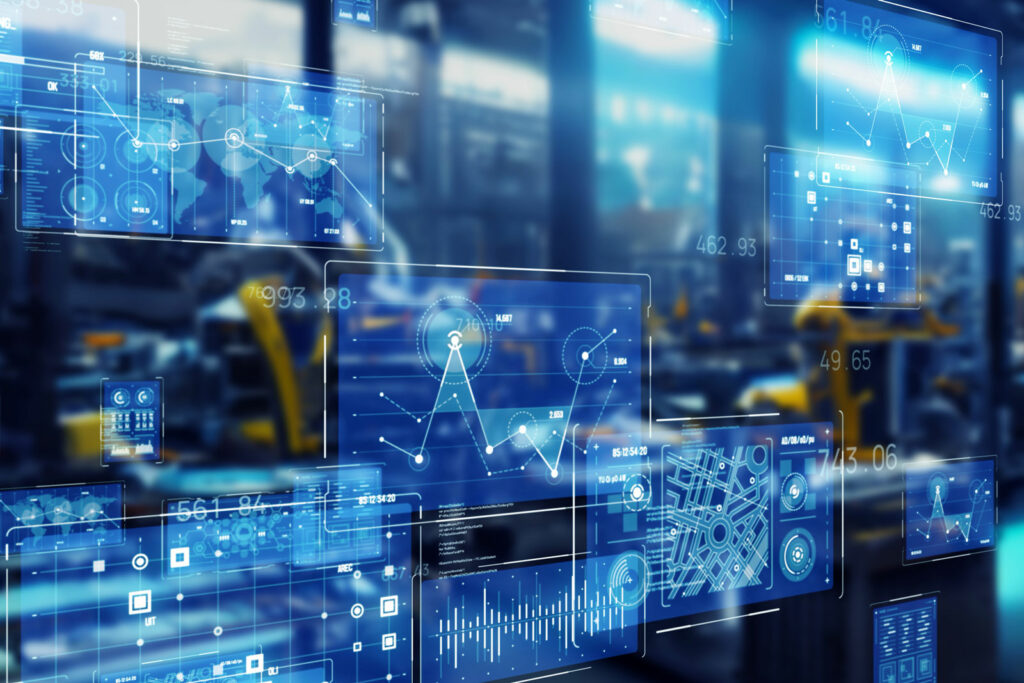
13 Essential Manufacturing KPIs for Continuous Improvement
KPIs are a powerful tool for manufacturers to drive continuous improvement and promote process efficiency. ...
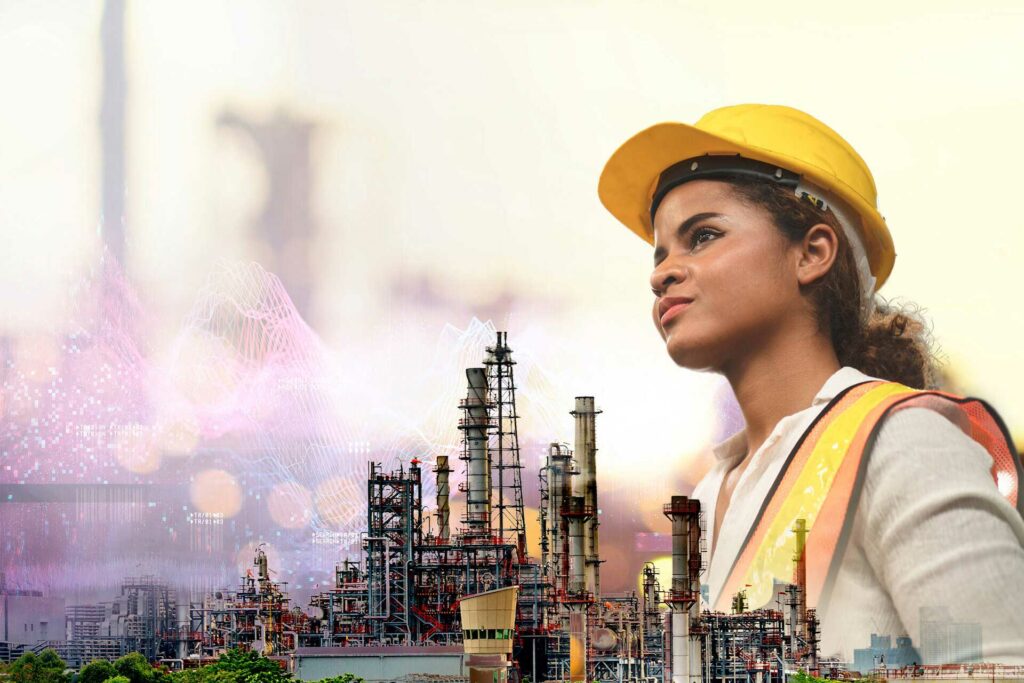
IT/OT Convergence in Manufacturing
IIT/OT Convergence and corresponding buzzwords are all over the place. If you are in manufacturing, ...
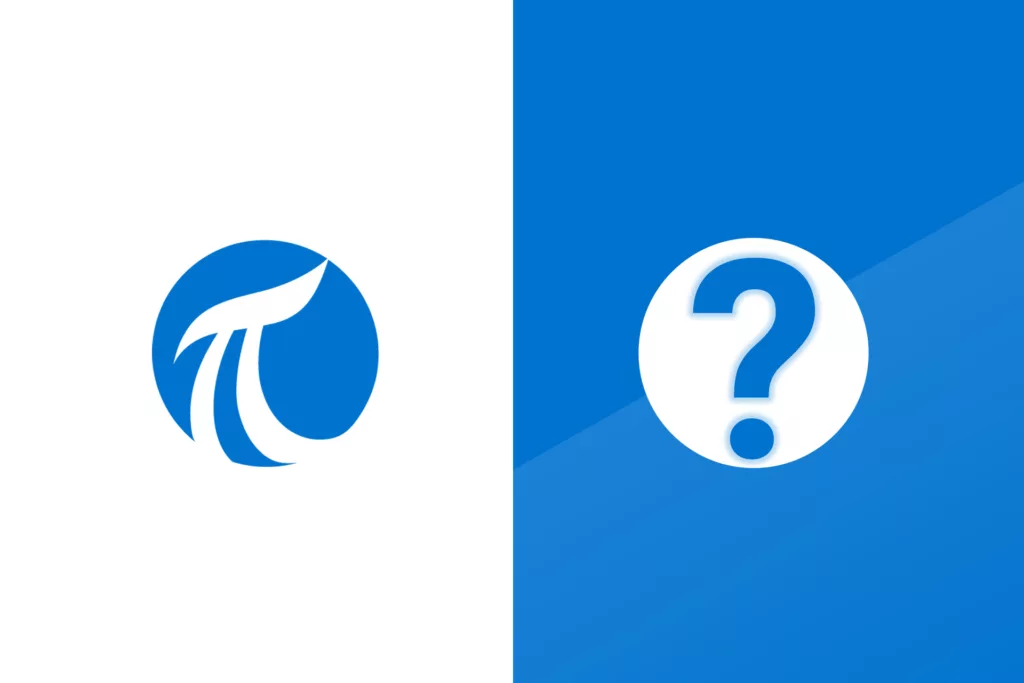
Best Pi ProcessBook Alternatives [2025]
Now that PI ProcessBook is headed toward extinction, many engineers & operators in the process ...
