Uncover how a digital twin in manufacturing can revolutionize your production processes. Learn how digital twins enable continuous monitoring, real-time data analysis, and enhanced training experience to optimize manufacturing efficiency. By embracing digital twins, you’ll gain deep insights into your operations, improve decision-making, and enhance productivity. Utilize platforms like dataPARC to integrate these advanced technologies and elevate your manufacturing capabilities.
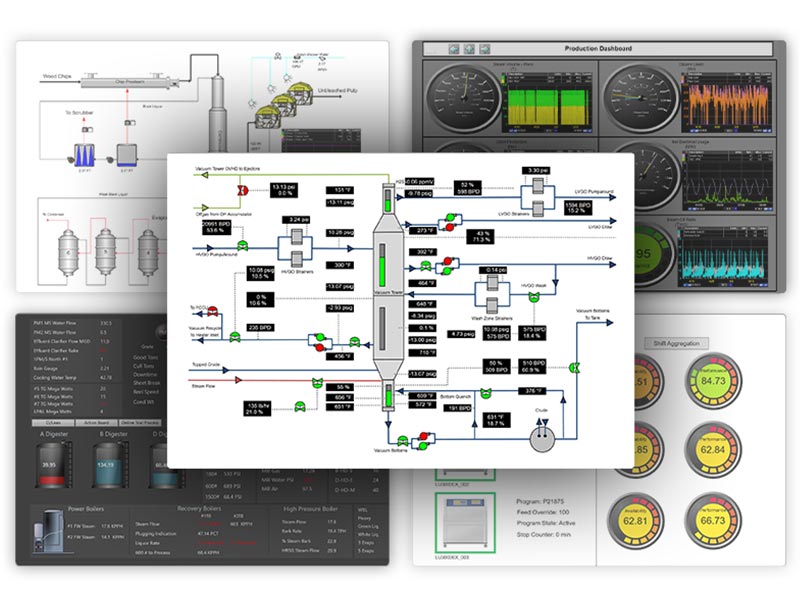
dataPARC empowers you to create real-time digital twins for smarter manufacturing.
Learn MoreWhat is a Digital Twin in Manufacturing?
A digital twin is a virtual replica of a physical object. To expand on this for manufacturing, a digital twin is a virtual replica of a process or system. Manufacturers can use this replica to monitor, analyze, design, or optimize the process without going out into the field or doing costly trials on the physical equipment. A digital replica can range from monitoring equipment data on a graphic to an entire production line simulation model. There is an array of options for those seeking digital twin solutions in process manufacturing.
Virtual replicas can be used to mirror a physical manufacturing process or plant. This dynamic and evolving representation enables manufacturers a virtual sandbox of their plant. This can be a powerful tool for optimizing performance, predicting maintenance needs, and fostering innovation. Manufacturers can uncover insights that drive smarter decisions and improve overall efficiency by creating a digital counterpart of their physical assets.

A comprehensive graphic representation of a paper machine, while buttons lead to more detailed pages when needed. Seamlessly integrating OEE, downtime, and broken storage data to enhance manufacturing insight and decision-making.
Historical Context and Trends
The concept of digital twins originated in the early 2000s, evolving significantly with technological advancements. Initially, the term was linked to product lifecycle management. Since then, it has expanded to encompass entire systems and processes in manufacturing. Today, the adoption of digital twins is accelerating. The acceleration comes from the Industry 4.0 revolution, which emphasizes interconnectivity, automation, machine learning, and real-time data.
In recent years, the integration of digital twins in manufacturing has seen a notable uptrend. Companies leverage this technology to create more agile, efficient, and responsive production environments. They want the ability to predict equipment failures, streamline operations, and accelerate product development. Digital twins are helping them achieve these goals.
Complementary Technologies
Digital twins in manufacturing do not operate in isolation; they work with various cutting-edge technologies to enhance their capabilities:
- Internet of Things (IoT): IoT devices provide real-time data that feed digital twins, allowing for accurate simulations and analyses. Sensors and connected devices monitor and collect data from the physical environment, which is then mirrored in the digital twin.
- Artificial Intelligence (AI) and Machine Learning (ML): AI and ML algorithms analyze the vast amounts of data generated by digital twins, offering predictive insights and enabling automated decision-making to optimize manufacturing processes.
