The purpose of process control alarms is to use automation to assist operators as they monitor and control processes, and alert them to abnormal situations. Proper process alarm and management of alarm systems requires careful planning. It has a significant impact on the overall effectiveness of a control system.
Incoming process signals are continuously monitored, and if the value of a given signal moves into an abnormal range. Then, a visual and/or audio alarm notifies the operator of that condition. This seems like a simple concept, almost not worthy of a second thought. Unfortunately, sometimes the configuration of alarms in a control system doesn’t get the attention it deserves.
In this post we’ll talk about the history of process alarms in manufacturing, and discuss best practices for configuring alarms for effective process control.
Early Process Alarm Management
Before digital process control, each alarm indicator required a dedicated lamp and some physical wiring. This meant that:
- Due to the effort required, the need for a given alarm was carefully scrutinized, somewhat limiting the total number of alarms
- Once the alarm was in place, it had a permanent “home” where an operator could become comfortable with its location and meaning
The Introduction of Digital Alarm Systems
As control systems became digital, the creation and presentation of alarms changed significantly. First, a “traditional” control panel was many square feet in size. Now, digital control system human machine interfaces (HMIs) consisted of a few computer monitors. They display a representation of the process in an area more appropriately measured in square inches than square feet.
Second, creating an alarm event was a simple matter of reconfiguring some software. Multiple levels of alarms (hi & hi-hi, lo & lo-lo) could easily be assigned to a single process value. This led to an increase in the number of possible process alarm notifications.
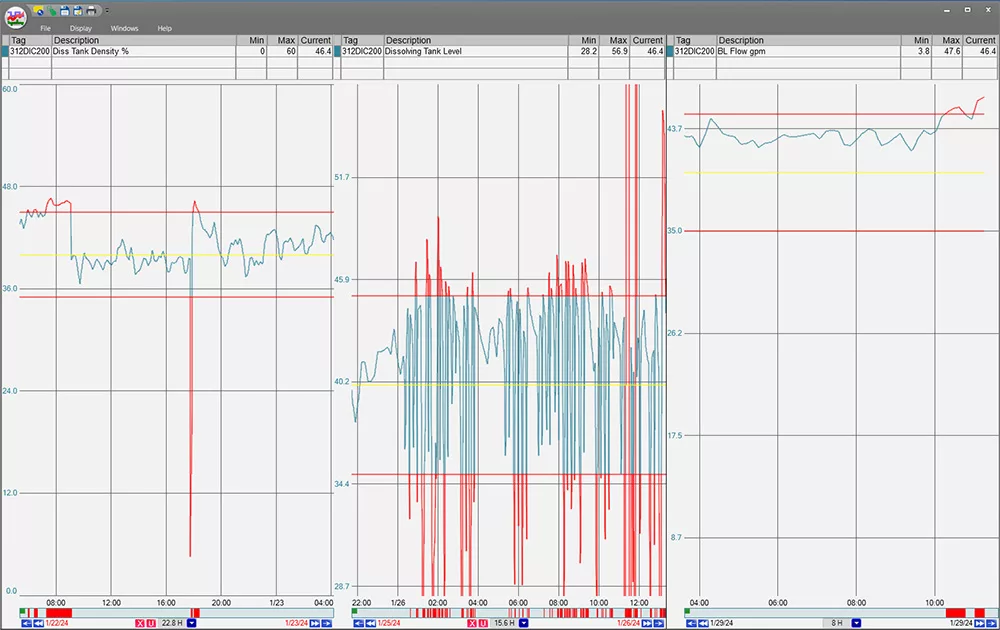
This multi-trend display shows how there is still usecases for simple hi/lo alarming. Each trend visualizes set limits. Turning red when values exceed thresholds, how now you can interac with advacned features and real-time monitoring.
