The stages of digital transformation in the process industries is part of a global shift where technology reshapes our personal and professional lives. From early personal computers to advanced AI like ChatGPT, the digital landscape has evolved significantly. This blog explores how manufacturing, traditionally slower to adapt, can navigate the stages of digital transformation to improve data collection, visualization, and communication.
Digital transformation in the process industries is part of a larger Digital Transformation occurring across the globe – everyone and everything is a part of it in some way. In the 20th century, new technologies allowed for the ever-evolving computing machines. Now we depend upon so totally, we rarely give them a second thought.
Even before the advent of microprocessors and supercomputers, there were certain notable scientists and inventors who helped lay the groundwork for the technology that has since drastically reshaped every facet of modern life.
For many of us, it started with the first personal computers like the Commodore 64. Then e-mail, and our first mobile phones. From there, technology expanded to Amazon’s Alexa and Apple’s Siri, and the fast-evolving ChatGPT. We use our smartphones, which are essentially, portable mini-computers, to navigate so many areas of our lives. Similar concepts apply to our work lives. The digital environment has changed drastically in the past decades, but the manufacturing industry can be slower to change. This article focuses on the stages of digital transformation and how they relate to data collection, visualization, and communications in manufacturing.
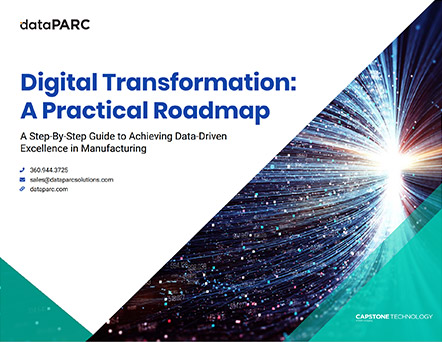
Working through digitization at your plant? Let our Digital Transformation Roadmap guide your way.
In the past few years, our customers in the process industries have become more aware of digital technology, and we are hearing more and more about their digital initiatives and journeys. In this awareness, there has been confusion with terms like Industry 4.0 and IIoT. These two concepts in particular can create confusion.
The first is a perception that these are new technologies, when in fact many of the technologies have been around for decades. Even the fundamental problem of data accessibility is not new. What is new are the people, enablers, or catalysts. Such as reduced cost and wireless technology, but the fundamental concept of collecting data to make better decisions has been around for decades.
The second issue is the association of technology (i.e. products) to a broad theme like IIOT or Industry 4.0. This broad theme to the classic trap of solutions looking for problems to solve. Regardless of the situation, first, you must start with a challenge and find the proper solution, if you reach for a technology or solution without a clear purpose it will not stick or be worth the investment.
The reality of the digital world is that there are huge opportunities and everyone is trying to figure out the right solutions. Engaging terminology is one way to convey messages in a way people will notice and remember. IIOT and Industry 4.0 are examples of this terminology.
What is Digital Transforamtion?
Digital transformation in manufacturing and process industries refers to the comprehensive integration of digital technologies into every aspect of business operations. This transformation fundamentally alters how companies function and deliver value to their customers, going beyond merely automating existing business processes to rethinking and redesigning them for maximum advantage. In these industries, digital transformation manifests in several impactful ways.
Operational efficiency is significantly improved as digital tools streamline operations, reduce downtime, and increase productivity across entire process. Real-time monitoring and control systems allow for more responsive and agile manufacturing processes, ensuring smooth and efficient production.
