With PI ProcessBook being phased out, many companies are looking into PI System Alternatives. Managing plant operating data effectively is essential. Finding alternatives that integrate various operational data sources while ensuring accurate data is crucial. This article provides tips for evaluating PI System alternatives and presents some of the best options available today. It focuses on scalability, advanced analytics, ease of integration, and robust data accuracy.
PI System Overview
The PI System, developed by OSIsoft, is now an AVEVA product, which is a set of software products. It is designed for real-time data management, historical data storage, and analytics within industrial operations. Known for its robust data collection capabilities, the PI System was a cornerstone for many manufacturing plants over the years. However, they ended security updates for its leading visualization packaged ProcessBook in 2022. AVEVA will stop supporting the platform entirely in December of 2024. Systems like this are critical plant performance data monitoring tools across manufacturing industries. When companies have them and lose access to their process data it can shut down operations.
Pros, Cons, and the Case for PI System Alternatives
We’ll explore the strengths and weaknesses of the PI System to understand why some organizations might seek alternatives. You can determine if the PI System aligns with your needs by evaluating the pros and cons. Decide if it’s best to stick with the PI System for your existing system data and transition to PI Vision or if another solution better suits your site’s data needs.
Pros
- Extensive Integration: The PI System excels in data integration with various industrial equipment and systems, providing comprehensive data collection.
- Scalability: It supports large-scale industrial environments, making it suitable for enterprises with extensive operational setups.
- Strong Community: OSIsoft has a well-established community. Third parties are available to assist with their tools, helping users maximize their platform use.
Cons
- Complexity: The PI System can be complex to get operters started using the software. Not to mention, the initial implementation and continual maintenance often require specialized training.
- Cost: They use a “per-user” subscription model, requiring a license for each user to access the data. This can be more expensive than site-based licensing models.
- Limited Customization: With ProcessBook being discontinued, PI Vision is the only replacement within the PI System. Many features were not replaced from ProcessBook in PI Vision. The data visualization tools are not as robust as they once were for building comprehensive monitoring system displays.
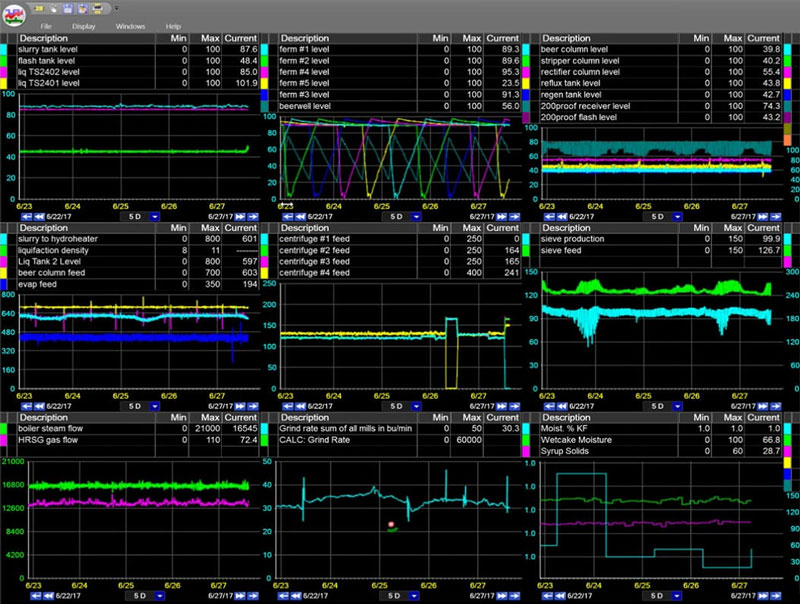
Check out dataPARC’s real-time process data analytics tools & see how better data can lead to better decisions.
Why You Might Want an Alternative
- End of Life for Key Products: AVEVA’s announcement regarding the end of life for ProcessBook and other legacy tools has prompted many users to explore alternatives. This transition phase poses challenges for those reliant on these tools. Many wonder how they will keep processing data in front of operators for daily operations and data analysis.
- Limited Features in Newer Versions: The successor to ProcessBook, PI Vision, while promising, does not yet offer all the functionalities that users have come to rely on. As detailed in PI Vision alternatives. Limitations include reduced customization and advanced analytical capabilities, which are critical for detailed and tailored data visualization and decision-making processes.