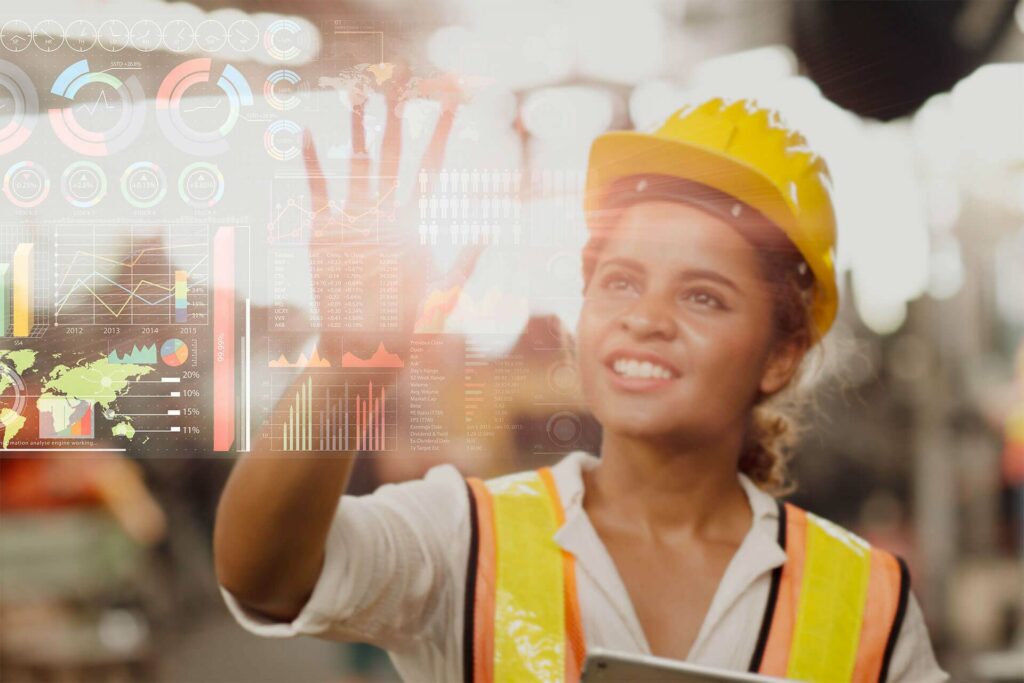
How to Implement 5 Whys Root Cause Analysis in Manufacturing
One of the easiest ways to explain why you should implement 5 whys root cause ...
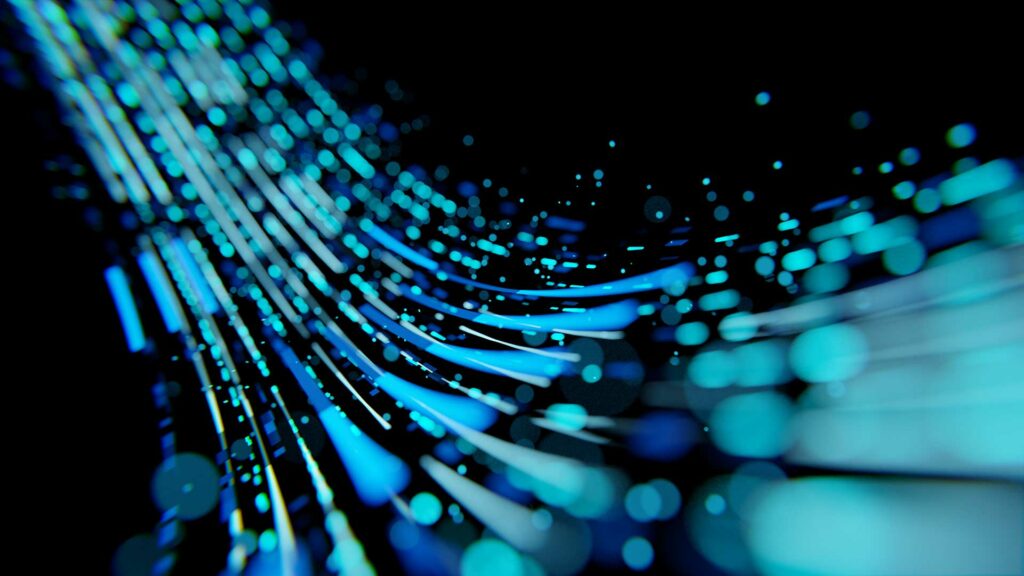
dataPARC vs PI
In the process industries, optimization is the key to efficiency. And efficiency is what leads ...
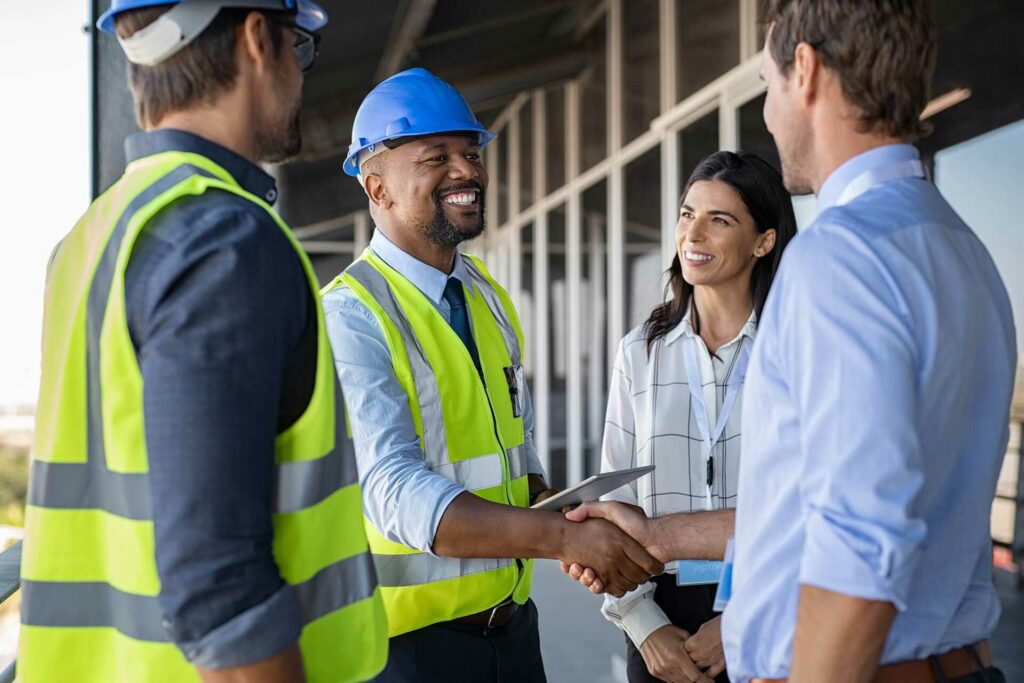
Digital Transformation Roles and Responsibilities in Manufacturing
Where do we start in digitizing our manufacturing operations? one may ask. While there is ...