Finally, when an alarm was activated, it was presented as an icon, or as flashing text on a process schematic screen. Then, logged in a dedicated alarm list somewhere within the large collection of display screens. However, when the alarm was presented, it lacked the consistency of location and intuitive meaning that the traditional physical lamp had.
The Dilemma With Digital Alarms
The digital and alarm handling systems worked acceptably well for single alarms and minor upsets. But for major upsets the limited visual real estate and the need to read and mentally place each alarm created bottlenecks to acknowledging and properly responding to large numbers of alarms in a short interval of time.
If a critical component in a process fails, for example a lubrication pump on a large induction fan. The result can be a “flood” of alarms occurring over a short time period. The first wave of alarm flood of alarms is associated with the immediate failure. Low lube oil pressure, low lube oil flow, and high bearing temperatures.
The second wave is associated with interlocks shutting down the fan. High inlet pressure, low air flow and low downstream pressure. With no ID fan the upstream boiler will soon start to shut down and generate numerous alarms. This is followed by problems from the process or processes which are served by the boiler.
The ASM Consortium – Abnormal Situration Management
Analyses of a number of serious industrial accidents has shown that a major contributor to the severity of the accidents was an overwhelming number of alarms. Operators were not capable of understanding and properly responding to in a timely manner.
As a result of these findings, in 1992 a consortium of companies, including Honeywell and several petroleum and chemical manufacturers, was established to study the issue of alarm management. More generally, abnormal situation alarm management philosophy.
The ASM Consortium, with funding from the National Institute of Standards and Technology. They researched and developed a series of documents on operator situation awareness, operator effectiveness and alarm management. Since then, a number of other industry groups and professional organizations, such as the Engineering Equipment and Materials Users Association in the UK and Instrument Society of America have also examined the issue of alarm management and issued best practices papers.
Exploring process controls? Easily implement online SPC/SQC utilizing dataPARC’s integrated limit management tools and alarm/event engine.
Process Alarm Systems Management: Alarm Philosophy Best Practices
The central message of these process alarm management best practices documents is that the alarm portion of a digital control system should be put together with as much care and design as the rest of the control system.
It is inadequate to simply assign a high and low limit to each incoming process variable and call it good. There are a number of practices that can improve the usability and effectiveness of an alarm system. Some techniques are rather simple to implement, while others are more complex and require more effort.
1. Planning
When designing or evaluating an existing system, start by looking at each alarm. Evaluate whether it is really needed, and is it set correctly. For example, a pump motor may have an alarm that sounds if the motor trips out.
However, if there is also a flow sensor downstream of the pump which has an alarm on it, if the pump stops, two alarms will register. Since the real effect on the process is a loss of flow. It makes sense to keep that alarm and eliminate the motor-trip alarm.
2. Prioritization
Alarms should be prioritized. Some alarms are safety related alarm priorities and should be presented to the operator in a manner that emphasizes their importance. High priority alarms should be presented in a fixed location on a dedicated alarm display.