- Virtual Reality (VR): VR technology allows engineers and operators to interact with the digital twin in a more immersive and intuitive way, facilitating better understanding and analysis of manufacturing processes.
By integrating these technologies, digital twins in manufacturing become a more robust and versatile tool. Allowing companies to stay ahead in the rapidly evolving industrial landscape. It is important to note manufacturers have to ready their data ecosystem for AI and other complementary tech. One way is to ensure that data historians and software platforms support these technologies and third-party integration. This compatibility allows for seamless data exchange and integration of various technologies, enhancing the digital twin’s accuracy and functionality.
Benefits of Using a Digital Twin
There are numerous advantages of working with a digital twin in manufacturing, some already mentioned, including process optimization and monitoring. Manufacturers can achieve efficiency and productivity by embracing digital twin technology, propelling their operations to new heights. Digital twins streamline processes, allowing for safer, faster repairs, more efficient training, and an accelerated pace of work.
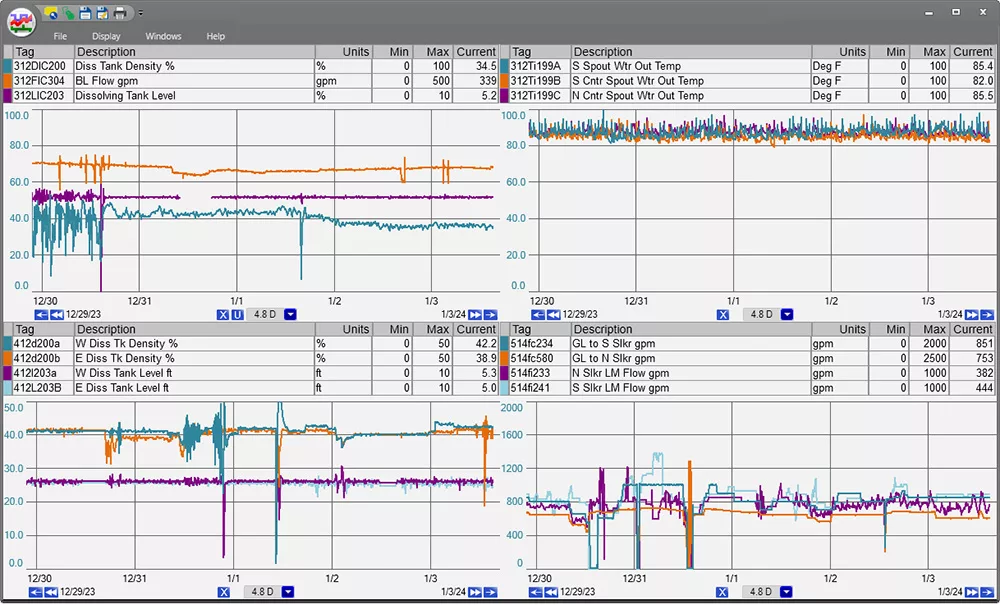
Check out our real-time process analytics tools & see how you can reduce downtime & product loss.
They serve as a powerful tool for decision-making. Manufacturing digital twins offers detailed insights and data-driven predictions that are invaluable in strategic planning. Moreover, a digital model provides a wealth of data and analytics; it is a catalyst for internal improvements.
It can also act as a compelling narrative for investors and stakeholders. This investment in digital transformation showcases the company’s commitment to technological advancement and operational excellence. As we continue, it becomes evident that digital replicas are a technological upgrade and a necessity for manufacturers today. In the next section, we will continue to explore the benefits of using digital twins in manufacturing.
Digital Twin Use Cases
Digital twin technology is revolutionizing the manufacturing industry by offering numerous applications that significantly enhance operational efficiency and innovation. Equipment monitoring is among the most impactful use cases, where digital twins provide unprecedented visibility and control over manufacturing assets.
Equipment Monitoring
Real-Time Data Analysis:
Having access to digital twin data enables continuous monitoring of physical asset equipment performance by analyzing the data collected in real-time. This granular visibility allows for immediate detection of anomalies, reducing downtime and enhancing productivity. Whether using trends or HMI graphic screens displaying real-time data, such examples of digital twin technologies provide actionable insights that empower operators to make informed decisions swiftly. Real-time data monitoring and analysis is one of the initial steps for manufacturing companies in their digital transformation journey.