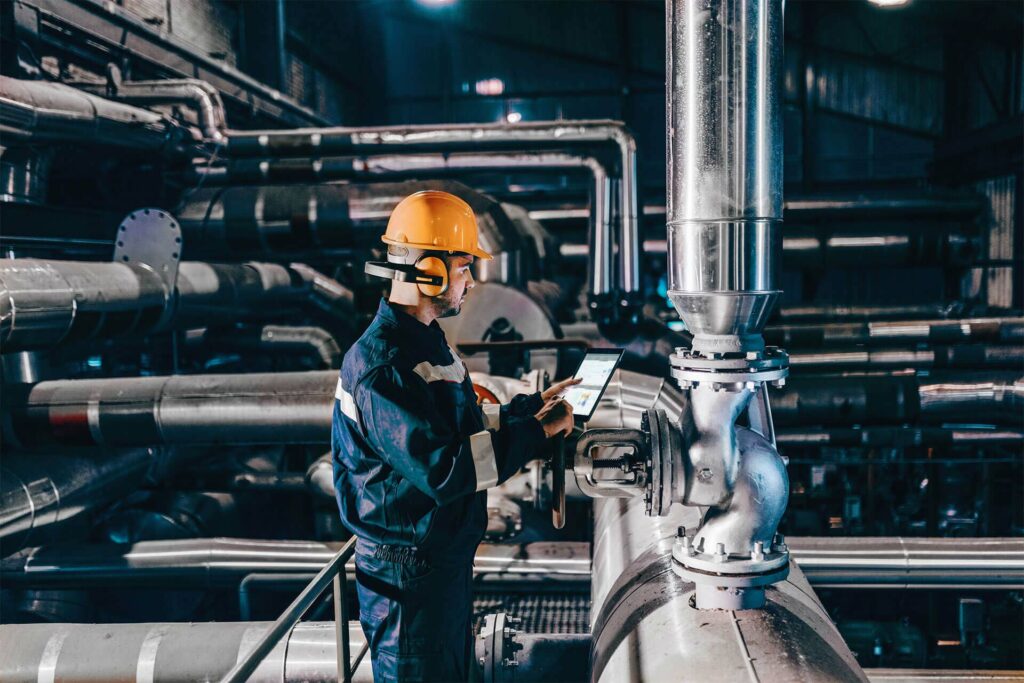
Integrating Manufacturing Data: 6 Combos for Process Analysis
Integrating big data in manufacturing is necessary for many reasons. Among the most important is ...
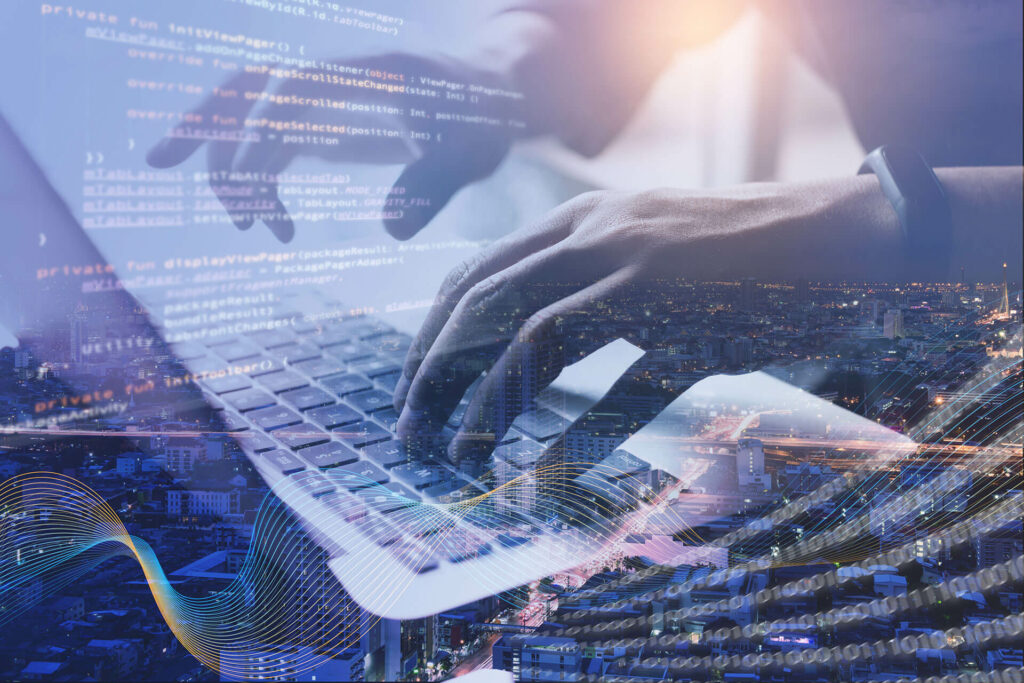
Stages of Digital Transformation in the Process Industry
The stages of digital transformation in the process industries is part of a global shift ...
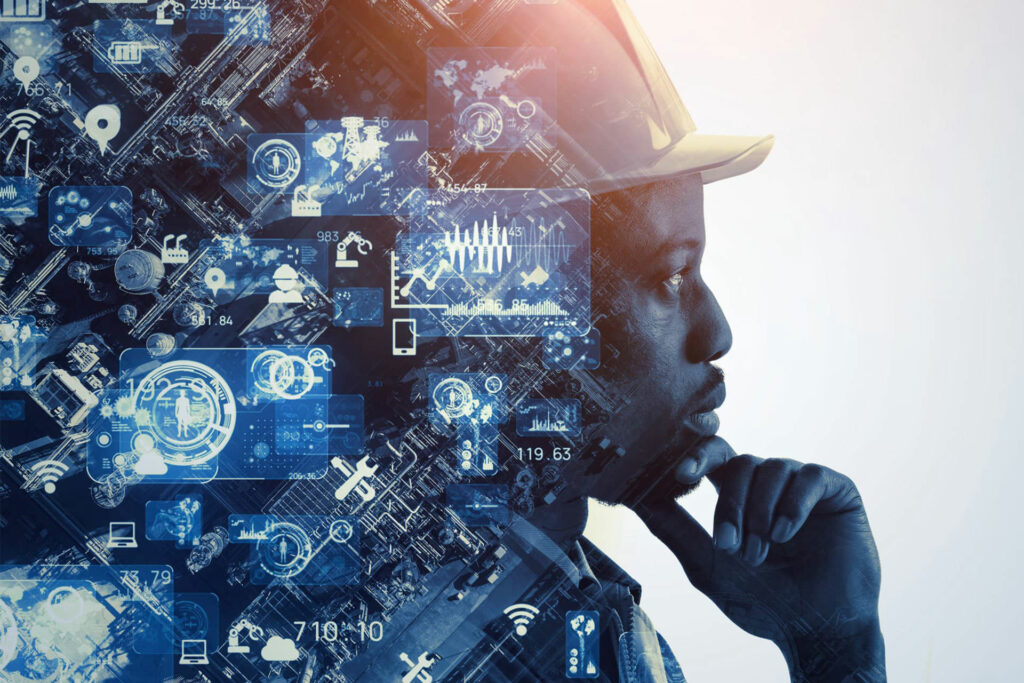
Predictive Modeling in Manufacturing: PLS vs PCA
Predictive models are extremely useful in monitoring and optimizing manufacturing processes. Predictive modeling in manufacturing, ...