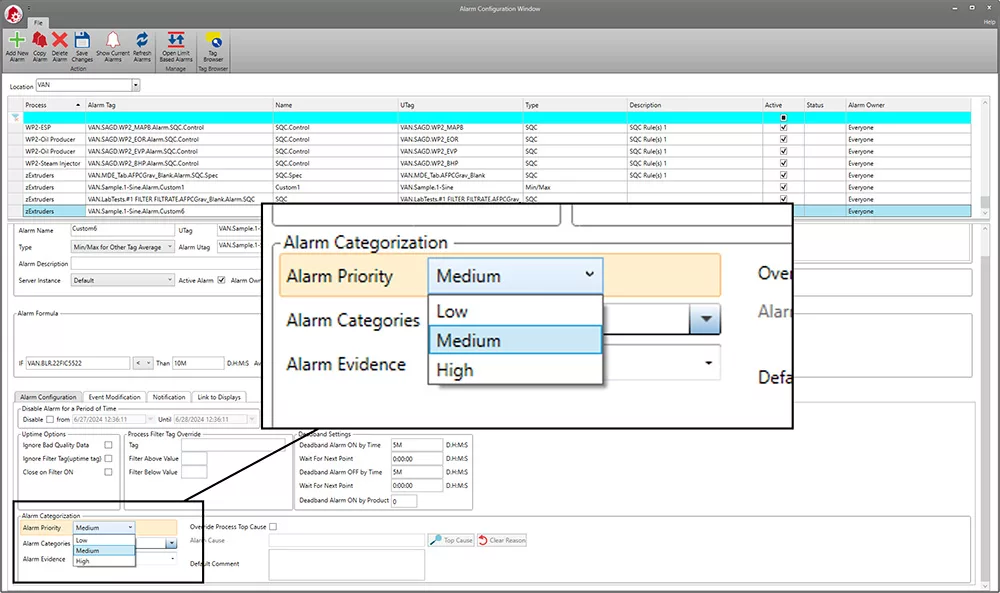
This alarm configuration screen highlights the priority section, showcasing Low, Medium, and High priority settings. Ensuring your alarm management software includes these options is crucial for effective alarm prioritization and response.
This allows operators to immediately recognize them and react in critical situations. It is very difficult to read, understand and quickly react to an alarm which is presented only in a scrolling list of alarms which will be continuously growing during a process upset.
The reduced speed category captures the losses of running below the target (maximum) speed. For information about using the right speed target in the performance factor calculation read 6 Keys to Successful OEE Implementation.
3. Grouping & Suppression
Correctly identifying the required alarms and prioritizing them is a help, but these techniques alone will not stop a surge of alarms during a crisis. In order to significantly reduce the number of presented crisis alarms, methods like alarm grouping and alarm suppression are needed.
As mentioned in the ID fan example above, a single point of failure can lead to several abnormal process conditions and thus several alarms.
It is possible to anticipate these patterns and create control logic which handles the situation more elegantly. In the case of the ID fan, if the inlet pressure to the fan goes high and the outlet flow drops it makes sense to present the operator with a virtual alarm of “Fan down” rather than a dozen individual alarms, all presented within seconds of each other, and too many alarms that he or she has to deal with. While the operator is trying to comprehend a cluster of individual alarms to deduce that the fan is down, the upstream boiler may trip out.
Hopefully, with a single concise alarm of a lost fan, the operator can take action at the boiler and perhaps keep that unit running at reduced rate until the fan can be restored. All alarms are still registered by the system for diagnosis and troubleshooting, but only condensed, pertinent information is presented to the operator.
This type of grouping and suppression can be done manually as well. If there is a process unit that is sometimes taken offline or bypassed, it makes sense to group and suppress all of the alarms associated with that unit’s operation. An operator shouldn’t have to continuously acknowledge a low flow alarm on a line that he knows has no flow in it.
4. Human Administration
Perhaps the most important part of alarm management is the actual human administration of the system. However a system is designed, its intent and use needs to be clearly communicated to the operators which use the system.