- Seeking Advanced Analytics and Integration: The manufacturing sector is moving towards more integrated and intelligent systems. This increases the need for platforms that offer seamless integration with advanced analytics, including predictive analytics and AI, is growing. Alternative systems may provide more robust data integration and feature-rich environments that better meet these requirements.
- Cost and Complexity Concerns: The PI System often has high costs and a steep learning curve. This makes it less accessible for smaller or less tech-intensive operations. Alternatives might offer more cost-effective and user-friendly solutions without sacrificing functionality.
- Broader Customization Needs: As highlighted in PI ProcessBook alternatives; there is a demand for tools that allow extensive customization to fit operational needs. Users are looking for platforms that replace PI ProcessBook, enhance the user experience, and offer new capabilities and modern data analysis.
These factors illustrate companies’ need to evaluate their current and future data management and visualization needs. Consider whether transitioning to an alternative solution could better align with their strategic goals. The subsequent sections of this blog will explore the features, pricing, and user experience of the top PI System alternatives. The goal is to assist manufacturers in making an informed decision.
3 Top PI System Alternatives
dataPARC
dataPARC is a comprehensive software suite offering enterprise-wide data visibility and a next-generation data historian. It offers a complete solution that combines the robust dataPARC Historian with the versatile PARCview for data visualization. Making dataPARC a standout alternative to the PI System.
Here’s a breakdown of what makes dataPARC the preferred choice for manufacturing plants looking for effective analytical data management and visualization tools.
User-Friendly Features
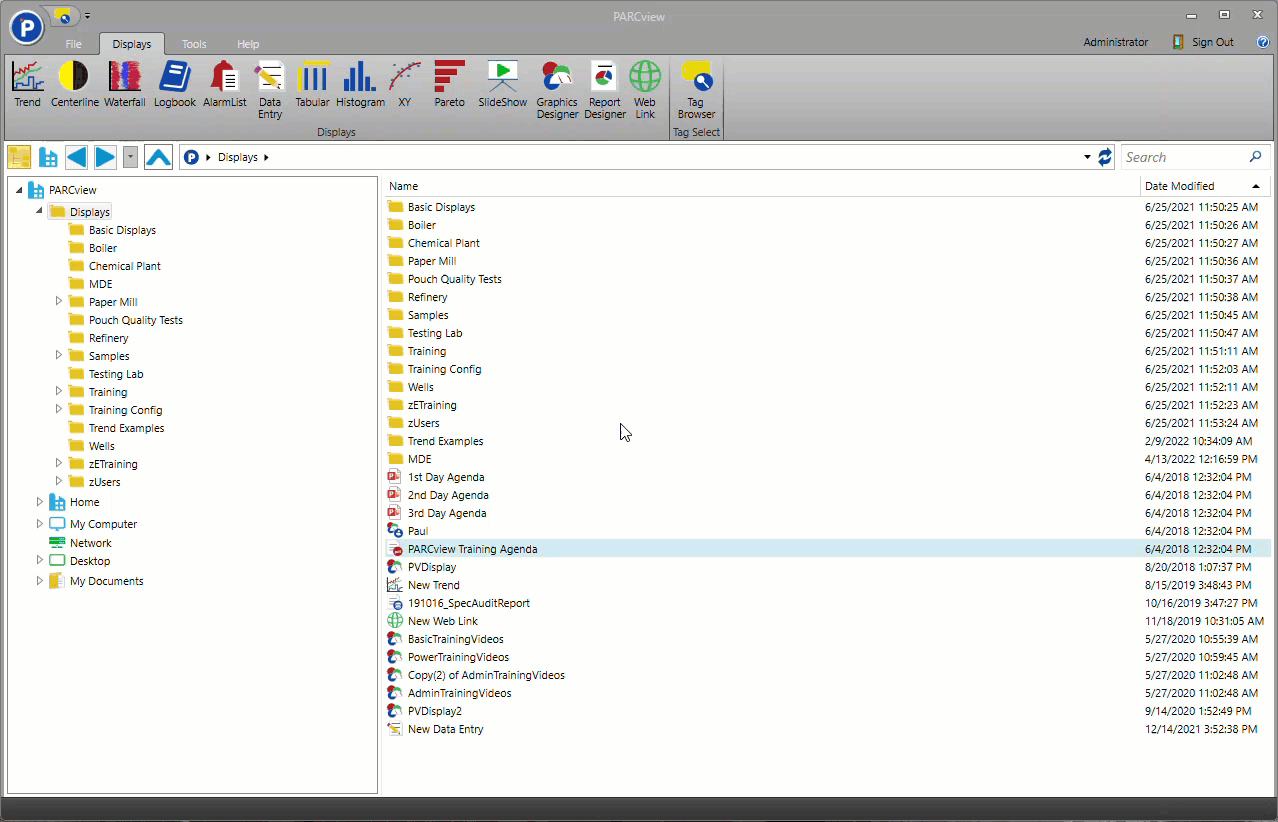
Experience seamless data navigation with dataPARC. Easily drag tags into trends and explore real-time insights with our user-friendly interface
dataPARC’s platform is designed to provide real-time and historical data analysis with an intuitive user interface. Featuring PARCview, a core component of the operational data layer, users can create customizable dashboards to display a wide range of data visualizations, from simple trends to complex graphical representations.
