The ISA-95 spec and OPC UA companion standard provide a model that allows software programs to exchange all the relevant information throughout a manufacturing organization.
This model provides the framework for an industrial internet of things by breaking down the communication barriers between objects.
The Internet of Things
The concept of an “Internet of Things” (IoT) has been around since about 2005 and has really begun to catch on in recent years. Basically, IoT is connecting multiple “things” with sensors to data processing programs capable of sending data to and receiving data from those things. The things can be anything from household appliances to industrial machines.
In factories this concept is called the Industrial Internet of Things or Industrie 4.0. Industrie 4.0 is the term coined in Germany for the IoT because it is being considered the 4th Industrial Revolution.
No matter what it’s called, the goal is to create a network world with intelligent objects that can communicate and interact with each other.
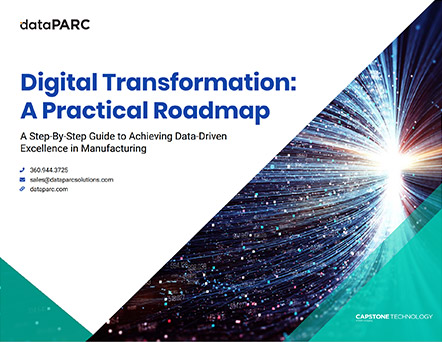
Integrating IT & OT data at your plant? Let our Digital Transformation Roadmap guide your way.
Both IoT and Industrie 4.0 involve connecting manufacturing machines and sensors so they can communicate and take action in real time. This can involve anything from automated control of production lines to maximize throughput to smart electricity grids that can balance power generation to match loads.
IoT is really just a concept, so there needs to be some enabling technology to make it a reality. There are some equipment and software vendors that have come up with their own solutions, but this can be limiting. Universal standards are required to guarantee interoperability between equipment and devices from different manufacturers.
Two related specifications have been established to address the need for a standard: ISA-95 and OPC UA. When combined, these two specifications provide a prescription for implementing a universal IoT platform.
Manufacturing Operations Management Systems
Before jumping into the ISA-95 and OPC UA standards, we need to provide a little background about current systems and why a universal standard is needed to achieve an IoT environment.
Think about how many different control and monitoring systems are required in modern manufacturing operations:
- Manufacturing Execution Systems (MES) for managing production
- Plant Information Management Systems (PIMS) for collecting and analyzing process data
- Laboratory Information Systems (LIMS) for tracking quality test performance
- Warehouse Management Systems (WMS) for managing the inventory of raw materials and finished goods
- Computerized Maintenance Management Systems (CMMS) for managing maintenance operations
- Learning Management Systems (LMS) for managing the training and qualifications of personnel
Collectively these systems are known as Manufacturing Operations Management (MOM) systems. The purpose of MOM systems is to help coordinate the allocation of resources (raw materials, energy, personnel, and equipment) to produce quality products. So, just like at home, MOM keeps an eye on everything and keeps things running smoothly.
However, each program has a specific function and they are rarely well integrated with each other. On its own, each system does its job well, but the overall results usually fall short of expectations. How can this be? We have all these systems to help coordinate the manufacturing process, why do we still have gaps?
There are actually many reasons. Each application is developed by a different vendor and they generally don’t play nice together. Special code is required for each information request between systems. The quality of these solutions can vary greatly, from web-based interfaces that can query multiple systems, to monster spreadsheets.
The purpose of ISA-95 is to facilitate communication between these MOM systems so manufacturing efficiency can be further improved.
On the road to digital transformation? Get our Free Digital Transformation Roadmap, a step-by-step guide to achieving data-driven excellence in manufacturing.
ISA-95
ISA-95 divides typical manufacturing organization activities into 5 levels.
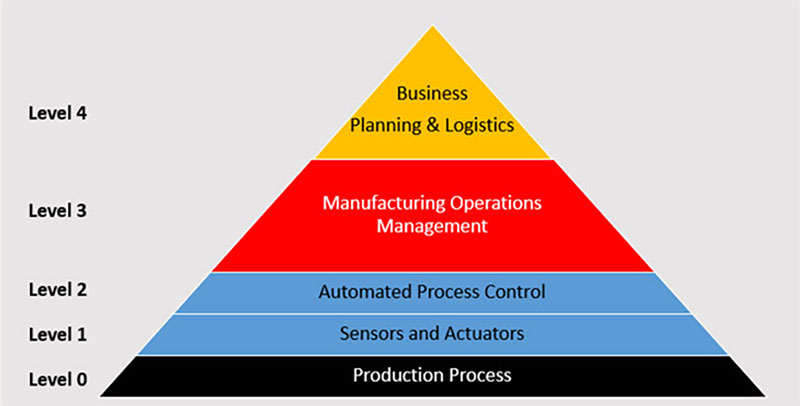
ISA-95 Activity Pyramid
Level 0 is the actual physical process. Levels 1 and 2 include all activities needed to monitor and control the physical process in real time. Level 3 includes all of the manufacturing operations management activities mentioned above.