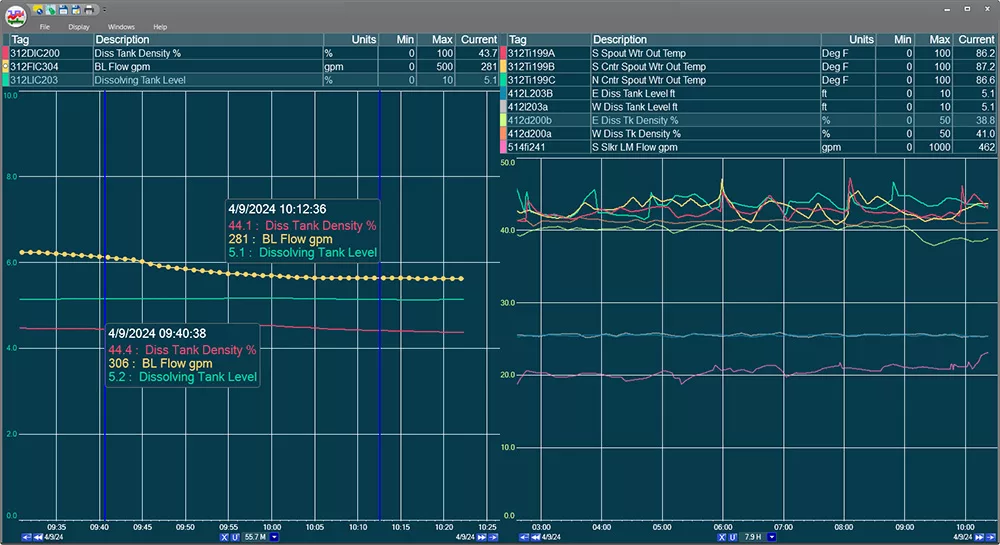
Enhance digital twin views with real-time data and dataPARC’s multi-trend display, offering real-time insights and smart mouse interactivity for precise equipment monitoring.
Predictive Maintenance:
By leveraging the predictive analytics capabilities of digital twins, manufacturers can predict failures before they occur. This proactive approach to maintenance will reduce costs by avoiding costly repairs. It also extends equipment lifespan and minimizes unplanned downtime.
Optimization of Operations:
Equipment monitoring through digital twins facilitates fine-tuning machine operations for optimal performance. Manufacturers can simulate different scenarios to identify the most efficient operational parameters, leading to energy savings, reduced wear and tear, and improved product quality.
Lifecycle Management:
Beyond daily operations, digital twins offer a comprehensive view of the equipment’s lifecycle, from installation through decommissioning. This holistic perspective aids in strategic planning, investment decisions, and sustainability efforts. This can be coupled with maintenance plans to ensure equipment effectiveness is on track for the age and lifespan of the asset.
Training
Enhanced Learning Experiences:
Digital twins in manufacturing revolutionize training programs by providing immersive, interactive learning experiences. Trainees can engage with the virtual model of the manufacturing environment. They gain hands-on experience without the risks associated with the physical system. This method fosters a deeper understanding of the equipment and processes, accelerating the learning curve.
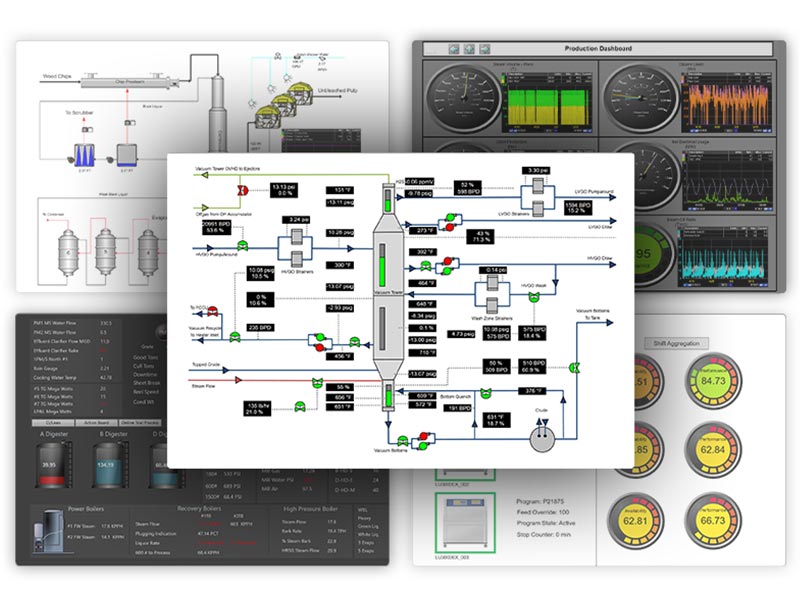
Enhance training with dataPARC’s intuitive user experience, giving employees what they need with real-time insights.