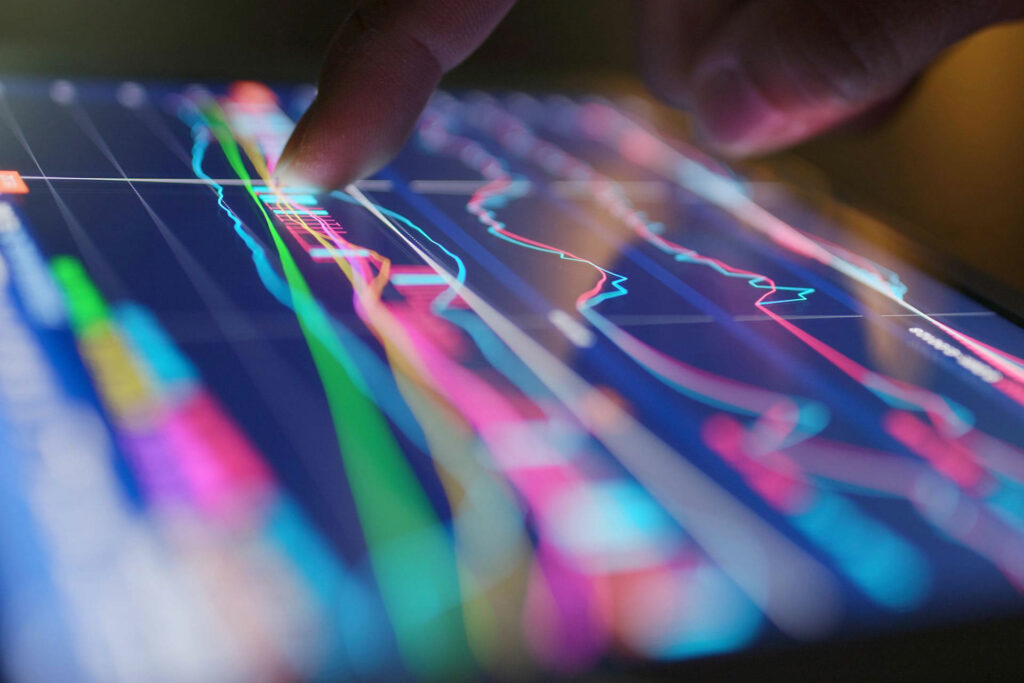
Deviation Analysis in Process Manufacturing
Deviation analysis is a routine form of troubleshooting performed at process manufacturing facilities around the ...

Five Reasons You Should Attend dataPARC’s Virtual Conference
1. You Won’t Have To Take Any Time Off To Attend We are happy to ...
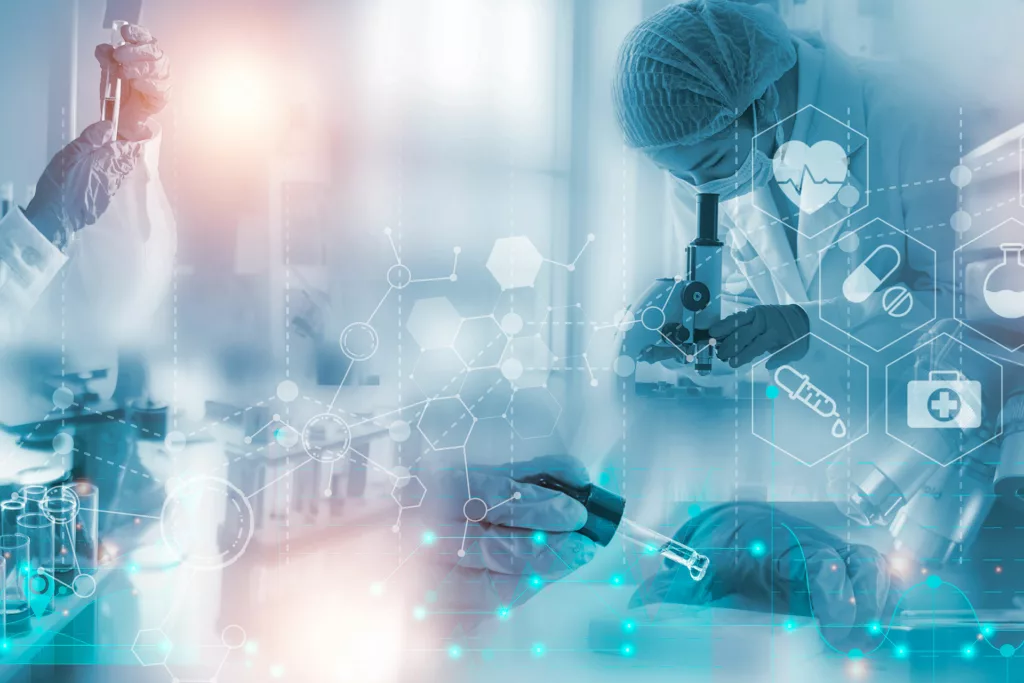
Data Analysis Basics: Uncovering the Impact of Covid-19
How Does Information Answer Questions? Does the information you find always answer the right questions ...
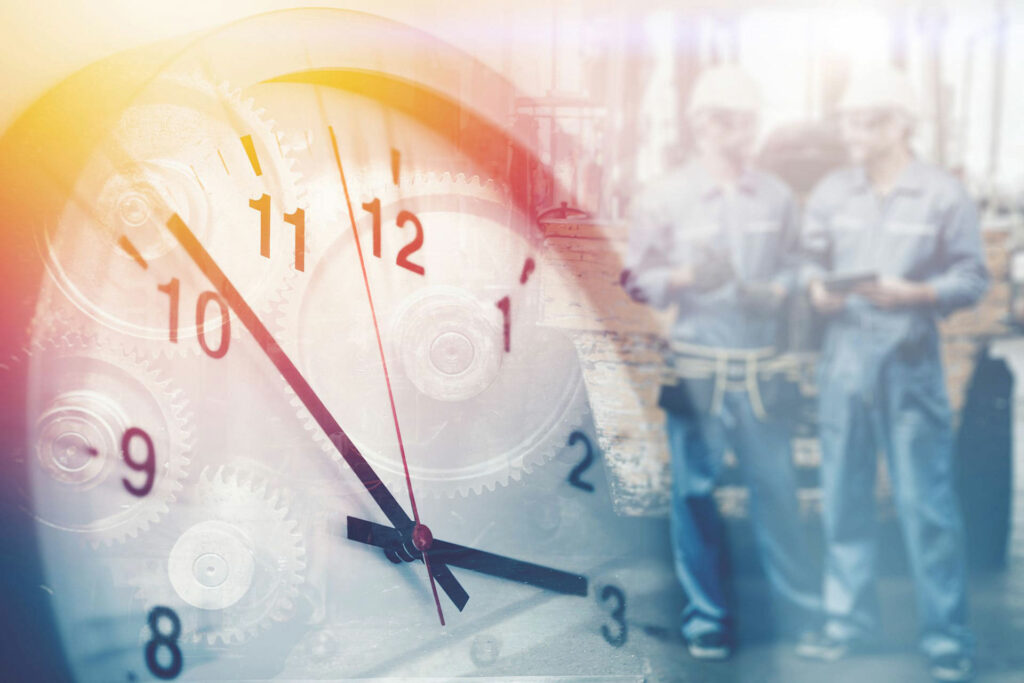
Anomaly Detection for Time Series Data
One of the problems in process manufacturing is that processes tend to drift over time. ...