Finally, Level 4 includes all of the business planning and logistics activities that are required to ensure the right materials are used to make the right products so they can be delivered to customers.
ISA 95 focuses on defining the information exchanges that occur within and between Levels 3 and 4.
ISA-95 defines four resource categories required for managing the information exchange in manufacturing processes:
- Materials and their properties
- Role based equipment
- Physical Assets
- Personnel and their roles and qualifications
Material
An adequate raw material supply and spare parts inventory are required to maintain efficient manufacturing operations. Based on incoming orders, the availability of raw material and energy resources needs to be confirmed.
Inventories need to be planned for short and long term material and energy requirements. Once product has been produced, the finished goods inventory also needs to be controlled and the production costs need to be calculated.
Equipment & Physical Assets
ISA-95 has defined two equipment categories. Role based equipment refers to the purpose or function of a given piece of equipment, and the physical asset is the specific equipment performing that function. To illustrate the difference consider a motor used to pump fresh water. Let’s call this the Fresh Water Pump Motor. The role based equipment would have properties that define the Fresh Water Pump Motor, such as the horsepower.
The physical asset is the specific motor that is installed as the Fresh Water Pump Motor. The physical asset can be identified by a serial number, or some other unique identifier. It is important to separate equipment in these two categories, so that information, such as motor amps can be tracked regardless of which motor is installed, and rebuild history or run hours can be tracked for each motor.
Also, Motor 101 could be used for other applications, not just the Fresh Water Pump Motor, so motor inventory can be monitored.
A common link between all of the MOM systems is the manufacturing equipment, so it is important to have equipment identification information. For example, production scheduling is assigned by equipment, Overall Equipment Effectiveness (OEE) calculations are equipment based, and maintenance is obviously tracked for each piece of equipment. However, the same piece of equipment often has a different ID in each system, which makes it difficult to share information between programs.
Personnel
Personnel availability is the final piece required to manage a manufacturing operation. This involves managing the availability of qualified individuals at all levels in the organization, from equipment operators, product testers, warehouse employees, and management.
You need to ensure that you have the necessary qualified persons available to operate the equipment needed to make product to fill the customer orders.
OPC UA Information Models
OPC UA uses a flexible and extendable system to define objects and variables. Templates (called Types in UA) are used for definitions and instances are created from them. For example, a Motor (object) template might have properties (variables) HP, RPM and Voltage.
If motors M100 and M200 (instances) are created from that template, they will have the HP, RPM and Voltage properties. Templates can be extended by creating a child and adding properties to the child; instances created from the child template will have all the properties from the child and parent templates combined.
If an AC Motor child template adds the Phase property then motor M300 created from the ACMotor template will have properties HP, RPM, Voltage and Phase.
ISA-95 defines four base templates: Equipment, Physical Assets, Personnel and Materials. From these a user can create sub-templates that accurately represent the types of objects in the facility. Motor templates might have three or four sub-templates. Pump templates could have 8 or 9 sub-templates whereas other objects might have none. The user can create the level of detail appropriate for their needs.
Once the templates are complete the user can create the facility’s objects and combine them in meaningful hierarchies and the objects can exist in multiple hierarchies without conflict. One hierarchy might represent the physical layout of the facility while another might represent the process flow. A piece of equipment in multiple hierarchies will have information from each (such as a cost center from the physical and a grade tag from the process) but each hierarchy will only be aware of the information appropriate to that hierarchy.
The values for properties can be static and stored in a database or dynamic and driven by a process tag. Most dynamic properties are used in equipment but it is possible to have dynamic properties on other types.
Summary
The ISA-95 spec and OPC UA companion standard provide a model that allows programs to exchange all the relevant information throughout a manufacturing organization. This provides the groundwork for an industrial internet of things by breaking down the communication barriers between objects. Software can be created to allow autonomous communication between equipment and sensors, but the improvements are not limited to machines. Communication between people and things and even person to person improves. All of this can improve manufacturing efficiency, reduce costs and facilitate better, faster decision making.