Simulation of Real-World Scenarios:
One of the standout benefits of using digital twins for training is the ability to simulate a wide range of operational scenarios, including emergency situations that would be impossible or hazardous to replicate in the real world. This prepares employees to handle various challenges efficiently and safely, enhancing their problem-solving skills and readiness.
Consistency and Scalability:
By standardizing training through digital twins, manufacturers ensure consistent knowledge transfer and quality across the workforce. Moreover, digital twin-based training can easily be scaled to accommodate more participants or adapted to different facilities, supporting the organization’s growth and adaptation to changing market demands.
By leveraging digital twins in training, manufacturers are enhancing the effectiveness and efficiency of their training programs and investing in their most valuable asset— their people. This forward-thinking approach equips employees with the skills and knowledge needed to excel in an increasingly complex and technologically advanced industry.
Tours and Guests
Interactive Guest Experiences:
Beyond mere observation, digital twins enable interactive experiences for guests. Visitors can engage with the virtual environment, manipulate elements, or even participate in simulated processes. This interactive component makes the experience more engaging and informative. It offers a deeper insight into the manufacturing operations and the company’s technological prowess.
Educational Outreach:
For educational institutions or programs aiming to expose students to advanced manufacturing concepts, digital twins serve as an excellent tool. They provide a realistic glimpse into the industry’s inner workings. This can help to inspire and educate the next generation of engineers, technicians, and industry professionals.
Stakeholder Engagement:
When engaging with stakeholders, digital twins can be a powerful tool to showcase the facility’s capabilities or future plans. This technology can help stakeholders better understand the complexities and innovations within the manufacturing process. Thus, facilitating more informed discussions and decisions.
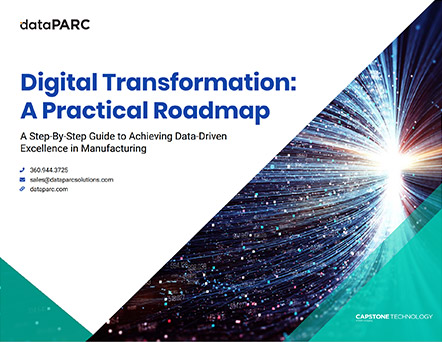
Discover the path to innovation with our digital transformation roadmap guide. Elevate your manufacturing processes strategically.
Marketing and Branding:
Utilizing digital twins for tours and guest experiences also serves as a strategic marketing and branding tool. It highlights the company’s commitment to innovation and technology. Distinguishing it in a competitive market and attracting attention from potential customers, partners, and talent.
By integrating digital twins into tours and guest experiences, manufacturers can offer a modern, immersive, and informative window into their operations. This not only enhances engagement but opens communication with a broad array of audiences.
Design Planning
Iterative Design Exploration:
Digital twins offer a dynamic platform for design planning, allowing engineers and designers to test and iterate on their ideas in a virtual environment. This capability significantly reduces the time and cost associated with physical prototyping, enabling a more agile and experimental approach to design.
Collaborative Design Process:
Digital twins facilitate a collaborative design process, enabling teams across different locations to work together seamlessly. Stakeholders can interact with the digital twin, provide feedback, and make informed decisions, ensuring alignment and accelerating the design timeline.