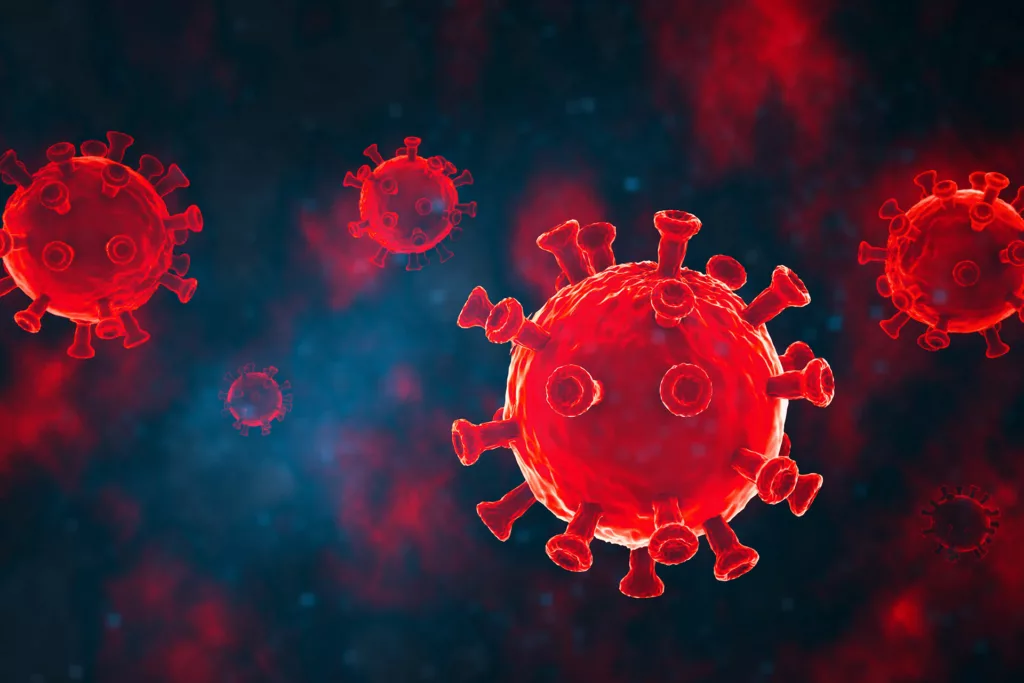
Covid-19: How to Support Manufacturing Operations Remotely
If you’re like us, you’ve likely been sent an email or told in meetings that ...
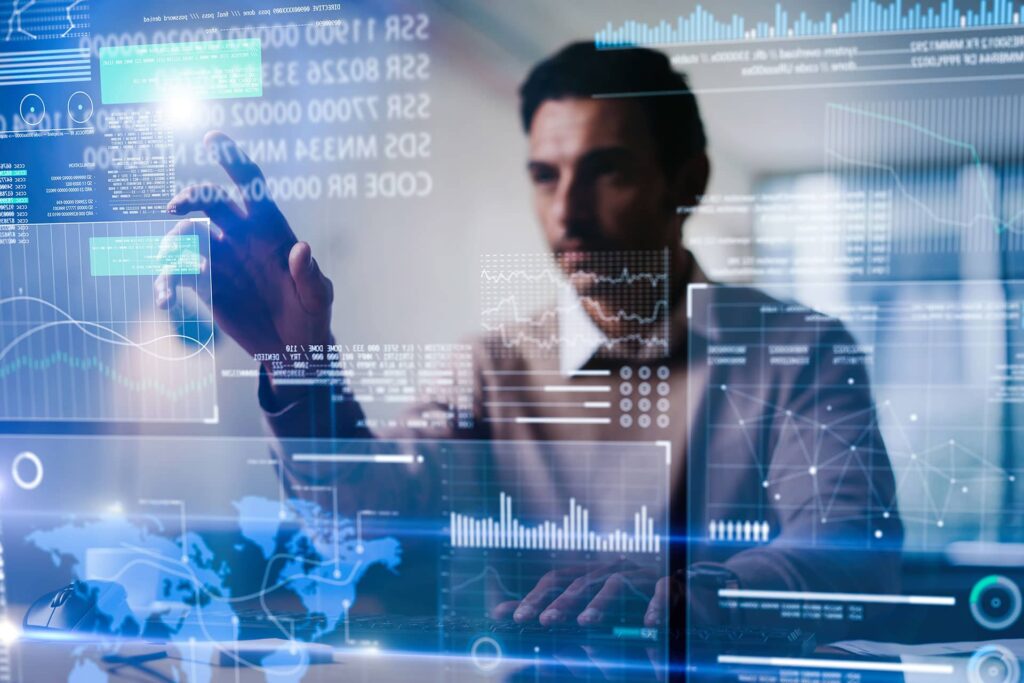
HMI Design Best Practices: The Complete Guide
Most modern manufacturing processes are controlled and monitored by computer based control and data acquisition ...
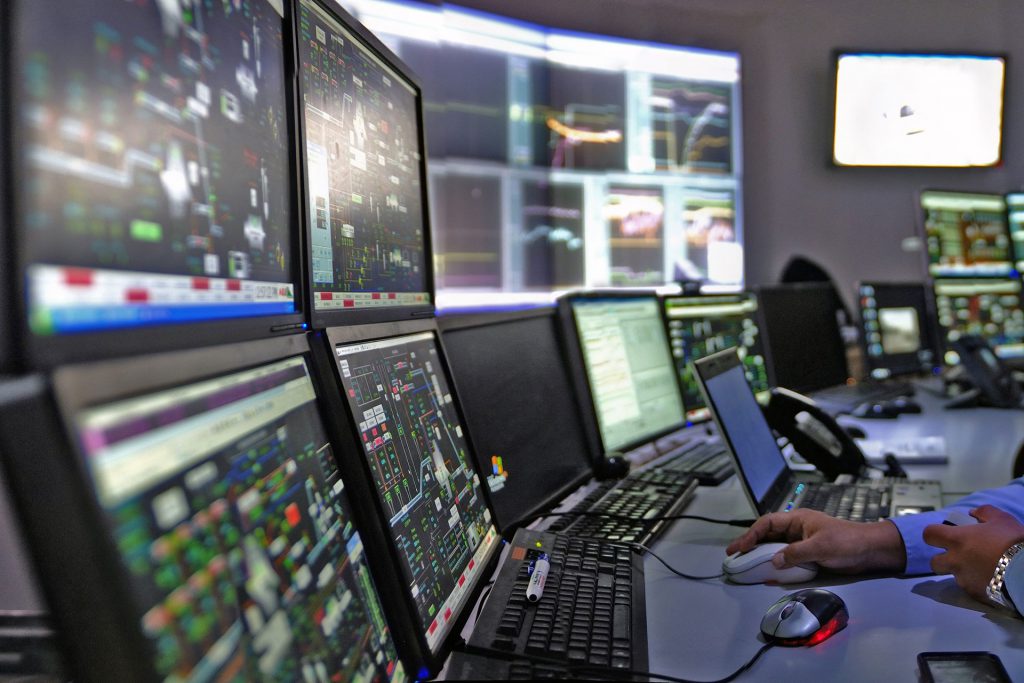
dataPARC – Intuitive Powerful and Connected
dataPARC – Intuitive Powerful and Connected A lot goes into running a mill, plant or ...
