One of the easiest ways to explain why you should implement 5 whys root cause analysis problem-solving technique at your plant is simple: the cause of the problem is often (we’d go so far to say almost always) different than initially speculated. Having a continuous improvement mindset and implementing a lean strategy like 5 whys can save you time and headaches in the future.
Issues and failures of assets are bound to happen in process manufacturing. Your team’s strategy for resolving problems when they occur will determine your productivity in countless ways. Getting a process set up for resolving problems will help resolve underlying issues and failures. It will also create a plan to resolve future problems with the goal of each resolution coming faster and easier.
What Exactly are the 5 Whys?
What is 5 Whys Root Cause Analysis?
5 Whys is a lean problem-solving method. This strategy is popular in many industries driving continuous improvement. Using lean methodology, the 5 whys were developed by Sakichi Toyoda, a Japanese inventor and industrialist. The 5 whys focus on root cause analysis (RCA) and critical thinking. It is defined as a systematic process for identifying the origins of problems and determining an approach for responding to and solving them. 5 whys focuses on prevention or being proactive rather than being reactive. It is a powerful tool to have in your toolkit of manufacturing process optimization strategies.
5 whys strives to be analytical and strategic about getting to the bottom of asset failures and issues. It is a holistic approach that is used by stepping back and looking at the entire process and the big picture. The essence of 5 whys is revealed in the quote below where something as small as a nail in a horse’s shoe being lost was the root cause of a war being lost:
“For want of the nail the shoe was lost
For want of the shoe the horse was lost
For want of a horse the warrior was lost
For want of a warrior the battle was lost
For want of a battle the kingdom was lost
All for the want of a nail.”
One of the key factors for successful implementation of the 5 whys technique is to make an informed decision. This means that the decision-making process should be based on an insightful and comprehensive understanding of what is happening on the plant floor. Hunches and guesses are not adequate as they are the equivalent of a band-aid solution. 5 whys method can be utilized in continuous manufacturing or in a batch process as a batch analysis tool. It has also been utilized in other industries, such as data analysis tools for power generation.
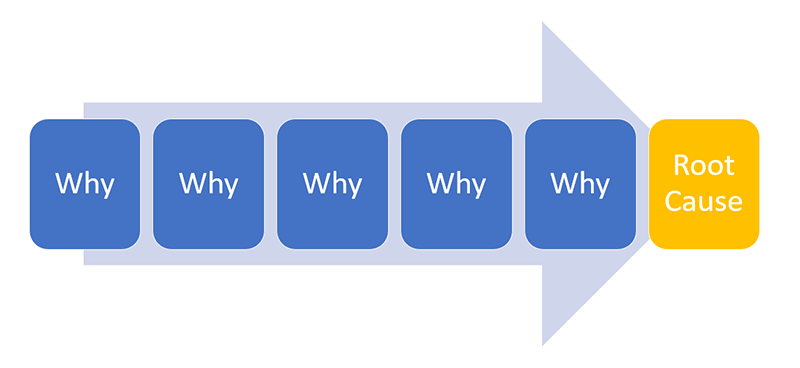
The 5 whys can help you identify the problem’s root, identifying the deeper issues and resolving them at your plant.
The 5 Whys Method in Action
Below is an example of a 5 whys method being used for a problem seemingly as basic as a computer failure. If you look closely, you will conclude that the actual problem has nothing to do with a computer failure.
- Why didn’t your computer perform the task? – Because the memory was not sufficient.
- Why wasn’t your memory sufficient? – Because I did not ask for enough memory.
- Why did you underestimate the amount of memory? – Because I did not know my programs would take so much space.
- Why didn’t you know programs would take so much space? – Because I did not do my research on programs and memory required for my annual projects.
- Why did you not do research on memory required? – Because I am short staffed and had to let some tasks slip to get other priorities accomplished.
As seen in the example above, the real problem was not in fact computer memory, but a shortage in human assets. Without performing this exercise, the person may never have gotten to the place where they knew they were short staffed and needed help.