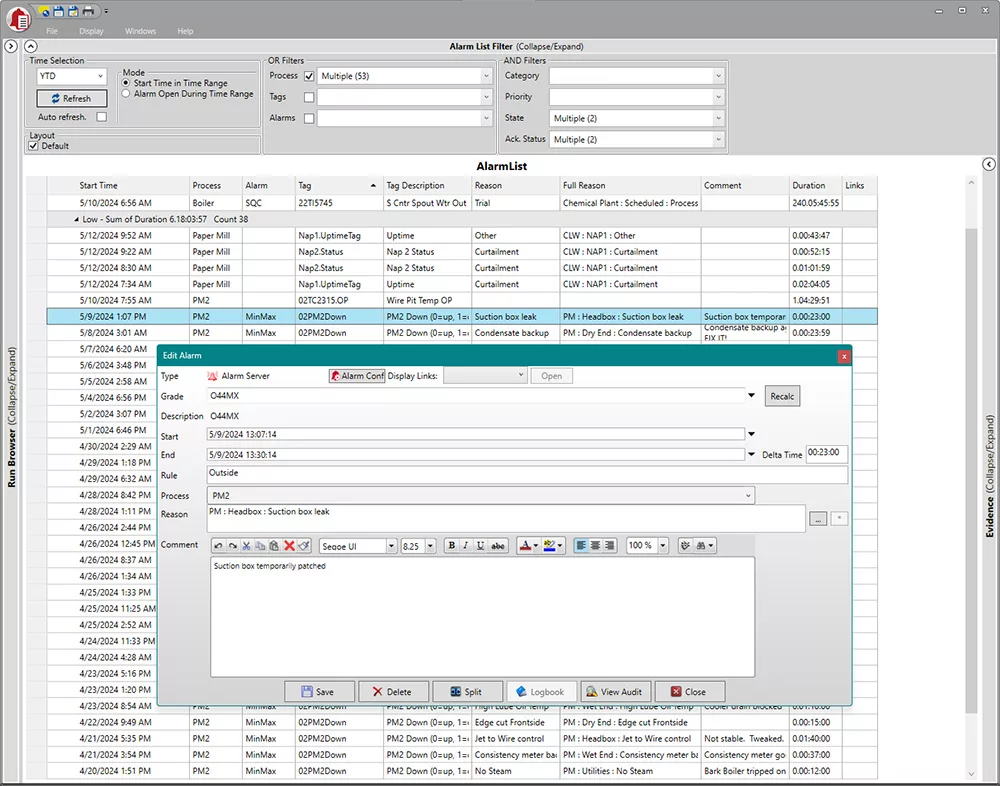
An alarm list or other type of display will allow users to view current and past alarms based on priority, with an acknowledgment section for users to assign reasons or comments. This feature enhances human administration by enabling effective tracking and management of alarm responses.
Training operators on how to use and respond to alarms is as important to safety instrumented systems as good original system design. Process alarm management is a dynamic endeavor, and as operators use the system they will have feedback which will lead to design improvements.
The system should be periodically audited to look for points of failure and areas of improvement. As processes change, the alarm configuration will also need to be changed. This ongoing attention to the alarm system will make it more robust and yield a system that will avert serious process-related incidents.
5. Regular Review and Updating
Regularly reviewing and updating your alarm system is crucial for maintaining its effectiveness and ensuring that it adapts to changing process conditions. This involves continuously evaluating the performance of alarms. As well as identifying any issues, and making necessary adjustments to improve reliability and response times. By doing so, you can prevent alarm fatigue. This can be caused by frequent nuisance alarms and ensure that critical alarms receive the attention they need.
Additionally, as processes and technologies evolve, the relevance and priority of alarms may change. Regular updates allow you to incorporate new safety standards, operational procedures, and technological advancements into your alarm system. This proactive approach helps maintain compliance with industry regulations. It ensures that the alarm system continues to support optimal plant performance and safety. It also helps keep the alarm counts to a reasonable number and not get overwhelming.
Implementing a review process, such as periodic audits and performance assessments, can help identify areas for improvement. Involving a cross-functional team in these reviews ensures that different perspectives are considered. It will help achieve a more comprehensive and effective alarm management strategy.
Looking Ahead: Alarm Management
Configuring and maintaining process alarms properly requires careful planning and has a significant impact on the overall effectiveness of a control system. Process alarm management best practices dictate that the alarm portion of a digital control system should be put together with as much care and design as the rest of the control system.

Looking forward, enhancing your site’s alarm management will significantly improve troubleshooting and root cause analysis. With recorded data, you can create Pareto charts and other tools to effectively identify and reduce downtime.
Alarm System FAQs
What are a few advanced alarm management techniques we should implement to improve our overall alarm management life cycle?