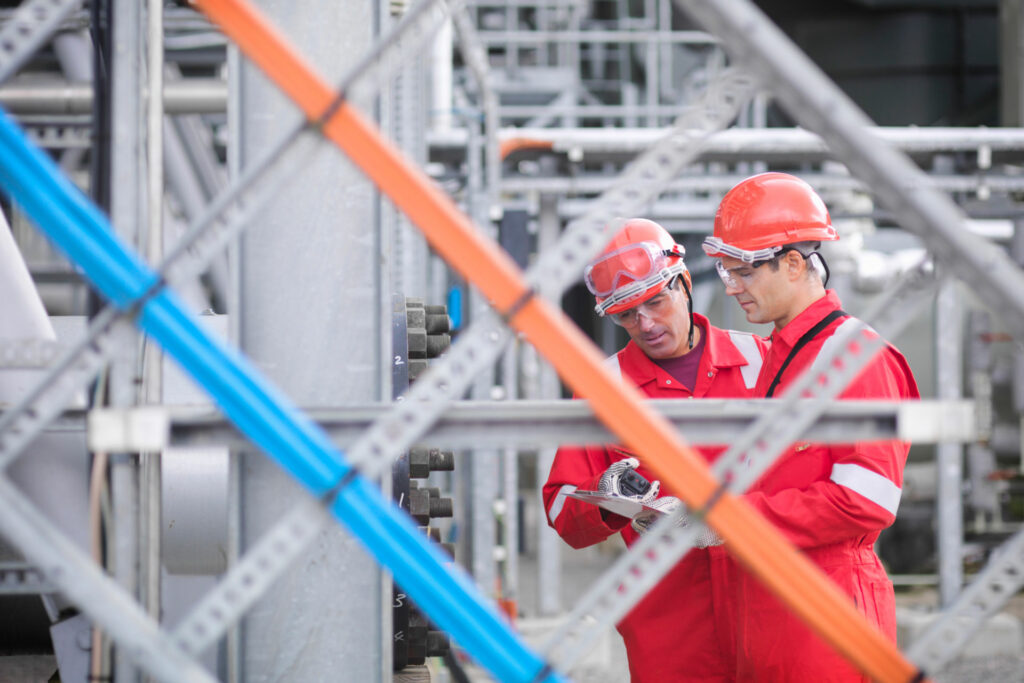
7 Strategies to Improve OEE While Analyzing the 6 Big Losses
Once you have cleared the important hurdle of collecting and calculating OEE data, it’s time ...
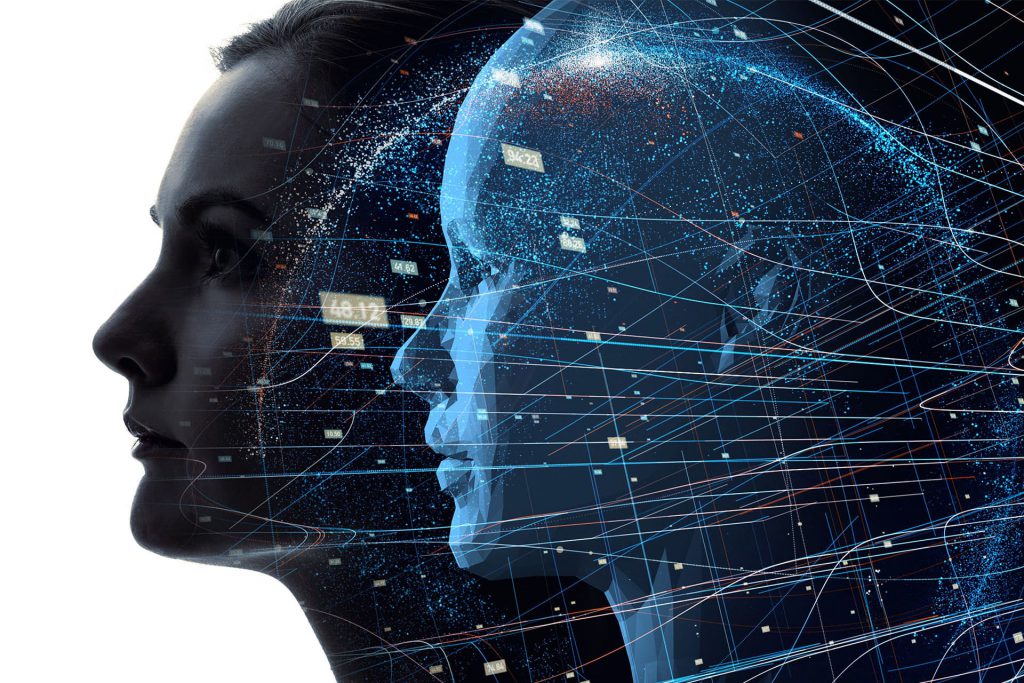
Digital Twin Solutions in Process Manufacturing
In a previous blog post, we explained that contemporary marketing language or buzz words can create confusion. One example of a common buzz word that may cause confusion is the concept of “Digital Twin.” Customers are asking about it and vendors are promoting it. But, what exactly is a Digital Twin? We decided to start with the Wikipedia definition:
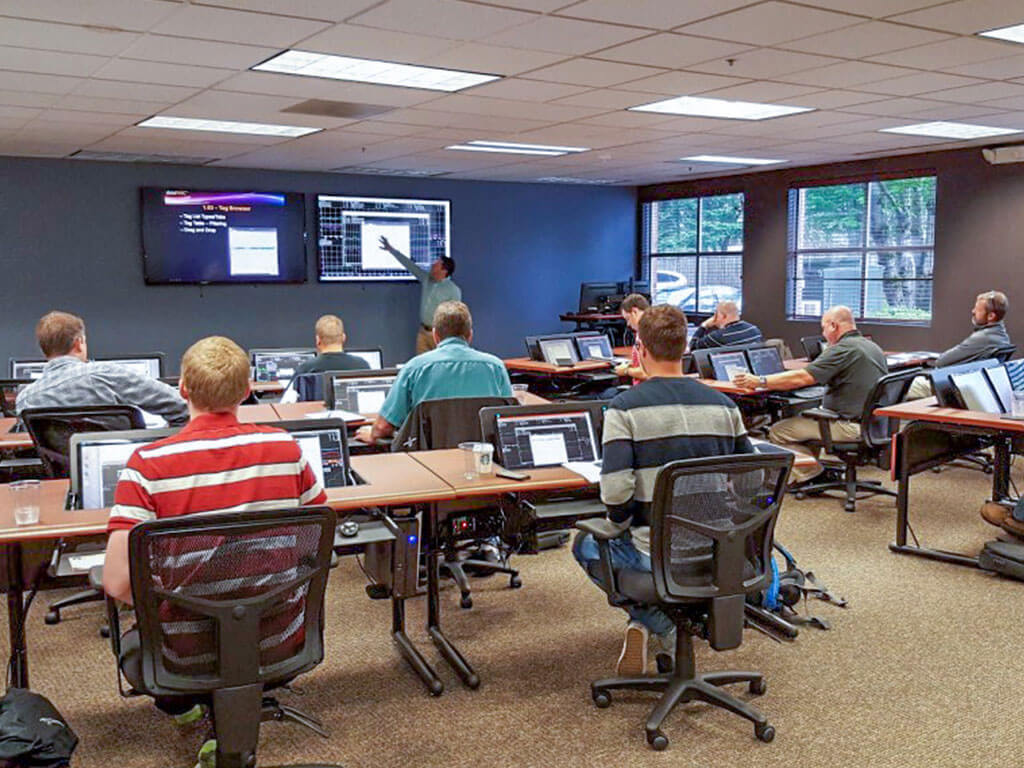
How To Get Your dataPARC Training Approved – Four Strategies That Will Work
How to Get Your dataPARC Training Approved – Four Strategies That Will Work New training ...
