In this blog, discover how Industrial Data Platforms can provide increased productivity, lowered costs, and enhanced operational efficiency. By integrating advanced technologies, manufacturers can streamline their processes. Thus gaining the ability to make more informed and data-driven decisions. Learn why Industrial Data Platforms are revolutionizing the manufacturing industry and how implementing them can reduce costs and improve analytical capabilities.
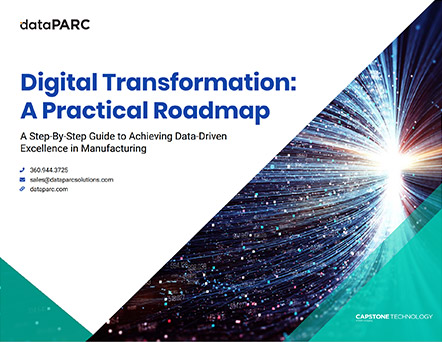
Thinking about an Industrial Data Platform? Let our Digital Transformation Roadmap guide your way.
In today’s ever-growing industrial landscape, to be able to collect, store and analyze data is critical for maintaining a competitive edge. One way to stay ahead is through the use of industrial data platforms.
Industrial data platforms are vital in this process, granting the ability for companies to integrate data from various systems and equipment across all facilities. These platforms provide real-time analysis and integrated solutions. They can also help standardize data management, enabling shared data access and enhanced operational efficiency.
With industry 4.0 on the rise, many companies are realizing the need for change with digital transformation. By bringing in new integrated technologies with the Internet of Things (IoT), companies are equipped with the tools to bring a new level of efficiency that was not previously attainable.
Understanding the Need for an Industrial Data Platform
The primary motivator for adopting industrial data platforms is the ambition to optimize industrial processes and gain improved efficiency. Big data in manufacturing can help consolidate data from multiple sources and eliminate data silos. This lets companies create more accessible and streamlined data environments.
This consolidation process can act as a data warehouse, allowing for increased data flow, accessibility, and analysis abilities. This can enhance business decision-making and predictive maintenance programs.
Advantages of Industrial Data Platforms
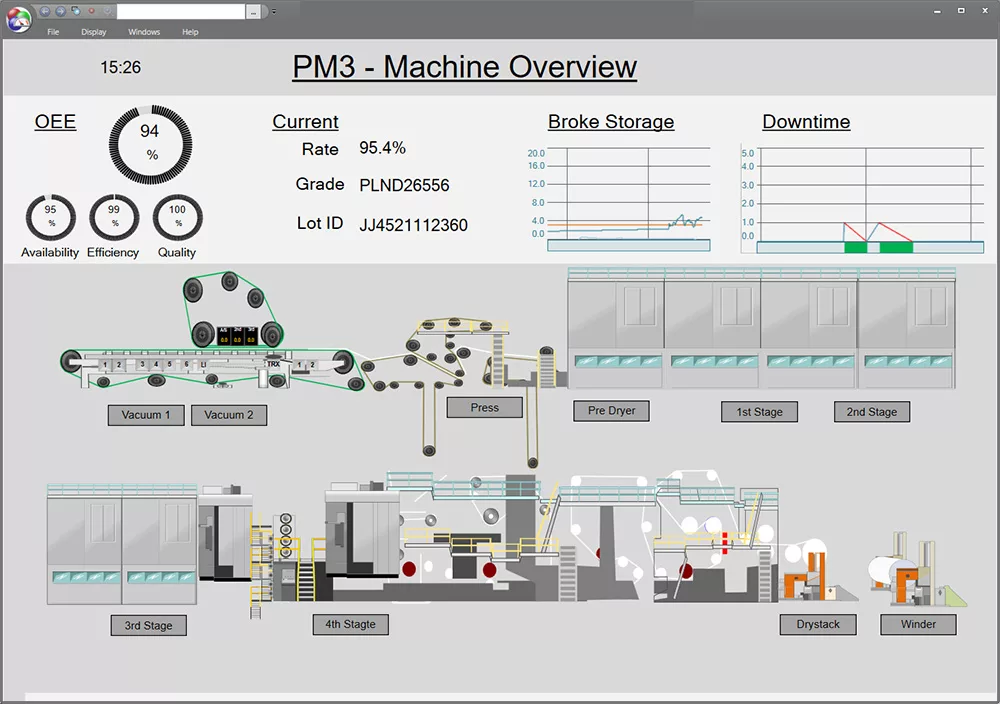
Industrial data platforms provide significant advantages by integrating data and providing a platform to visualize complex manufacturing data. This helps improve operator awareness and decision-making.