Implementing advanced alarm management techniques is crucial for addressing ineffective alarm management and enhancing overall efficiency. Here are a few techniques to consider:
- Dynamic Alarm Rationalization: Regularly review and adjust alarm settings based on process changes and historical data to minimize nuisance alarms and maintain good alarm management practices.
- Alarm Prioritization: Use alarm management software to categorize alarms by severity and impact, ensuring that critical alarms receive immediate attention.
- Alarm Analytics: Leverage advanced analytics to identify patterns and root causes of frequent alarms, enabling targeted improvements and more effective alarm management.
What are the business impacts of poor alarm management?
Poor alarm management can lead to major industrial incidents, significantly reducing process safety and increasing the likelihood of operational inefficiency. When alarms are not effectively managed, operators may become overwhelmed or desensitized to alarms, potentially missing critical warnings.
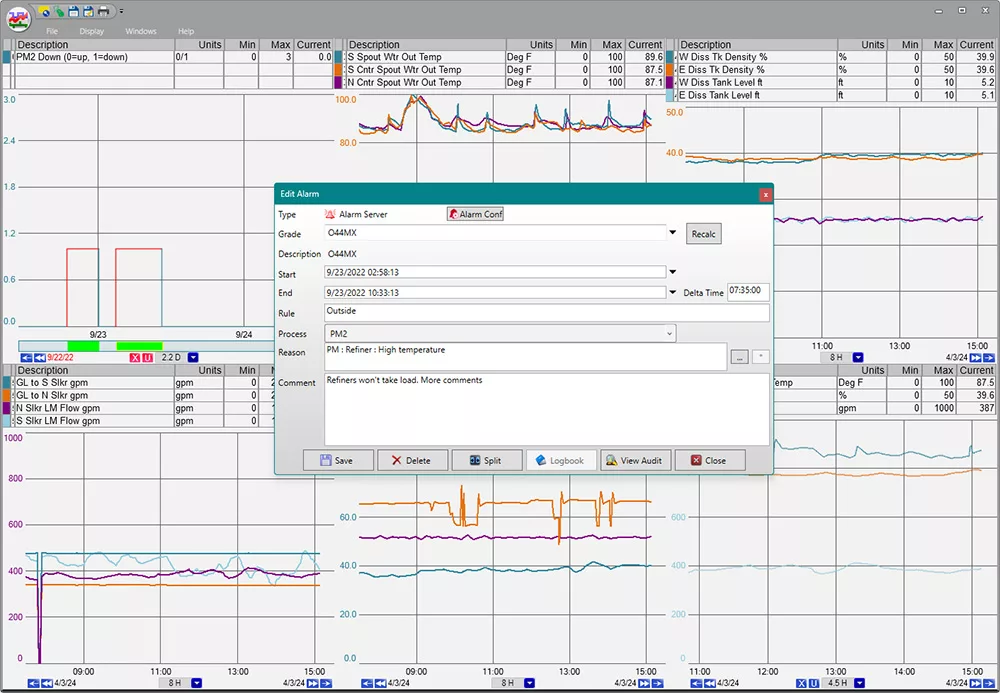
Effective alarm management prevents downtime and prevents operators from becoming overwhelmed. Not have too many alarms, and staying on top of them, allows for quick responses and maintains operational efficiency.
This can result in equipment malfunction and unplanned downtime, further escalating operational costs and risks. Consequently, maintaining effective alarm management practices is essential to ensure both safety and efficiency in industrial operations.
Under normal operating conditions, is investing in effecting alarm system management beneficial?
Yes, investing in an effective alarm system is highly beneficial even under normal operating conditions, particularly in process industries. Proper alarm management prevents alarm floods in the central control room, ensuring that critical alarms are not overlooked. This leads to more effective alarm response, enhancing operational efficiency and maintaining personnel safety.
By prioritizing and managing alarms correctly, companies can further lost production, avoid equipment malfunctions and ensure smoother operations, ultimately contributing to a safer and more productive work environment.