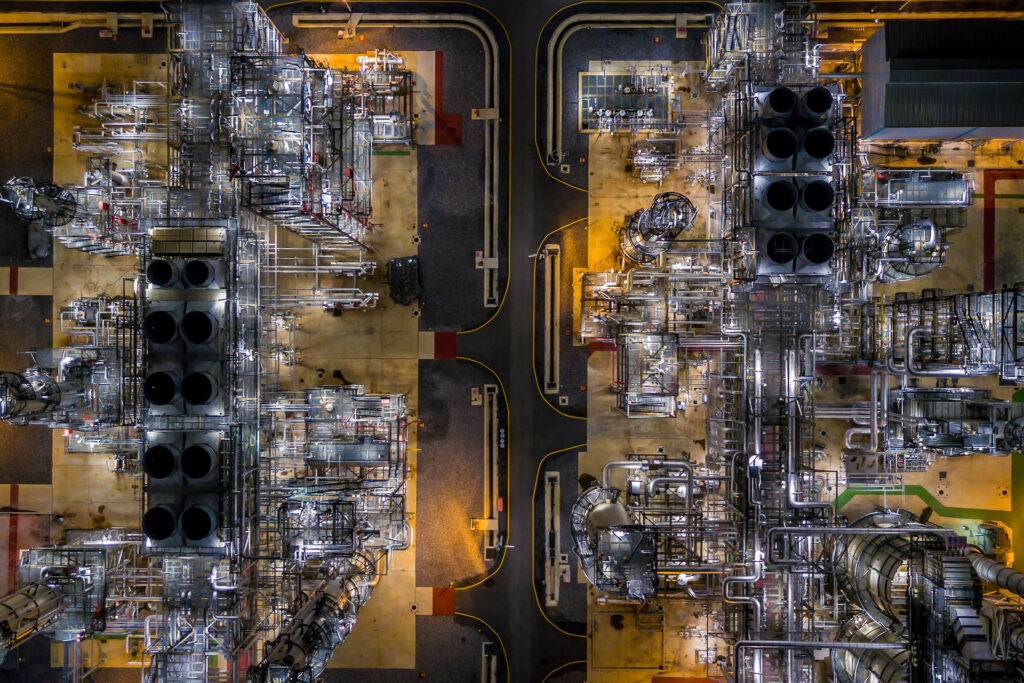
Industrial Energy Monitoring in Manufacturing
All forms of commerce require energy and industrial energy monitoring is essential. Industrial processing facilities ...
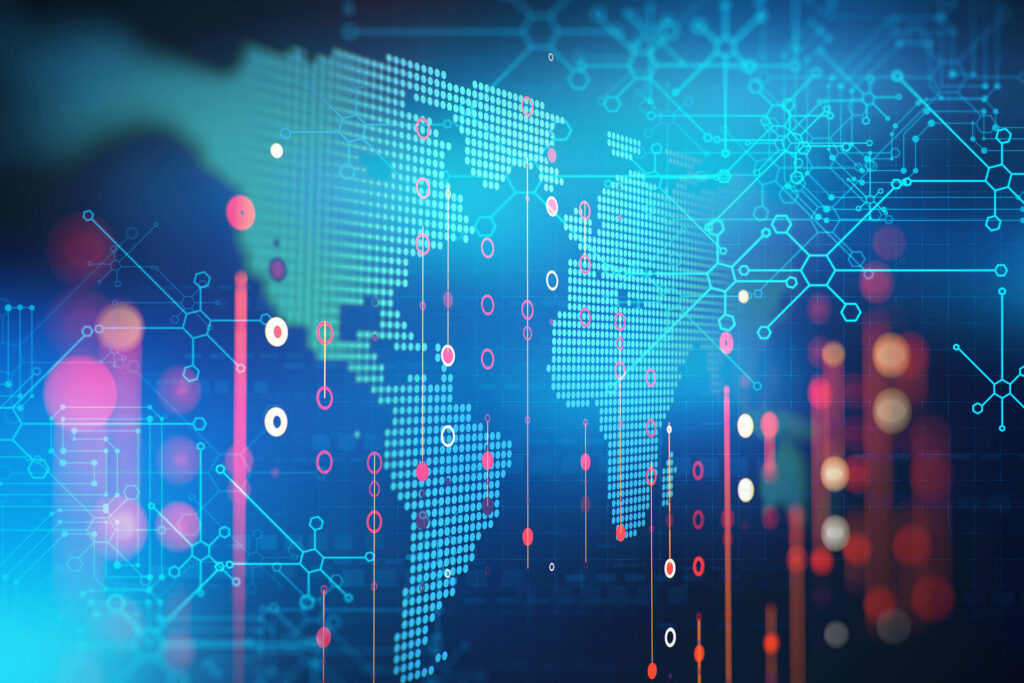
Rethinking Data Compression For Process Historians
Most people are familiar with compressing data files so that they require less memory and ...
2018 dataPARC User Conference – A Recap
The 2018 dataPARC User Conference was a success! Held in Portland Oregon from October 15-18, ...