Industrial data platforms offer a multitude of benefits that can significantly elevate manufacturing operations. Some of the most important are the use of data analysis, enhanced security, cost reduction, and improved operations.
Data platforms offer improved data analytics. They can provide in-depth insights into machine performance and optimize maintenance strategies. With advanced analytics, companies can make informed decisions for operations. Many times, this is done through utilizing trends and detecting anomalies.
Proper data security is a must in today’s facilities with the IoT. By unifying data to one source, an industrial data platform can allow the implementation of robust security measures. This includes two-factor authentication and device authorization. Such features help protect sensitive information from outside access and the threat of cyber attacks.
Automation and optimization strategies are at the forefront of continuous improvement efforts. Aiming to save time and cut costs considerably. Predictive maintenance strategies are the new hot topic by leveraging Artificial Intelligence (AI) and Machine Learning (ML). Companies can reduce downtown, in turn saving on maintenance costs. In addition, automated processes reduce variability in tasks like manual testing and labor costs.
There are many advantages to using an industrial data platform in facilities. With them, you can easily analyze data, gain better insight into machinery and predictive maintenance programs, have higher security, and reduce costs.
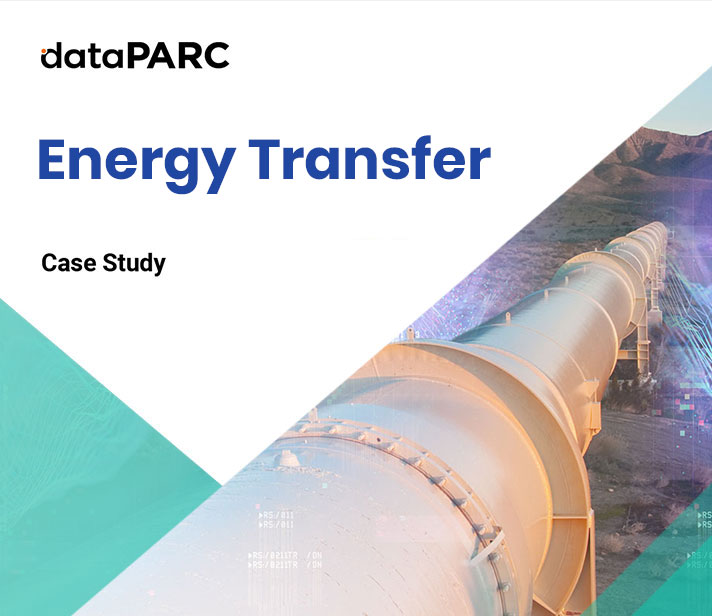
See how Energy Transfer implemented the dataPARC scalable platform across 100 sites, handling 6 million tags.
Scalability
The scalability of an industrial data platform is important for production facilities to consider. It must support organizational growth, ensuring data remains fast and accessible and can adapt to complex needs. Industrial data platforms should effectively integrate various data sources, each possibly from a different decade, and work cohesively.
Once systems are fully integrated, adding more machines and processes is quick and easy. The platform should ensure that access and performance remain efficient even as data volume increases, enabling rapid decision-making and streamlined operations.
Real-time Monitoring and Advanced Analytics
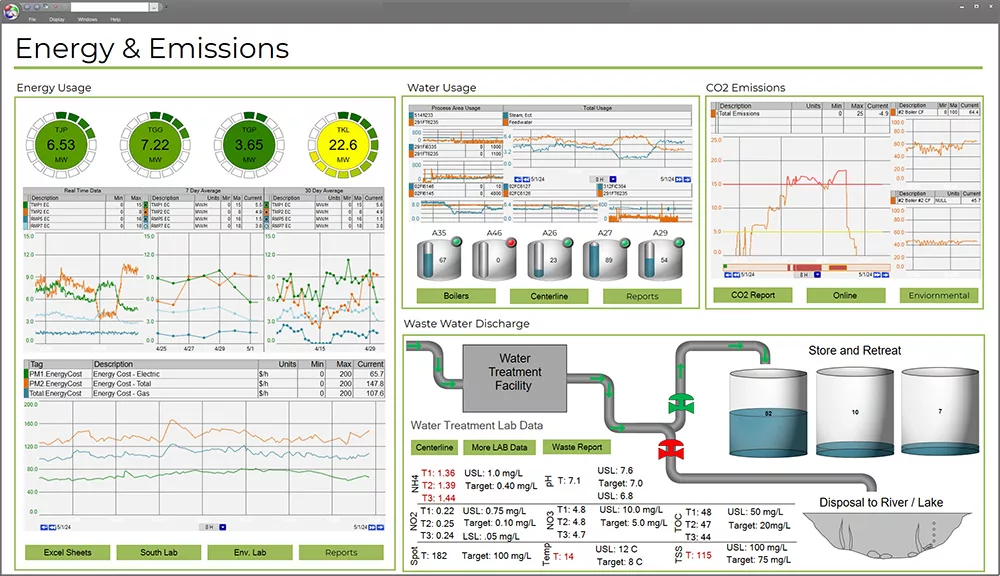
Real-time dashboards provide comprehensive monitoring solutions by displaying critical data for the process and energy and emissions regulations.