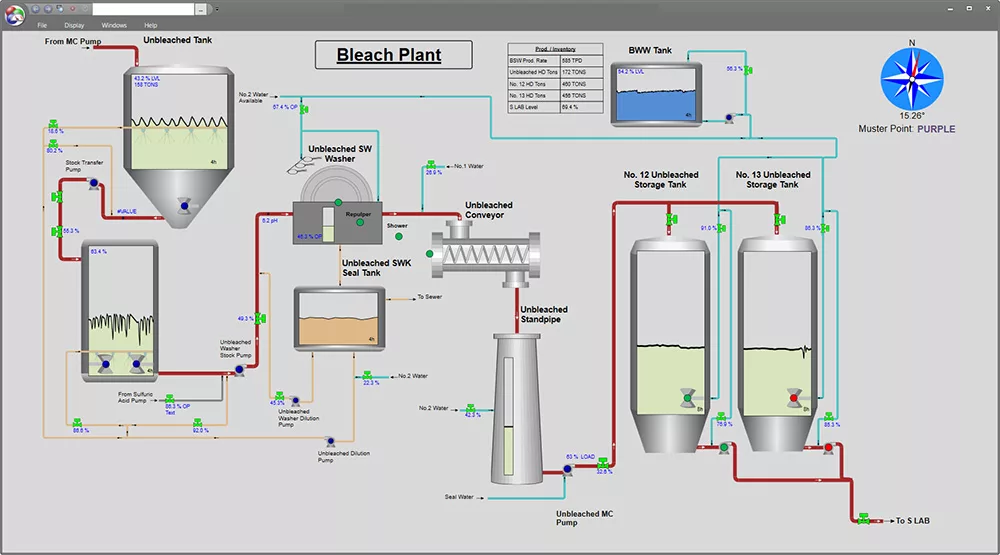
Visualize precision with dataPARC’s digital twin: a detailed graphic of a bleach plant, integrating tanks, lines, and trends for comprehensive asset monitoring.
Risk Mitigation:
Manufacturers can identify potential issues and design flaws early in the process by using digital twins in design planning. This proactive approach allows for timely adjustments, reducing the risk of costly errors and rework in later stages of product development.
Sustainability and Resource Optimization:
Digital twins enable designers to assess the environmental impact and resource usage of their designs, promoting more sustainable manufacturing practices. By optimizing materials and energy consumption in the virtual model, companies can minimize waste and improve the overall sustainability of their products.
Incorporating digital twins into design planning empowers manufacturers to innovate more effectively, respond to market demands swiftly, and create products that are not only high in quality but also sustainable. This strategic use of digital twins is transforming the landscape of design in the manufacturing industry, setting new standards for efficiency, collaboration, and environmental responsibility.
How to Create a Digital Twin for Your Facility
Implementing digital twins in your manufacturing facility is a step toward operational efficiency and decision-making. dataPARC offers a suite of tools that enable plant managers to create and utilize asset performance as part of a digital environment. Here’s a streamlined guide on how to get started with your digital twin applications:
1. Asset Selection:
Start by identifying which components of your facility would most benefit from a digital representation. Focus on assets where enhanced visibility could improve efficiency, reduce downtime, or improve performance. Processes lacking data, could be higher priority or do a gap tracking analysis to determine potential impact and feasibility.
2. Digital Representation Creation:
Develop digital models of your chosen assets. This can be achieved through various methods depending on the software available. Leveraging existing digital blueprints to convert into a graphic or manually create models that reflect the physical characteristics of these assets.
