IIT/OT Convergence and corresponding buzzwords are all over the place. If you are in manufacturing, chances are you have seen ads and read articles like this one on the necessity of keeping up with the ever-changing digital landscape. No matter what the source, important data needs to get to the right people at the right time, so where does one start?
In a plant or industrial operations, chances are you have many sources of IT and OT data that contribute to seamless operations. Whether it is an oil & gas, food, chemical or mineral process, on the ideal days, your operation runs like a well- oiled machine. That being said, how easily and consistently can the entire plant or enterprise operate efficiently, solve problems and reduce bottlenecks? Are you taking the right steps toward manufacturing digital tranformantion for your plant?
Accurate and fast data access, intuitive data visualization, predictive maintenance and analytics are needed to make decisions that affect production on a 24/7 basis. Resources are also at risk when changes are made, even if they are for the better. Ripping and replacing data systems and equipment is expensive and involves a lot of risk.
No matter what the source, important data needs to get to the right people at the right time, so where does one start to make small, gradual IT/OT changes?
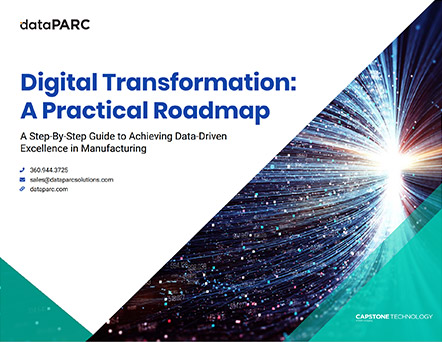
Integrating IT & OT data at your plant? Let our Digital Transformation Roadmap guide your way.
Leverage Existing IT/OT Tools and Integrate New Solutions for Seamless Convergence
Firstly, you can leverage the data assets you already have. Risk is reduced considerably when you add on products that enhance data sources you’re already using.
For example, if you utilize a data historian that works well for your needs, you can easily integrate data visualization and analytics solutions on top, as well as connect other sources that were previously siloed. Not replacing the historian saves time and avoids production interruptions, while allowing you to maintain operational continuity. This approach saves valuable financial resources that can be allocated to other needs, accelerates ROI, and reduces overall risk.
Technology: Key Enablers of IT/OT Convergence
Specific technologies are crucial to facilitating the convergence of IT and OT systems. Data historians, as mentioned, play a central role by collecting and storing real-time data from operational systems, making it accessible for advanced analytics and decision-making. Integration platforms, such as middleware or IoT gateways, allow seamless communication between disparate IT and OT systems, bridging the gap between shop-floor operations and business-level software like ERP systems.
Additionally, technologies such as edge computing, cloud platforms, and IIoT (Industrial Internet of Things) solutions provide the infrastructure for processing and analyzing data closer to where it’s generated. Edge devices can handle data locally, reducing latency and bandwidth requirements, while cloud services enable scalable data storage and long-term analysis.
Meanwhile, cybersecurity solutions tailored to OT environments help ensure that data shared between IT and OT systems remains secure, reducing the risks of cyber threats that come with increased connectivity between physical devices.
Digital transformation in process industires in necessary to stay competivite. By incorporating these advanced technologies into production processes, manufacturers can achieve greater visibility, flexibility, and efficiency across their operations, fully realizing the benefits of IT/OT convergence.
Case Study: IT/OT Convergence at Engery Transfer
Check out Enery Transfers digital transformation journey.
An example of a company that utilized current tools and enhanced their operations with new ones was Energy Transfer, a midstream energy company headquartered in Houston, Texas. Energy Transfer had an enormous amount of data at their 477 sites and 90k miles of pipeline. The company has acquired assets over the years, resulting in multiple vendor data systems across the Enterprise, and did not have a good way to share it.
Engineers and management both needed data from all sites but couldn’t make operational decisions before the window of opportunity had passed. They also knew future acquisitions with different data systems might come, so a flexible future was critical. Energy Transfer purchased a reliable data visualization and analytics software solution and was then able to combine data from all sites with just one program.
