Yogi Berra once said, “If you don’t know where you are going, you might wind up someplace else.” This is stating the obvious but it is important to have a plan when implementing OEE. If you don’t spend time planning up front, you will pay for it down the road with extra time and effort or it could lead you down the wrong path with misleading OEE results.
When implementing OEE, it helps to start with a standard definition of OEE and its factors, and work backwards to determine what data you need for the calculation. The OEE calculation formula is standard, but there are many different opinions on what data should be included when determining the availability, performance, and quality factors. Just remember that if you don’t measure it, you can’t improve it.
To help with your OEE implementation, we have included some guidelines to help explain some of the most confusing aspects of OEE:
1. Define OEE
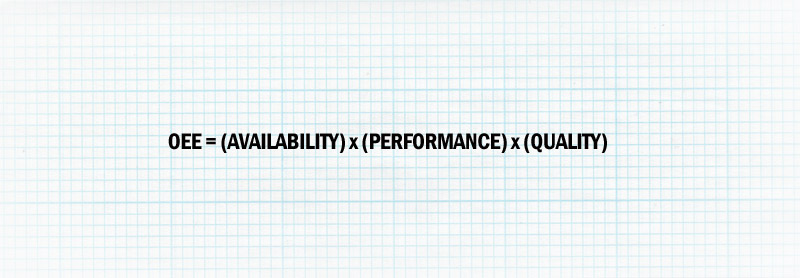
As we said, the formula is pre-defined, so this may not be one of the most confusing implementation issues, but it’s the key to the entire process. There are 5 values you need to capture in order to calculate OEE:
- Unscheduled time
- Unplanned downtime
- Total units produced
- Target units
- Good units produced
With these 5 values you can calculate OEE for any time period, but you should also consider what information you need to problem solve the OEE losses. For example, it is a good idea to capture detailed downtime data, such as the machine fault, downtime reason, duration, and operator comments or corrective actions. You might also want to collect the quality measurements used to determine if the product is within specifications and any off-quality reasons.
2. Define Unscheduled/Unavailable Time
Availability measures the downtime losses of your process when it is available to run, but some time should be removed from the available time if the process is not scheduled.
(!) Unscheduled time should only include the following:
Lack of customer orders
If a machine can produce more than customers demand, the machine is not required to run without customer orders. However, if running over customer demand to add inventory to the warehouse, the time should be counted as available time.
Lack of operating personnel or other resources
Lack of personnel or resources must be caused by forces outside the company’s control (force majeure) in order to be considered unscheduled time. A planning mistake that causes a raw material supply shortage should be considered unplanned downtime and should count in the OEE calculation. You wouldn’t want to hide these problems.
Product development/trials
During research and development work, the equipment is unavailable to the production team, so this time is considered unscheduled and is excluded from OEE calculations.
Events like preventative maintenance, changeovers, cleaning, operator breaks, and meetings can occur during unscheduled time without counting as downtime, but if they occur during scheduled time, then the time needs to be accounted for.
he goal is to improve the process, not to have a high OEE, so all losses in control of the operations team should be tracked. This isn’t always popular because people don’t like to see a lower number, and some things may seem like they are not in control of the operators. However, if you want to identify all opportunities that are available for improvement, you must be honest with yourself and not worry about the absolute OEE value.
Looking to improve OEE? Get The Complete Guide to OEE, and get everything you need to successfully implement, analyze, & improve oee at your plant.
3. Define A Value For Target Speed In The Performance Calculation
The choice of target speed (or ideal cycle time) can vary depending on how a facility wants to evaluate the production speed. Some companies will use a “budget” or “standard” speed that is product specific. However, using a budget speed that is lower than the maximum speed raises the OEE and hides the true production capacity. Sometimes the speed differences can be significant, and knowing the impact on OEE can help identify process improvements or optimize product mix.
The best way to calculate the performance factor is to always use the maximum theoretical production speed. This is sometimes referred to as the nameplate capacity or design speed for the equipment. To make all speed losses visible, the target speed should be the same for all products even though some products may be run at slower speeds. Knowing the speed loss caused by “difficult products” can help compare and understand the total business impact of running some products with reduced capacity.
The performance factor should never exceed 100%, so it is better to have a target speed that is too high versus one that is too low. You want to make improvements, but the speed target should only be changed if there is a major process or equipment change. Reaching the maximum speed should not be a regular occurrence that requires frequently updating the target speed. If a theoretical maximum is not known, it is a good idea to set the target speed 10-25% above the current demonstrated maximum to ensure the performance factor does not exceed 100%. If the performance factor is above 100%, it can hide deficiencies in availability or quality.