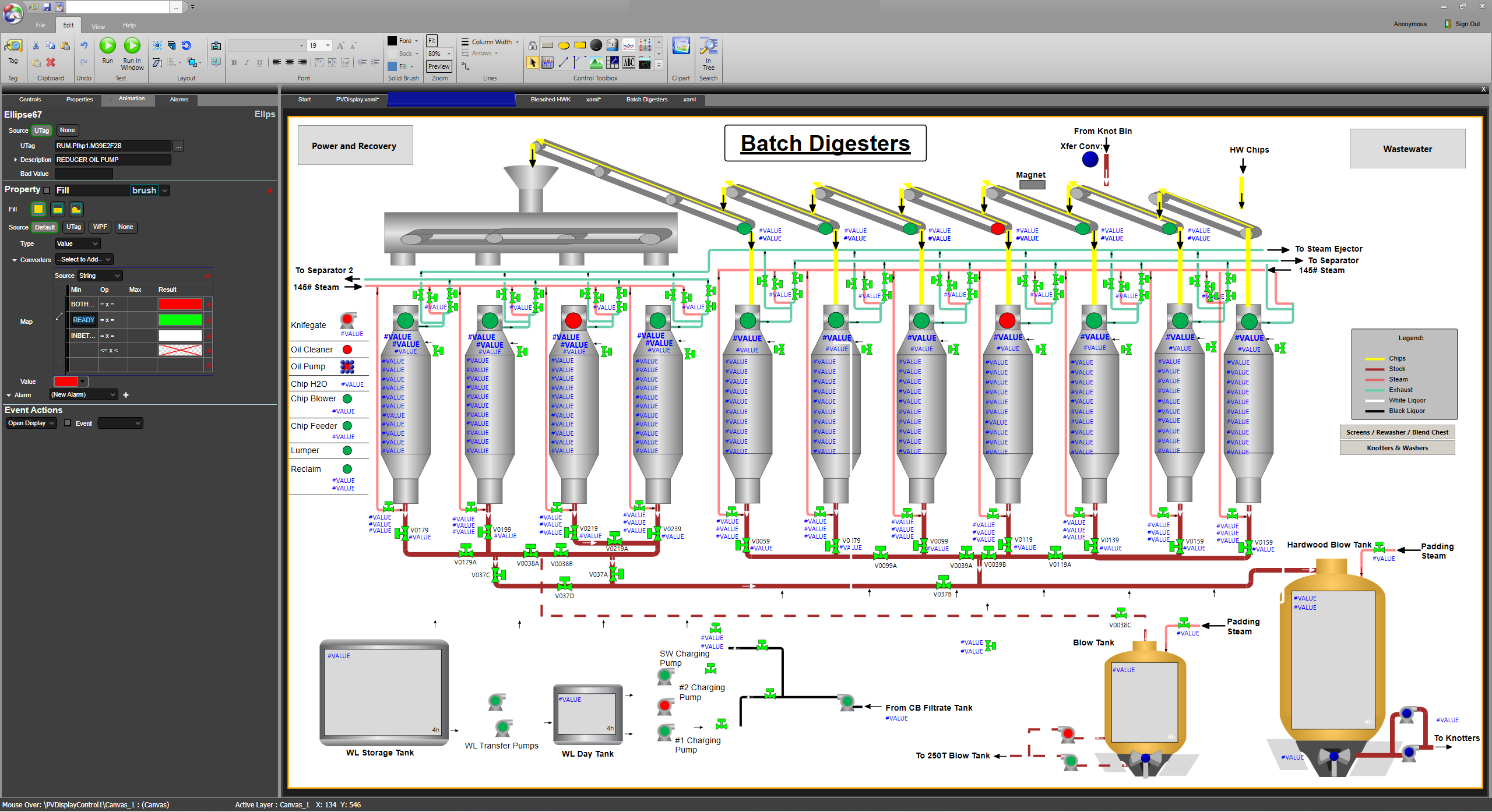
Craft your facility’s digital twin with dataPARC’s Dashboard Designer. Use images to illustrate processes such as batch digesters and pull-in tags to incorporate data monitoring. These help to ensure an accurate digital representation.
3. Sensor Integration and Data Collection:
Equip your selected assets with appropriate sensors to collect and transmit operational data. This step is crucial for ensuring that your digital twin reflects real-time conditions. For more about data collection and historization, check out Data Historian: Still The Right Choice for Your Manufacturing Data. dataPARC facilitates the integration of this data, ensuring robustness and accuracy in the digital twin’s reflection of real-world operations.
4. Development of Analytical Models:
Utilize dataPARC’s analytics capabilities to build models that interpret the collected data, enabling the prediction of operations and adjusting the process before the outcome occurs. This step transforms your digital twin into a proactive tool for operational excellence and strategic planning. For more complex models, be sure third-party software will seamlessly integrate with what you have.
5. Activation and Operational Integration:
With the digital twin developed, integrate it into your daily operations. Use it as a dynamic tool for continuous monitoring, scenario analysis, and decision support. dataPARC ensures that the digital twin is a living component of your operational ecosystem, providing ongoing value and adaptability. Such real-time data should be available to operators to make data-driven decisions.
6. Continuous Improvement and Training:
Leverage dataPARC’s training resources to ensure your team is proficient in using the digital twin. Encourage ongoing feedback and use insights from the digital twin to continuously improve your processes and asset management.
This approach provides a structured yet flexible framework for implementing a digital twin, leveraging dataPARC’s capabilities to enhance each process step. The focus is on creating a tailored solution that aligns with your facility’s specific needs and goals, ensuring that the digital twin becomes a cornerstone of your operational strategy.