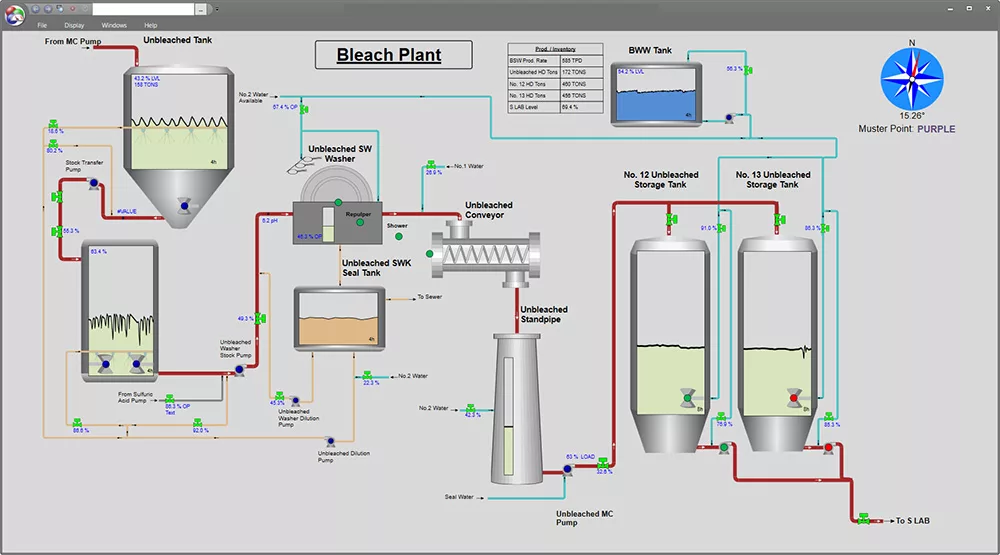
With digital transformation, companies can achieve real-time monitoring and control systems, enabling more responsive and agile manufacturing processes for smooth and efficient production.
Additionally, digital platforms enhance collaboration across departments and with external partners, ensuring seamless information flow, better coordination, more customer experience and faster decision-making. With the right tools, embracing such digital transformation strategies in internal processes can increase efficiency and help an organization stay competitive.
In summary, digital transformation in manufacturing and process industries is essential for making informed decisions, staying competitive, and creating new value propositions. It ensures that companies can remain competitive, relevant, and thrive in an increasingly digital and connected world.
How dataPARC Views Digital Transformation
Digital Transformation is a term that resonates. The term implies that the journey of becoming digital is not binary. There are no digital or non-digital companies; we are all on a digital spectrum.
At dataPARC, we like to take this one step further and identify 5 stages of digital transformation in the process industries. Every organization falls into one of these categories. Assigning transformation categories provides a framework to define the broad challenges for each manufacturer and present the best path forward in their digital transformation journey. Perhaps you can see yourself and your plant in one of the stages.
On the road to digital transformation? Get our Free Digital Transformation Roadmap, a step-by-step guide to achieving data-driven excellence in manufacturing.
Stage 1: No Time, No Data
Stage one is an early stage. If you are in stage one you likely utilize manual operations and have a limited or no PLC or DCS.
In stage one of manufacturing digital transformation, facilities are still looking to modernize their control systems from analog to digital. There are opportunities at this end, but the primary focus should be identifying the right solutions (PLC upgrades, additional sensors/instruments, etc.) and topics like AR (Augmented Reality) and ML (Machine Learning) should be a longer-term vision.
Key Considerations
- What small changes can you make to digitize operations? Can you easily add sensors? Talk with your team about how that can be done.
- How can you convert manual to digital data? What sources of data do you have? Create a plan, internally and or using vendor help, to digitize your data.
- What is your budget for purchasing or upgrading equipment? Has your budget changed since COVID? Decide what resources are available.
Stage 2: Some Data, Little Time
If you are in stage two, your digital efforts are just getting off the ground. Your plant has a PLC or DCS, but does not have a historian. You also likely still have many functions that require manual data.
One of the best ways to optimize your operations at stage 2 of your digital transformation process is to add a historian.
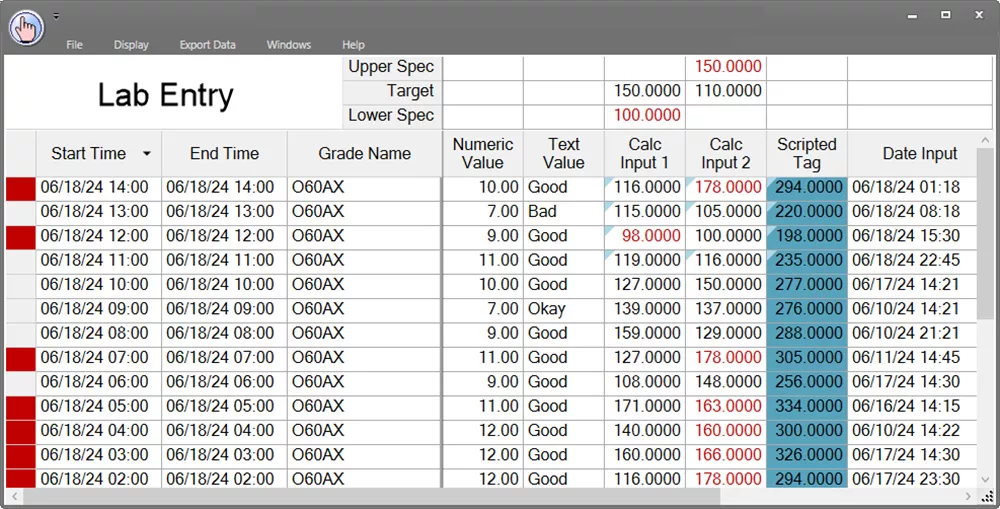
Manual data entry screen showing numeric, text, and calculated cells, emphasizing that with the right digital tools, even complex data can be managed efficiently and with minimal time investment.