Not only was the data easily available, but the tools enabled the data to be customized to the way that everyone- from operator to engineer to management- wanted to see it. Sites could customize and access data they specifically needed, while corporate headquarters could access data they wanted and customize it to their specific needs. By joining their OT and IT worlds in a future-proof manner, Energy Transfer not only improved efficiency but they saved time and money while doing it to the tune of $10M in annualized savings.
On the road to digital transformation? Get our Free Digital Transformation Roadmap, a step-by-step guide to achieving data-driven excellence in manufacturing.
Begin IT/OT Integration with Small Steps and Team Collaboration
Another step you can take is to get your people on the same page about digitizing as many processes and data as you can at your plant. This means small steps such as LIMS data and process data being shared digitally rather than manually through eliminating time-consuming methods such as handwritten reports and manually entered excel spreadsheets.
Manual processes create delays and perpetuate data silos as they are only available to those who receive them through arduous, dated methods. A reliable data visualization and analytics software can help you do this, allowing you to share the data seamlessly. The small things can add up to the big things in IT/OT convergence. Getting the team into a digital mindset is an important step.
Starting with a team to talk about IT/OT convergence is a wise first step. Formulating a plan with goals, milestones and deadlines helps make the process more bite sized and manageable. Defining roles, assigning tasks and meeting about progress are effective ways of incorporating your IT/OT data into your manufacturing process and reporting.
Case Study: W.R. Grace’s Success with IT/OT Convergence
Read about the Catalyzing IT/OT Convergence with W.R. Grace
An example of a company that started small and soon widely adopted IT/OT convergence was W.R. Grace, a $2 billion specialty chemical company that manufactures a wide array of chemicals and is the world’s leading supplier of FCC catalyst and additives. Grace has manufacturing locations on three continents and sells to over 60 countries and is headquartered in Columbia, Maryland. Grace’s IT and OT worlds were very disconnected.
Grace had robust OT and IT data but their operational technology was limited in the way they could use this data. Most Grace staff were required to use the operator control system functions to interact with process data because the existing historian tools were ineffective, slow, and not intuitive, resulting in no buy-in, especially from operations staff.
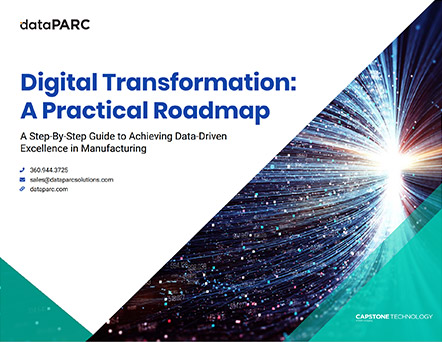
Integrating IT & OT data at your plant? Let our Digital Transformation Roadmap guide your way.
Grace implemented a data visualization solution across several of its chemical facilities, including its largest facility, Curtis Bay, with over 600 employees. The site unified key sources of data with a robust data visualization and analytics product.
Grace employed intuitive, fast and effective dashboards, unifying operations and information technologies and thereby increasing process management effectiveness, decreasing downtime and increasing profitability. These dashboards were easy to use and highly intuitive, and in turn they got utilized by many staff who were hesitant to engage the previous system. Grace saw an ROI from the implementation of data visualization software tools in less than six months.
Using the data visualization & analytics tools also allowed Grace to make predictive and proactive changes in their operations resulting in increased first pass product quality.

Simplify IT/OT Convergence in Manufacturing with Effective Data Visualization and Analytics
If you lack high performing data visualization and analytics across your plant or enterprise, achieving IT/OT convergence in manufacturing is relatively simple when you employ the right resources and have a plan that allows for gradual changes that add up to significant results. Small changes such as combining existing systems, effective software tools and a mindset of proactive digital awareness for your team can significantly impact the overall success of your manufacturing operations.
Newfound ease in your daily tasks and reporting are results of effective IT/OT convergence and will be experienced by everyone. From the operator to the engineer all the way to corporate management, small changes become major impacts when completed strategically and as part of an effective plan for positive digital progress.