This example can be used to illustrate problems in a plant as well. Maybe an asset is having repeated failures or lab data is not testing accurately. Rather than immediately concluding that the problem is entirely mechanical, use the 5 whys method and you may discover that your problem is not what you think.al, use the 5 whys method and you may discover that your problem is not what you think.
Advantages and Disadvantages of the 5 Whys Root Cause Analysis
Advantages are easily identified by such outcomes such as being able to identify the underlying root cause of your problem and not just the symptoms. It is simple and easy to use and implement, and perhaps the most attractive advantage is that it helps you avoid taking immediate action without first identifying the real root cause of the problem. Taking immediate action on a path that is not accurate is a waste of precious time and resources.
The disadvantage is that some people may disagree with the different answers that come up for the cause of the problem. It is also only as good as the collective knowledge of the people using it and if time and diligence is not applied, you may not uncover and address the true root cause of the problem.
On the road to digital transformation? Get our Free Digital Transformation Roadmap, a step-by-step guide to achieving data-driven excellence in manufacturing.
5 Whys Root Cause Analysis Implementation at your Plant: A Guide
Now that a thorough understanding of the problem in its essence has been revealed, what are the next steps?
Get Familiar with the 5 Whys Concept
The first step in implementing the 5 whys at your plant is to get familiar with the concept. You may research the 5 whys methodology online or listen to tutorials to gain a deeper understanding. In the information age, we have access to plenty of free information at the touch of our screens. Get acquainted with 5 whys. Even if it is just one video on YouTube and a few articles online, a better understanding means a better implementation.
Schedule and Conduct a 5 Whys Root Cause Analysis Meeting with Your Team
The second step would be to solve a problem at your plant using the 5 whys method. To do so, follow the steps below to schedule and hold a 5 whys RCA meeting.
These steps are simple to give you a basic understanding. To gain a greater understanding in detail of how to implement the 5 whys RCA, read on for in-depth instructions.
- Organize your meeting
- Define your problem statement
- Ask the first “why”
- Ask why four more times
- Determine countermeasures
- Assign responsibilities
- Monitor progress
- Schedule a follow-up meeting
In other words, the root cause analysis process should include people with practical experience. Logically, they can give you the most valuable information regarding any problem that appears in their area of expertise.

What’s Next? What Happens Once I have Held my 5 Whys meeting?
Once your meeting has been held and you begin to implement the 5 whys method, it is essential to remember that some failures can cascade into other failures, creating a greater need for root cause analysis to fully understand the sequence of multiple root cause and failure events.
Root Cause Analysis using the 5 whys method typically has 3 goals:
- Uncover the root cause
- Fully understand how to address and learn from the problem
- Apply the solution to this and future issues, creating a solid methodology to ensure the same success in the future
The Six Phases of 5 Whys Root Cause Analysis
Digging even deeper, when 5 whys root cause analysis is performed, there are six phases in one cycle. The components of asset failure may include the environment, people, equipment, materials, and procedure. Before you carry out 5 whys RCA, you should decide which problems are immediate candidates for this root cause analysis method. Just a few examples of where root cause analysis is used include major accidents, everyday incidents, human errors, and manufacturing mistakes. Those that result in the highest costs to resolve, most downtime, or threats to safety will rise to the top of the list.