Key Considerations
- What are your company’s internal resources and how can you leverage them? What are the financial and personnel resources you can use to advance your operations forward?
- Are there areas of the plant that can be automated quickly? What parts of the plant will be easily automated and what areas will pose more challenges? Decide and come up with a plan.
- How will new systems integrate in the future? Consider new systems you may implement later. How will these systems integrate will current solutions? Will they be completely replaced or complement current systems?
Stage 3: Reflective Decision-Making
In stage 3, things are really starting to transform digitally. Stage 3 is where the IT/OT convergence begins to take place.
At this stage, your plant may be ready from a cultural standpoint but lacks the software tools. You may have a small historian that is not heavily used or other homegrown tools, but you are able to see the vision of what is needed to go forward
Key Considerations
- Where does your plant aspire to be from an IT perspective? Think about where you ultimately want to be digitally and create a plan.
- Will you take on this work internally or engage vendors? Can your team handle the tasks internally or will you need to research and engage vendors?
- Will legacy systems be replaced or leveraged? Will the systems you currently use still be relevant or need to be completely replaced?
- Will the selected solutions bridge existing systems or require a rip and replace approach? Are your current solutions complementary to new ones or will they become obsolete?
Stage 4: Data-Driven Culture
Beginning to digitize harmoniously describes stage four. At stage four, your plant is mature in its use of data. You have a historian with most of the data coming in. You likely have a variety of systems for LIMS, manual data, etc. The culture is there to embrace data for decision-making, but the site lacks the right software to bring the data together.
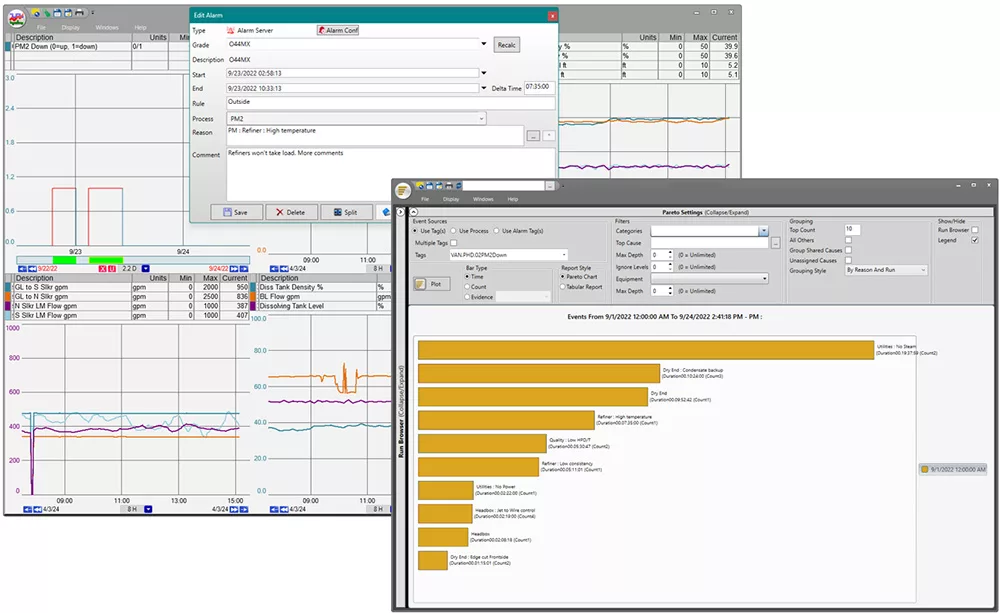
Manufacturing Process Optimization Software enables recording downtime for use in analysis in continuous improvement and driving a data-driven culture for enhanced efficiency.