This versatility ensures that users can collect event data and monitor critical operational data in ways that are most meaningful to their specific needs, enhancing overall data visibility and analysis.
Exceptional Support
dataPARC is committed to providing exceptional customer support to ensure users maximize the benefits of their data management system. The support team is known for its responsiveness and expertise, offering both troubleshooting and strategic advice.
By focusing on reliable data and comprehensive data services, dataPARC helps users optimize their data visualization and analysis practices for improved decision-making and operational efficiency.
Extensive System Integration
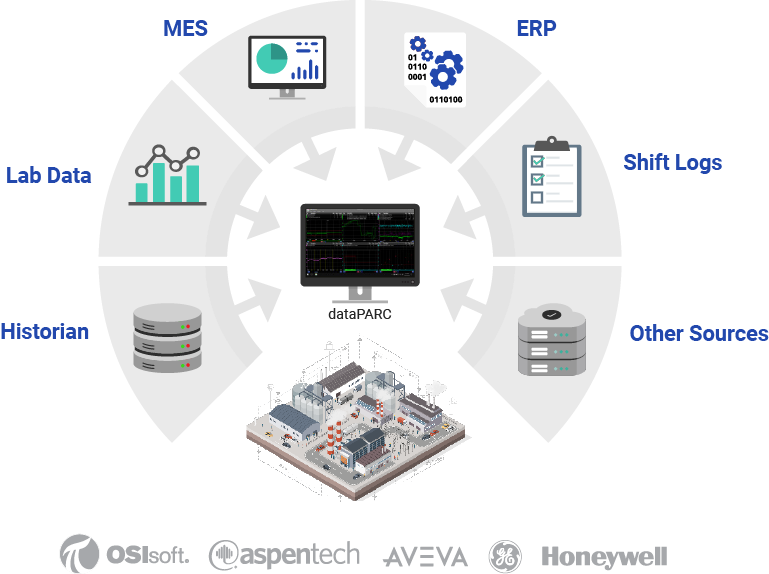
Explore dataPARC’s manufacturing data integration capabilities, seamlessly combining historians, lab data, MES, ERP, shift logs, and more for comprehensive data management.
One of the significant advantages of dataPARC is its seamless integration with existing systems and machinery. Not only with PARCview but also with the dataPARC historian, data can be collected from a diverse array of sources, ensuring all relevant data points are captured and stored efficiently.
This integration extends to third-party applications, maintaining a cohesive data ecosystem without extensive modifications. Customers always have critical data at their fingertips and can trust the accuracy of what they are viewing, thanks to the robust capabilities of data historian systems within dataPARC.
Pricing Model
Unlike the PI System, which often bases its pricing on the number of users, dataPARC utilizes a per-tag pricing model. This approach ensures that every stakeholder needing data access can get it without additional licensing costs.
This pricing strategy not only makes dataPARC more accessible but also more scalable, accommodating the growing data needs of a manufacturing operation without a corresponding increase in cost. Now, you don’t have to choose who has access to the data analytics solutions; everyone can benefit from them.