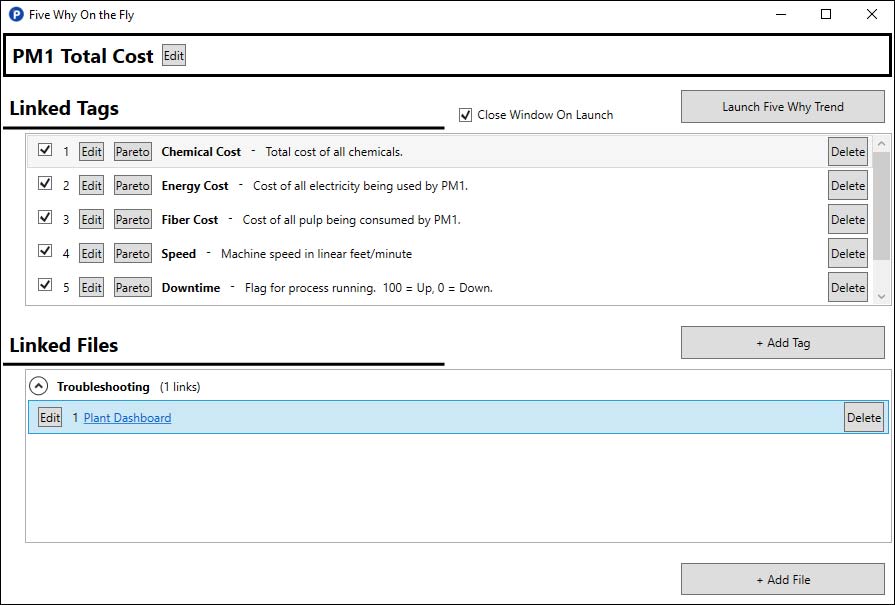
There are some software-based 5 whys analysis tools out there, like dataPARC’s PARCview, which automatically identifies potential the 5 top culprits of a process issue & links to trend data for deeper root cause analysis.
5 Whys Phase 1: Make an Exhaustive List of Every Possible Cause
The first thing to do in 5 whys is to list every potential cause leading up to a problem or event. At the same time, brainstorm everything that could possibly be related to the problem. In doing these steps you can create a history of what might have gone wrong and when.
You must remain neutral and focus only on the facts of the situation. Emotions and defensiveness must be minimized to have an effective list that you can start with. Stay neutral, open. Talk with people and look at records, logs and other fact keeping resources. Try to replay and reconstruct what you think happened when the problem occurred.
5 Whys Phase 2: Evidence, Fact and Data Seeking and Gathering
Phase 2 is the time when you get your hands on any possible data or files that can lead to the possible underlying causes of your problem. Checking data from your process data historian software is a great place to start. Other sources for this data may be databases, digital handwritten or printed files. In this phase the 5 whys list of at least 5 reasons comes into play and needs backup for each outcome or reason why that came up on your list.
5 Whys Phase 3: Identify What Contributed to the Problem
In Phase 3 all contributions to the problem are identified. List changes and events in the asset’s history. Evidence around the changes can be very helpful so gather this as you are able. Evidence can be broken down into four categories: paper, people, recording and physical evidence. Examples include paperwork specific to an activity, broken parts of the assets and video footage if you have it.
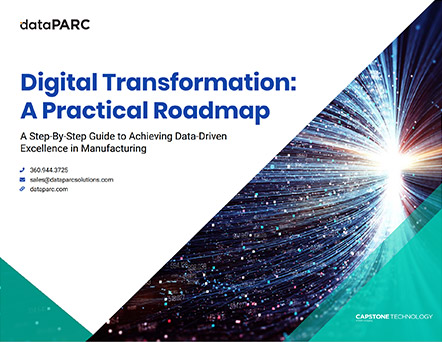
Integrating manufacturing data at your plant? Let our Digital Transformation Roadmap guide your way.
5 Whys Phase 4: Collect Data and Analyze It
In Phase 4, you should analyze the collected data. Data aggregation and trend performance can be a starting point. Organize changes or events by how much or little you can have an impact on the outcome. Then, decide if each event is unrelated, a correlating factor, a contributing factor, or a root cause. An unrelated event is one that has no impact or effect on the problem whatsoever. A correlating factor is one that is statistically related to the problem but may or may not have a direct impact on the problem.
A contributing factor is an event or condition that directly led to the problem, in full or in part. This should help you arrive at one or more one root causes. When the root cause has been identified, more questions can be asked. Why are you certain that this is the root cause of complex problems instead of something else?