If you are in stage 4, the core digital systems are in place. Combining data sources within the plant and across the enterprise is key. Culture change is also very important. Standardization and collaboration across the entire organization and enterprise ensures consistent and accurate data sharing.
Key Considerations
- How will your company handle multiple system standards? As you start to incorporate multiple sites, one must decide how to handle situations where there are multiple systems standards used. For example, half of the plants have the OSI PI Historian, and the other half have the Aspen IP.21 data Historian. Your company can migrate everything to a common Historian vendor, which could be a lot of work and has significant risk.
- How will you integrate data from multiple sites? A company could choose to implement centralized data systems, like a single enterprise-wide historian. The advantage of Enterprise-wide data is that the data is more easily accessible. The tradeoff could be application performance when accessing data across the Intranet or Internet, depending on the chosen technology. Another option is to select data analysis applications that can easily connect to the existing infrastructure. This option has the advantage of leveraging existing investments, having the least effort to get started, and delivers the best performance to the local plant site. One downside is that data integrity issues between sites could exist, and a lot of work may be required to process the data before performing analysis. There is also a 3rd option that provides a hybrid approach and looks to achieve the best of the previous two.
Stage 5: Data Is In Your DNA
If you are in stage 5, you are in a very sophisticated plant that has a well-developed strategy for data and decision support. You have settled on one major historian and have spent a lot of time and effort to transfer all data from other sources (LIMS, MES, ERP, etc.) into the historian and have a number of business systems pulling from the historian.
Organizations at Stage 5 are ready, from both an infrastructure and cultural perspective, for advanced topics like AR & ML. In stage 5 there should be continued use of Advanced data modeling and analytics and there may be opportunities for application consolidation.
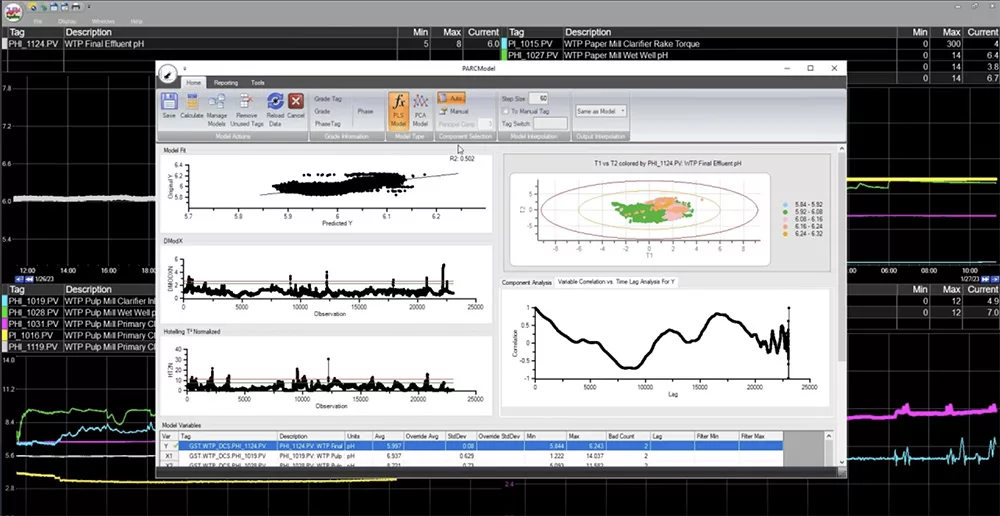
Using a soft sensor and PLS model to drive production, this modeling display screen demonstrates how data becomes the DNA of your operations, crucial for optimizing processes.
Key Considerations
- Are there key sources of data still missing from the Historian? Check all your sources of data and make sure they are connected to the historian. Is there a source you are overlooking?
- Have your business requirements changed or evolved and how does your data platform fit into this? What has changed in your business? Make sure that the solution you chose to digitize and manage your data is accomplishing your goals.
- Are all the key user groups getting what they need? People needing data within a plant can range from operator to engineer to plant manager. Are all roles getting the data they need in the way they need it?