Scalable Solutions
dataPARC’s platform offers highly scalable solutions that grow with your manufacturing operations, whether managing a single site or multiple facilities globally. Its flexible architecture accommodates increasing data volumes seamlessly, maintaining performance even as demands escalate.
The modular nature of dataPARC allows for integrating additional functionalities, such as advanced analytics or expanded data storage. Moreover, its robust workflow management functionality ensures efficient process automation and optimization. This scalability enables manufacturers to adapt to evolving needs without substantial new investments, continuously leveraging dataPARC’s comprehensive data analysis and visualization capabilities.
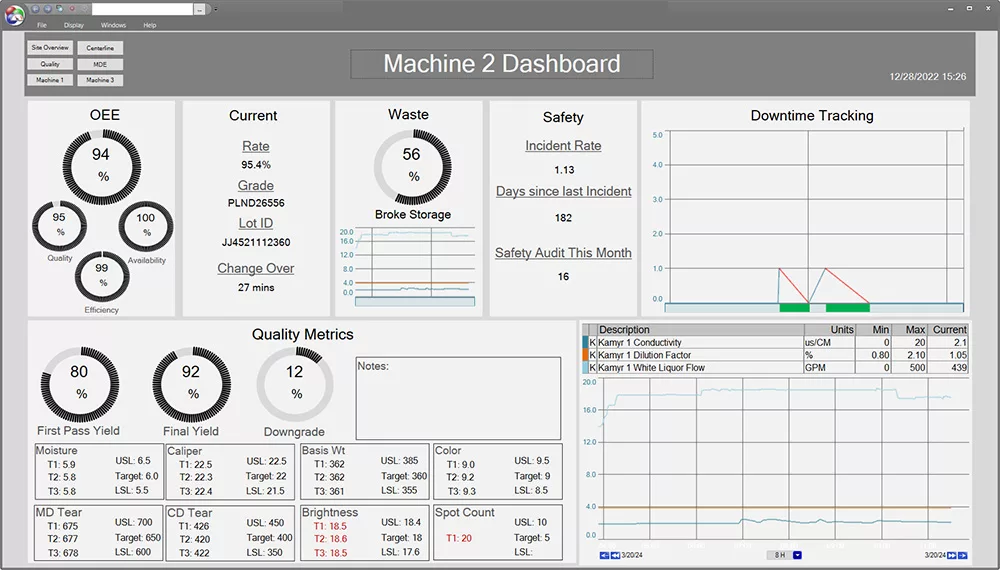
Get a comprehensive overview with dataPARC’s integrated graphics, displaying quality metrics, OEE, and downtime in one easy-to-read screen.
By focusing on flexibility, user accessibility, and comprehensive support, dataPARC stands out as a leading alternative to traditional PI Systems. It offers a more adaptable and cost-effective solution for modern manufacturing environments, with a strong emphasis on data accuracy and data integrity.
GE Digitals Proficy Plant Applications
GE Digital’s Proficy plant applications have stood out as a PI System alternative. It is valued for its strong capabilities in improving operational efficiency and productivity across manufacturing environments.
- Data Integration: GE Digital states that its Proficy software integrates with a wide range of manufacturing equipment and ERP systems. This interoperability is important for manufacturers who rely on diverse systems and need a centralized platform to manage their operations efficiently.
- Scalable Solutions: Proficy is designed to be scalable, catering to the needs of both small manufacturers and large, multi-site operations. Its flexibility ensures that as your business grows, your data management and operational intelligence capabilities can grow with it, without the need for significant additional investments.
GE Digital’s Proficy Plant Applications provides a robust alternative for manufacturing facilities looking to replace their PI System and ensure they can scale to future needs.
Siemens MindSphere
Siemens MindSphere is another formidable competitor in the realm of PI System alternatives, particularly due to its robust IoT capabilities that seamlessly integrate with digital manufacturing processes. MindSphere excels by leveraging cloud technology to provide a comprehensive suite of tools designed for industrial data analytics and connectivity.
- Cloud-Based Platform: MindSphere is a cloud-based, open IoT operating system that allows manufacturers to connect their physical infrastructure to the digital world. This connectivity facilitates the continuous collection and analysis of data across entire manufacturing operations, enhancing visibility and insights without the need for on-premise infrastructure.