Challenges and Solutions in IT/OT Convergence
Challenge 1: Cultural and Organizational Silos
One of the biggest challenges in IT/OT convergence is the cultural divide between IT and OT teams. IT departments are typically focused on data security, scalability, and network management, while OT teams prioritize operational efficiency, equipment reliability, and uptime. These differing priorities can create friction and slow down convergence efforts.
Solution:
Bridging this gap starts with fostering collaboration and communication between IT and OT teams. Establishing cross-functional teams that include both IT and OT personnel helps ensure that both perspectives are considered in decision-making. Providing training on each other’s priorities and technologies can also foster mutual understanding, helping to align goals and ease the transition toward convergence.
Challenge 2: Legacy Systems and Infrastructure Compatibility
Many manufacturing environments rely on legacy OT systems that were not designed to interface with modern IT systems. These older technologies can present compatibility issues when trying to integrate them with newer IT infrastructure, which can delay or complicate convergence efforts.
Solution:
Rather than completely replacing legacy systems, consider using middleware, edge computing devices, or integration platforms to bridge the gap between old and new systems. These technologies can facilitate communication between incompatible systems without disrupting current operations. Additionally, adopting a phased approach to integration allows for gradual modernization manufacturing execution systems, reducing the risk of operational disruptions.
Challenge 3: Cybersecurity Risks
As IT and OT systems become more connected, the attack surface for potential cyber threats expands. OT systems that were once isolated are now exposed to new vulnerabilities, which can put critical infrastructure and operational systems at risk if not properly secured.
Solution:
To address cybersecurity concerns, implement a robust security framework that includes both IT and OT considerations. This for security concerns may involve segmenting networks, deploying firewalls, and using intrusion detection systems (IDS) to monitor OT networks. Conducting regular cybersecurity assessments and adopting best practices like multi-factor authentication, encrypted communications, and patch management ensures that both IT and OT systems are well protected from threats.
Challenge 4: Data Integration and Standardization
Integrating data from multiple sources—especially when they use different formats, protocols, or communication standards—can be a daunting challenge in IT/OT convergence. Without proper data standardization, it becomes difficult to perform meaningful analysis or create a unified view of operations.
Solution:
Utilize data integration platforms or middleware to aggregate data from various sources into a standardized format. Many of these platforms are designed to handle different communication protocols and data formats, making it easier to harmonize data from diverse systems. Additionally, adopting industry standards for data management and interoperability (such as OPC-UA) can help streamline the integration process and ensure data consistency across the enterprise.

dataPARC is a robust manufacturing data integration platform.
Challenge 5: Scalability of Solutions
As the number of connected devices and data streams increases, managing the scalability of IT/OT solutions becomes a critical challenge. Ensuring that systems can handle future growth without requiring constant overhauls is key to long-term success.
Solution:
To ensure scalability, invest in flexible, cloud-based or hybrid solutions that can expand as your data and infrastructure needs grow. Cloud platforms offer virtually limitless scalability, while edge computing enables local processing to reduce strain on centralized systems. Modular architecture and flexible integration tools also allow for incremental upgrades, preventing the need for large-scale system replacements down the road.
Conclusion: Unlock the Full Potential of IT/OT Convergence
IT/OT convergence is no longer just a forward-thinking strategy for manufacturing companies; it’s a critical step for manufacturers seeking to optimize operations, improve decision-making, and stay competitive in an increasingly data-driven landscape. By addressing common challenges—such as organizational silos, legacy system compatibility, and cybersecurity risks—and leveraging the right technologies, businesses can achieve a seamless integration that enhances both productivity and profitability.
While the journey may seem complex, the long-term benefits far outweigh the challenges. Improved operational visibility, enhanced collaboration, and faster response times are just some of the rewards that come with successfully merging IT and OT systems. Now is the time to assess your current infrastructure, identify areas for improvement, and begin taking incremental steps toward convergence.
The key to success lies in choosing the right tools and fostering collaboration across teams. By doing so, you’ll unlock the full potential of IT/OT convergence and position your organization for continued success in the evolving industrial landscape.