4. Exclude Rework And Downgraded Parts From The Quality Factor
The quality factor of OEE only counts units that are good quality the first time they are produced. If a part doesn’t meet quality specifications the first time through the process, then the time spent reworking that part should be counted against OEE. You are spending additional resources to rework the part instead of producing a new quality part.
Some units might not meet their quality specifications, but they could still be sold as a different grade, brand, etc. Although they can still be sold, the product did not meet its intended purpose as produced, so it was not correct the first time through the process and it should be considered waste.
This can be one of the more difficult aspects of OEE to track. Some processes can be sending rework through at the same time as new products so it can be difficult to isolate. Some consideration should be given to how this can be accomplished in your particular process. As far as OEE is concerned, waste (scrap), rework, or downgraded product are all considered quality losses.
It is important that the specifications used for quality are within the capability of the process, and that the properties can be easily tested.
5. Find The Bottleneck
When calculating OEE for a production line, you should collect availability data on the bottleneck (slowest machine) of the process because the bottleneck determines the production for the line.
Downtime events should be tracked for all pieces of equipment in the line. When tracking downtime for the bottleneck, also keep track of the amount of time the bottleneck is starved and blocked. The bottleneck is starved when waiting for input from upstream equipment and it is blocked when downstream equipment cannot receive output.
The actual speed for the line is equal to the bottleneck speed, but the speed target for the performance factor should be based on the fastest equipment in the line. This will highlight the impact of having an unbalanced line and will help justify improvement activities on the bottleneck.

In the process above the slowest step is 90 units/minute and the fastest is 120 units/minute. If step 4 consistently runs at 90 units/min, the performance rate would be 90/120, or 75%. So, why not use 90 as the target speed and then have a performance rate of 100% because the line cannot run faster than its slowest component. Looking at the performance rate this way hides the fact that this line is handicapped by a step that can run only 75% of the rest of the line. Effort should be focused on the slowest step to have the biggest impact on effectiveness.
6. Do Not Average OEE Values
OEE is a weighted calculation. A lot of times OEE is calculated for small time periods, such as an hour or shift, and then simply averaged to calculate an OEE for a longer time period, but this is a bad practice. OEE should be calculated from its base data for each time period. The following example illustrates why averaging OEE values does not work.
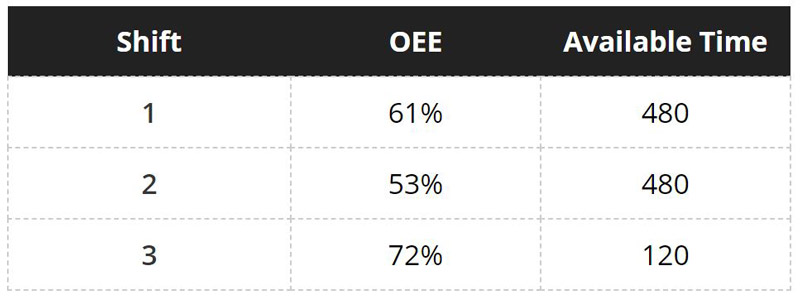
If you just take the average by adding the OEE values together and dividing by three, you will get a daily OEE of 62%. However, the third shift only had 120 minutes of available time, so when weighted by available time, the daily OEE is actually 59%. The difference may seem small, but it is important, especially when you are trying to track progress.
Implementing OEE: Parting Thoughts
The goal of tracking OEE is to get the right information to the right people at the right time so they can solve problems that reduce waste and improve productivity. Determining the correct data to be analyzed is a critical step in OEE implementation and improvement.
Once you know what data you need, you can figure out how to collect it and calculate OEE. OEE can be tracked manually on paper or with a spreadsheet or there are several software options. Manual calculations and tracking can be a good way to get started and verify the OEE data collection process, but automatic systems will help save time and effort and will provide more reliable results.
OEE: The Complete Guide
All the resources you need to successfully implement, analyze, & improve overall equipment effectiveness.
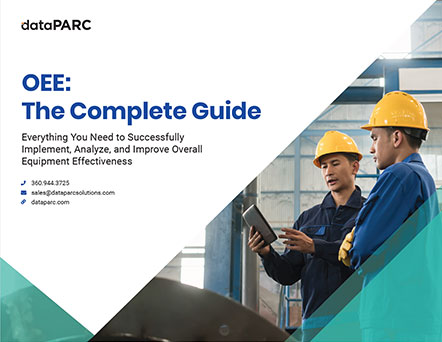