Monitoring in real-time is one of the most beneficial advantages of using an industrial data platform. The user can easily access data and view up-to-date data for their entire process in one place. This equips operators with the knowledge to make data-driven adjustments on the fly and maintain optimal operating conditions.
Through this, real-time monitoring can support sustainability initiatives. By tracking key performance indicators and ensuring that changes do not lead to harmful impacts on sustainability goals.
Advanced analytics further grows the capability of data platforms. By making use of machine learning and AI. Companies can foresee potential downtime for equipment failure and make plans for early intervention. AI can automate various processes, optimizing speed and production based on real-time data and historical trends.
Reduced Cost
Automation and optimization brought by data platforms lead to reduced operational costs. By increasing consistency through automation, manual testing, and preventative maintenance, companies can decrease the variability associated with manual processes.
Additionally, platforms reduce costs by consolidating services under a single provider. Acting as data historians, warehouses, and analytical tools, these platforms eliminate the need to outsource work, spend extensive hours deciphering data, or pay multiple companies for different services. With decreased variability, increased productivity and reduction in waste contribute to overall cost savings.
Improved Operations
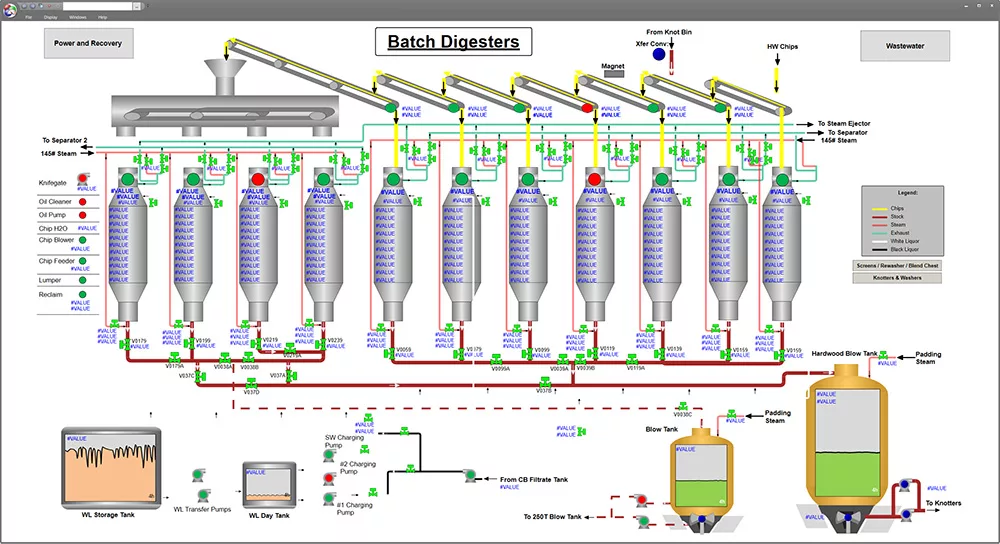
Overviews like this complex process graphic enhance operations by providing clear visibility into data, facilitating manufacturing process optimization for better decision-making and improved efficiency.
Industrial data platforms improve operational efficiency by providing operators with instant access to critical data. This quick visibility allows operators to have faster response times and more informed decision-making. Not to mention, they have more time to watch and make adjustments as hours-a-day tasks can be eliminated with just the bare minimum implementation of an industrial data platform.
Operation graphics such as live trends or overviews of systems ensure that operators are always aware of system statuses. Uses of alarms and limits on these graphics help users to visualize the health of their system, and allow for proactive management of potential issues.