5 Whys Phase 5: Preventing Future Breakdowns with Effective Countermeasures
The fifth phase of the 5 whys Root Cause Analysis is to prevent future breakdowns by creating a custom plan that includes countermeasures, which essentially address each of the 5 whys you identified in your team meeting. Preventive actions should also be identified. Your corrective actions should not only prevent the problem from happening again, but other problems should not be caused because of it. Ideally, a solid solution is one that is repeatable and can be used on other problems.
One of the most important things to determine is how the root cause of the problem can be eliminated. Root causes will, of course, vary just as much as people and assets do. Examples of eliminating the root cause of the issue are changes to preventive maintenance, improved operator training, new signage or HMI controls, or a change of parts or part suppliers.
In addition, be sure to identify any cost associated with the plan. How much was lost because of the problem, and how much it is going to cost to implement it.
To avoid and predict the potential for future problems, you should ask the team a few questions.
- What are the steps we must take to prevent the problem from reoccurring?
- Who will implement and how will the solution be implemented?
- Are any risks involved?
5 Whys Phase 6 – Implementation of your Plan
If you make it to this step, you have successfully completed 5 whys root cause analysis and have a solid plan for effective solutions.
Depending on the type, severity, and complexity of the problem and the plan to prevent it from happening again, there are several factors the team needs to think about before implementation occurs. These can include the people in charge of the assets, asset condition and status, processes related to the maintenance of the assets, and any people or processes outside of asset maintenance that have an impact on the identified problem. You would be surprised how much is involved with just one asset when you exhaustively think about it and make a list of all the people and actions involved during its useful life.
Implementing your plan should be well organized and orchestrated as well as documented. Follow-up meetings with your team should be scheduled to talk about what went well and what could be improved upon. With time, 5 whys can become an effective tool to both solve and prevent future problems at your plant.
Summing Up 5 Whys Root Cause Analysis for Manufacturing Success
Using the 5 Whys in manufacturing is critical because it helps teams identify and eliminate the root cause of recurring problems rather than just addressing surface-level symptoms. By drilling down into the cause of an issue, manufacturers can reduce downtime, improve efficiency, and prevent costly errors from happening again. This method promotes a proactive approach to problem-solving, fostering continuous improvement and operational excellence in a competitive manufacturing environment. The simplicity and effectiveness of the 5 Whys make it a powerful tool in the industry.
FAQ: 5 Whys Root Cause Analysis in Manufacturing
1. What is the 5 Whys method?
The 5 Whys is a simple yet powerful problem-solving technique used to identify the root cause of an issue by repeatedly asking “Why?” five times, typically until the underlying cause is revealed.
2. When should you use the 5 Whys analysis?
Use it when troubleshooting recurring issues, production slowdowns, quality defects, or unplanned downtime. It’s especially effective for problems that aren’t overly complex and where data is readily available.
3. Do you always have to ask “why” five times?
Not necessarily. Five is just a guideline. You may reach the root cause in three questions, or it might take six or more. The goal is to continue asking “why” until you’ve identified a cause that is actionable and within your control.
4. How is 5 Whys different from other root cause tools like fishbone diagrams or fault trees?
The 5 Whys is simpler and more direct. Fishbone diagrams and fault trees are better for complex problems with multiple contributing factors, while 5 Whys is ideal for quickly drilling down into a specific issue.
5. What’s an example of 5 Whys in manufacturing?
Example:
- Problem: A pump stopped working.
- Why? It overheated.
- Why? It wasn’t getting enough lubrication.
- Why? The lubrication line was blocked.
- Why? Debris got into the system.
- Why? A filter was missing during maintenance.
→ Root Cause: Maintenance procedures weren’t followed.
6. What are common mistakes when using 5 Whys?
Stopping too early, focusing on blame instead of process, and not validating each answer with data. It’s also important to involve the right people who understand the process and context.