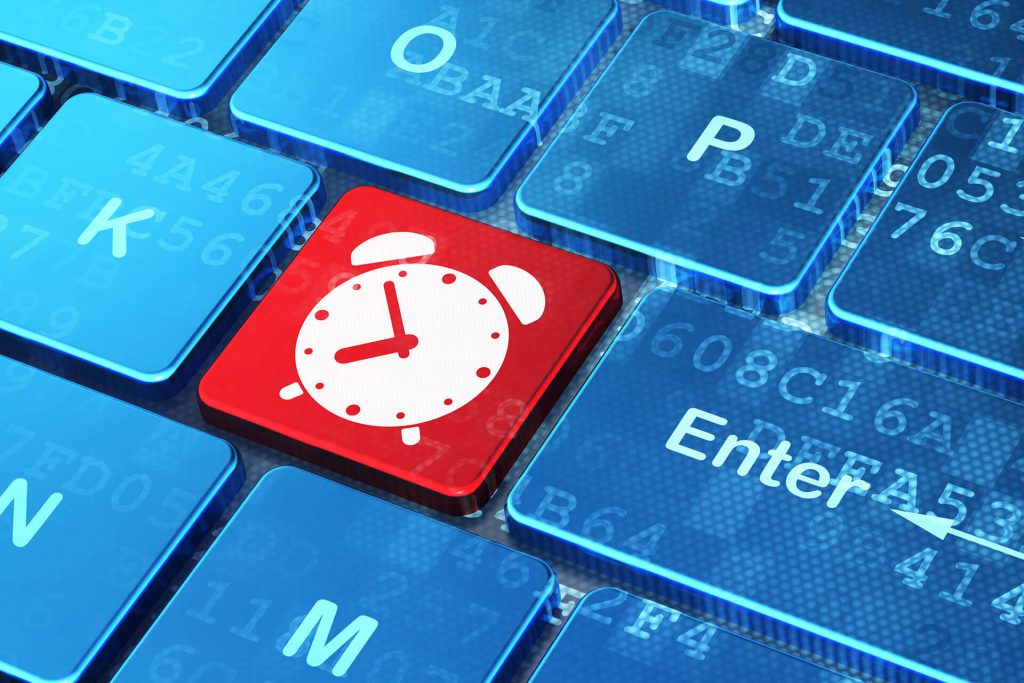
Process Alarm Management Best Practices
The purpose of process control alarms is to use automation to assist operators as they ...
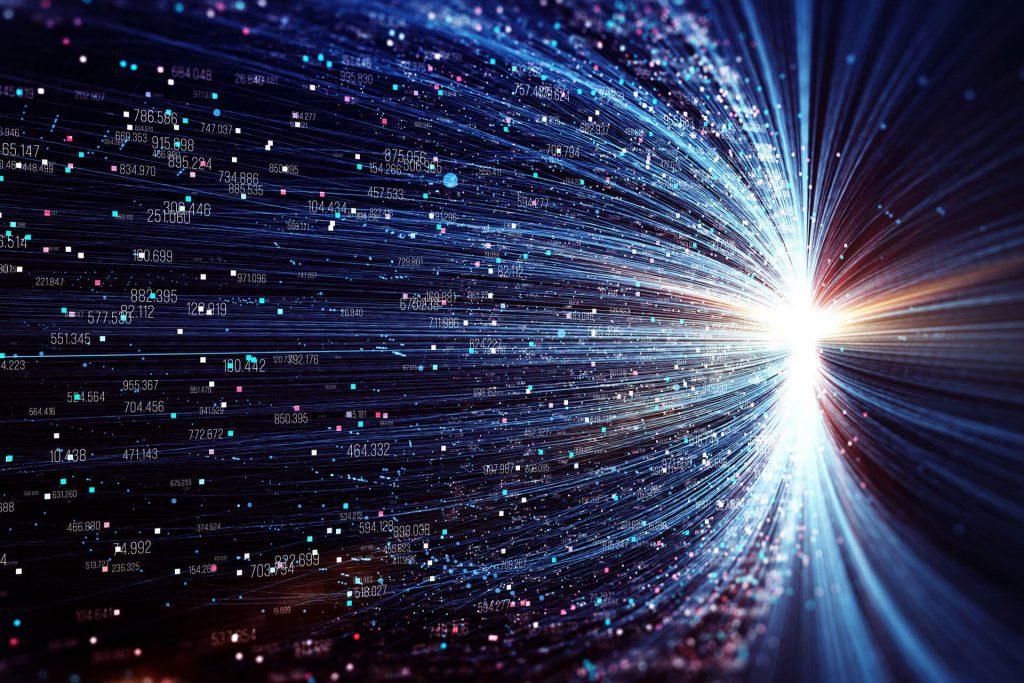
Easily Integrating Maintenance Information With A Computerized Maintenance Management System (CMMS)
One of the challenges facing industrial process along their manufacturing digital transformation is the growing ...
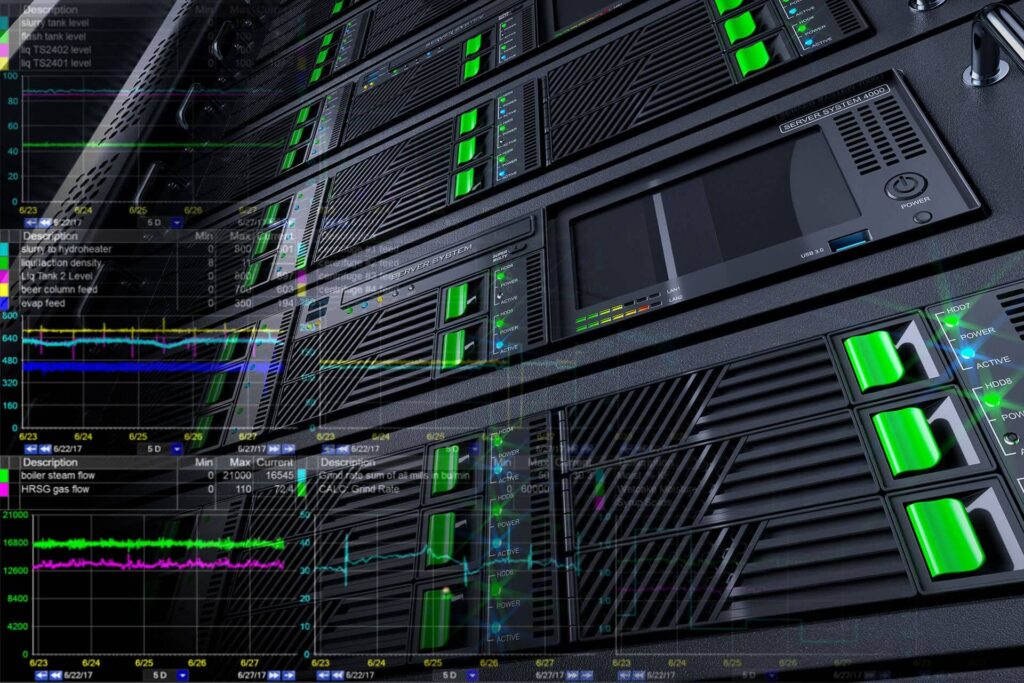
What Makes Good Visualization Software For Data Historians?
There are many different systems available for storing and analyzing manufacturing process data. A historian is a ...
Tech Terms Part II
As mentioned in our previous article, technical terms continue to change and evolve. Below are more terms we found useful to know and understand and think you will, too.