Integrations with ML & AI
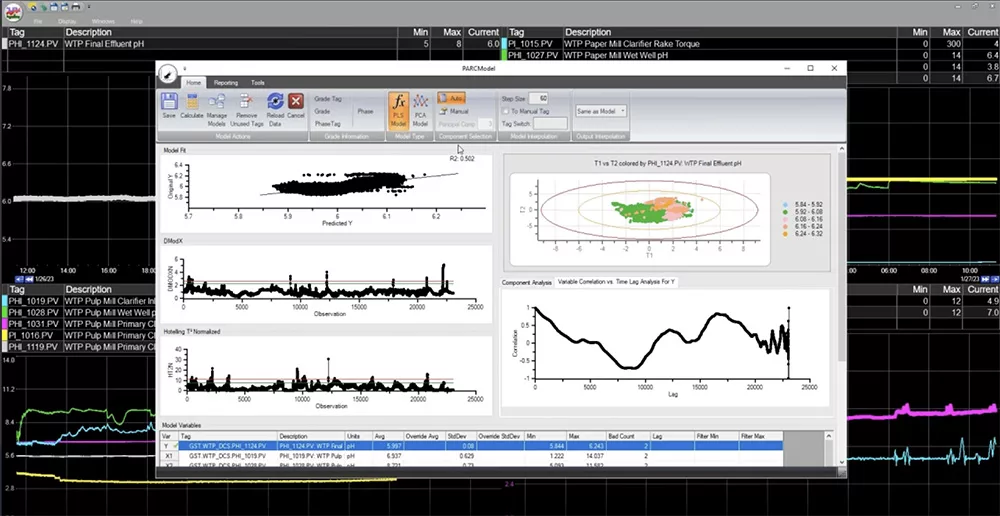
Plants can leverage machine learning and soft sensors to predict plant quality variables in real time, allowing for the modeling of properties that are impractical or impossible to measure in line.
The integration of AI and ML in a data platform opens up new capabilities of automation and predictive strategies. AI can forecast potential issues in equipment and systems before they occur, while ML enables machines to self-adjust based on various factors, such as current performance data.
Artificial intelligence can be used in factory automation and predictive maintenance. Thus allowing users to see the possibilities of what may occur to any given piece of equipment at any time. This future view can help to plan preventative maintenance of equipment before it is worn down.
Machine learning allows the machine to make changes based on its current values and how other equipment in a process performs. The need for manual tests required for predictive maintenance goes down, eradicating the possibility of compromised data.
Centralized Data Collection and Management
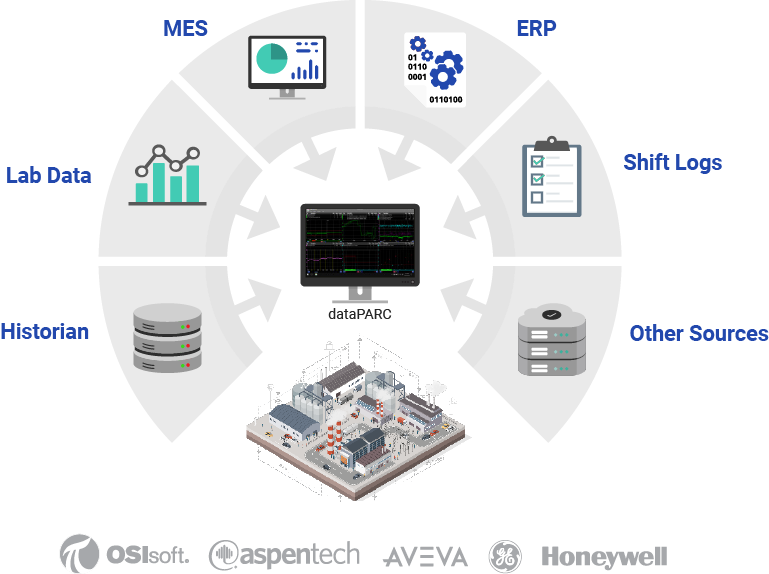
Integrate your data from any source with PARCview.
With all the user’s data in one platform, process optimization and data operations become simplified. Companies can achieve greater connectivity and analytical capabilities with consolidated data.
Device connectivity gives analytical capabilities that were not previously had before. The ability to see all data from any system in a facility at the same time allows for quick viewing of systems. This aids in the ability to adapt to market changes and more efficient service management.
Overall Factory Performance with Industrial Data Platforms
Industrial data platforms greatly enhance overall facility performance through real-time monitoring, enhanced analytic abilities, reduced costs, and minimized waste. These comprehensive insights and advanced abilities brought by data platforms empower companies in operation optimization, achieve higher levels of efficiency, and maintain a competitive edge in the industrial sector.
The adoption of industrial data platforms is a vital step for manufacturers wanting to grow and thrive in Industry 4.0. By leveraging these platforms, companies can unlock new levels of efficiency, cost savings, and operational success. Therefore, they are positioning themselves for long-term success in a rapidly evolving industrial landscape.