- Flexible Integration: MindSphere supports a broad range of industry applications and offers flexible integration options with existing manufacturing systems and software. This versatility ensures that manufacturers can adapt and expand their IoT solutions as their business requirements evolve without being locked into a single vendor or platform.
By leveraging Siemens MindSphere, manufacturers can optimize their operations and drive digital transformation.
How to Choose the Best System
Selecting the best system for your manufacturing plant isn’t just about choosing the most popular or cost-effective option. It’s about finding a solution that aligns perfectly with your specific operational needs and long-term business goals. Do you want just to replace your system or continue your digital transformation journey?
Here’s a brief recap of the key considerations and a strategy to help you narrow down your choices effectively. Consider what’s important: scalability, advanced analytics, ease of integration, high levels of support, or having the latest tech regardless of cost and maintenance.
To effectively narrow down your options, consider implementing the following strategies based on your specific operational needs and the overarching goals of your manufacturing environment.
- Assess Integration Needs: Begin by evaluating how well potential systems can integrate with your current technological setup. This includes compatibility with existing machinery, software, and IoT devices. A system that integrates easily with your current infrastructure will reduce implementation time and costs.
- Cloud-based vs. On-premise: Decide whether a cloud-based or on-premise solution is more suitable for your site. Cloud-based systems offer scalability and remote accessibility but may raise concerns about data security and internet dependency. On-premise solutions allow you to store data locally, providing more control and reliability, especially in areas with poor internet connectivity.
- Specific Functional Requirements: Identify any specific features or capabilities critical to your operations. For example, if your operation requires extensive visualization of real-time data, prioritize systems that excel in creating and managing dynamic, interactive dashboards to present data effectively.
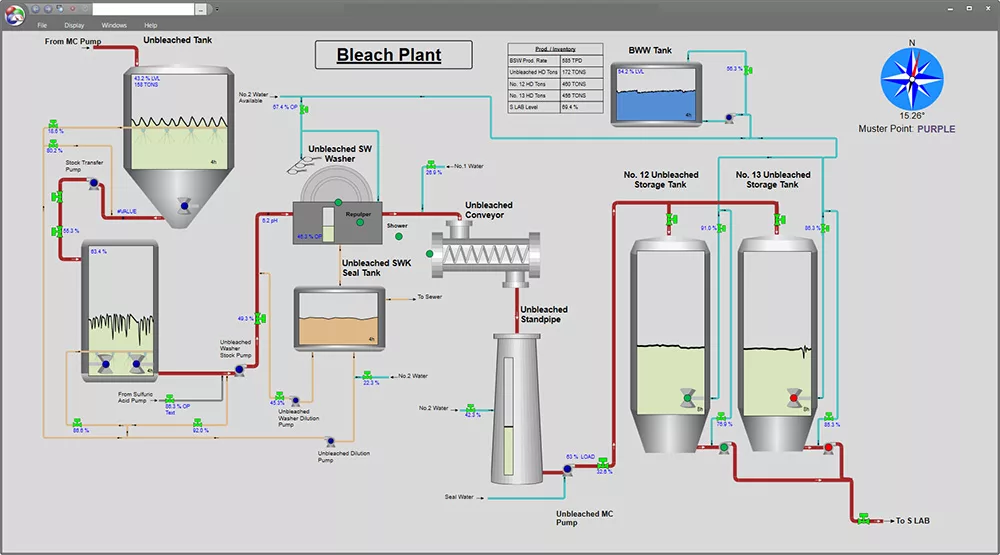
Ensure critical data is at your fingertips at all times with dataPARC’s process diagrams, displaying tank levels, and flows, for real-time process monitoring.
- Evaluate Total Cost of Ownership: Look beyond the initial purchase price and consider the total cost of ownership, which includes installation, customization, training, support, and maintenance costs. Opt for systems that offer a clear and predictable pricing model, like per-tag instead of per-user, to ensure that costs remain manageable as your usage scales.
- Consult with Stakeholders: Engage with key stakeholders, including IT staff, plant managers, and end-users, to gather insights and preferences. Note what they like and what improvements they would seek on the next system. Their input can be invaluable, as these individuals interact daily with the system.
By evaluating these aspects, you can narrow down your options to a few that best meet your specific requirements. This approach ensures that the system you choose fits seamlessly into your existing operations and enhances efficiency and productivity while positioning your plant for future growth and challenges.