On the road to digital transformation? Get our Free Digital Transformation Roadmap, a step-by-step guide to achieving data-driven excellence in manufacturing.
Challenges Faced with Digital Transformation
In manufacturing, creating a digital transformation strategy can address several significant challenges. However, as mentioned earlier, you don’t want to go after setting digital transformation initiatives without a challenge to correct in mind. Here are a few key challenges and how digital transformation improves these scenarios:
Data Silos and Poor Collaboration:
Departments often work in isolation, leading to data silos and poor collaboration, which hampers decision-making and overall efficiency.
Solution: Data silos can be challenging to elimelate at times, and can persistent even after stage two or three. It is important to have a culture of data to help contunie to break down silos as they occur. Robust data visualization platforms break down these silos by integrating data across the organization. Enhanced collaboration tools and centralized data repositories ensure seamless information flow, better coordination, and faster, more informed decision-making.
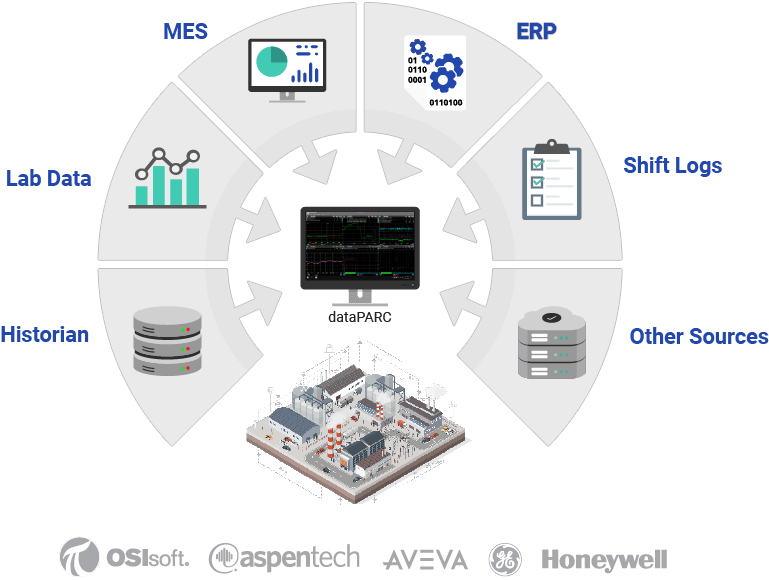
dataPARC is a powerful manufacturing data integration platform, seamlessly connecting historians, lab data, MES, ERP, shift logs, and more for comprehensive and efficient data management.
Operational Inefficiencies:
Traditional manufacturing processes often suffer from inefficiencies due to manual interventions, outdated machinery, and a lack of real-time data like relying on DCS screens.
Solution: Data historians and visualization system introduces advanced analytics and real-time monitoring, allowing companies to optimize operations, reduce downtime, and enhance productivity. Once the basics are established sites can go beyond to predictive maintenance powered by AI and foresee equipment failures before they occur, ensuring smoother and more efficient production processes.
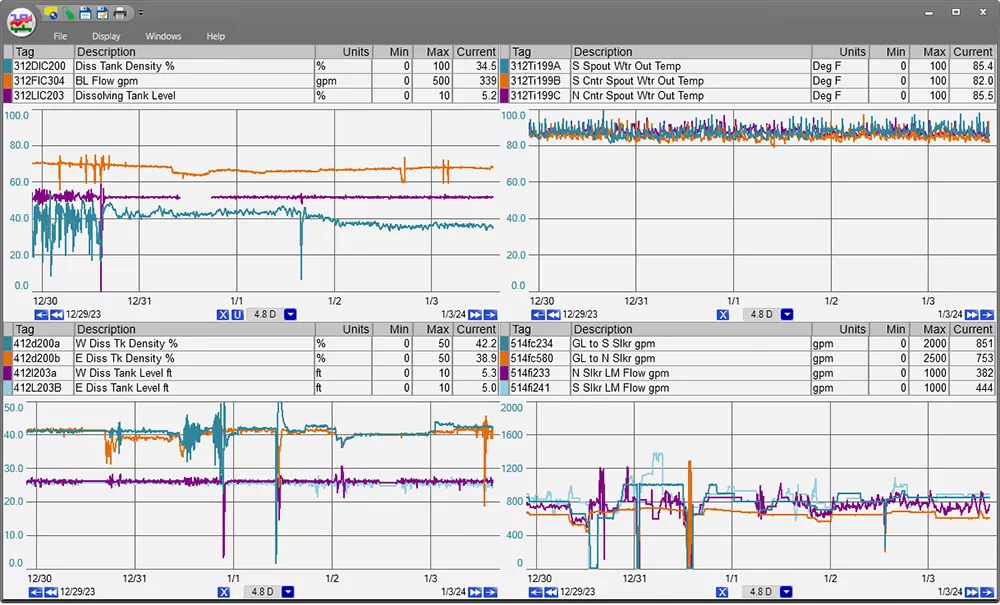
Upgrading from DCS screens to a multi-trend display allows you to monitor hundreds of tags simultaneously, significantly reducing operational inefficiencies.
Quality Control:
Maintaining consistent product quality can be difficult due to variability in raw materials, human error, and inadequate monitoring systems.
Solution: Moving away from paper records, or Excel spreadsheets gives time back to lab techs and operators. They can monitor and control quality parameters in real-time. Not to mention the limits and values are accessible and backed up in a database.
Regulatory Compliance:
Keeping up with stringent regulatory requirements and ensuring compliance can be time-consuming and costly.
Solution: Digital technologies such as data historians collect and store data while analytics software can assist with monitoring and reporting of important compliance metrics. There are automated systems that alert and report emissions, energy consumption, and other critical parameters, ensuring adherence to regulations and reducing the risk of non-compliance.
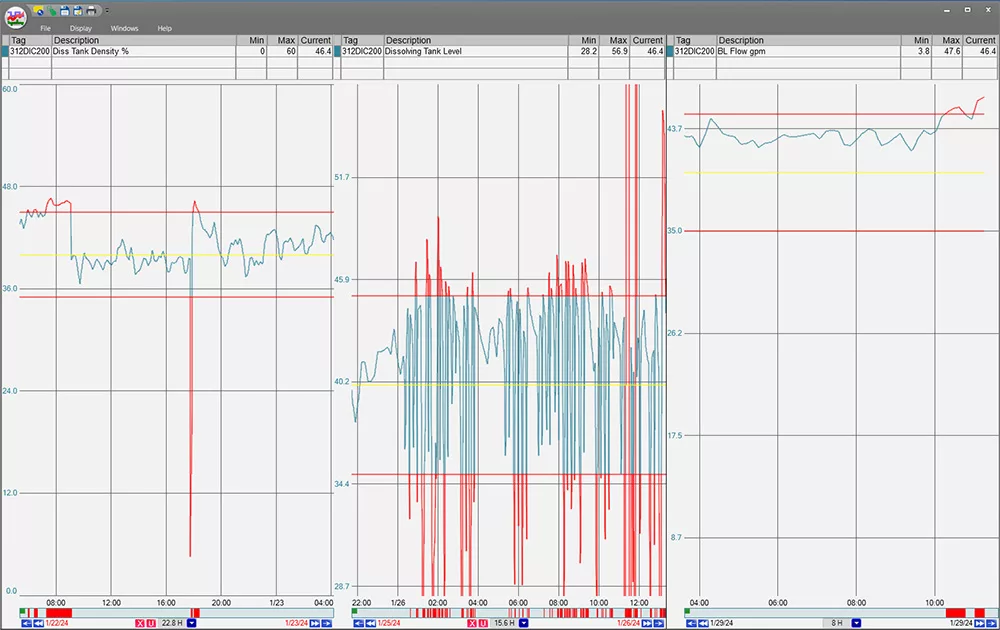
Integrated alarms alert users when values are out of spec, ensuring continuous awareness and compliance.
By addressing these challenges, digital transformation empowers process industries to enhance operational efficiency, ensure quality, foster collaboration, maintain compliance, and achieve sustainability goals, ultimately driving growth and competitiveness in a rapidly evolving landscape.
Looking Forward to Successful Digital Transformation Strategy
Digital transformation in any form can make a large impact on your business. Whether it is a small change such as inexpensive sensors or a large enterprise-wide application, digital transformation in the process industries enables organizations to operate more consistently and efficiently resulting in less downtime and greater profitability.