パレートチャートとは、「結果の80%はその入力の20%から生じる」というパレートの原理に基づく品質改善ツールです。
イタリアのエンジニアであり経済学者であったVilfredo Paretoは、人口と富との関係で80/20の法則に初めて気付きました。20世紀初頭、Paretoは、イタリアやヨーロッパの他の国々で、富の80%が人口のわずか20%によって支配されていることに着目しました。
80/20の法則
この80/20の法則は、以下のように、多くの異なるシステムに当てはまります。
- 交通機関では、遅れの80%は考えられる原因の20%によるものである可能性がある
- ビジネスでは、収益の80%は顧客の20%または製品の20%からもたらされている可能性がある
- 製造プロセスでは、ダウンタイムの80%は問題の20%に起因している可能性がある
パレートチャートは、総合品質管理やシックスシグマの手法で使用される重要なツールの1つです。基本的には、ある結果や効果に対する原因ごとの寄与を表す棒グラフです。棒の長さは、それが表す原因の「コスト」(時間、数、または金銭)を表します。最も重要または主要な原因を視覚的に強調するために、長い棒から短い棒へと順番に並んでいます。
品質管理でのパレートチャートの使用
パレートチャートは、以下のようなさまざまな方法で使用できます。
- プロセスの問題または欠陥の頻度を分析する
- 大まかな原因を、個々の構成要素を検討することで分析する
- 問題または原因が多数存在する場合に、最も重要な問題または原因に作業を集中させる
- 問題または原因の重要性を伝えるのに役立つ
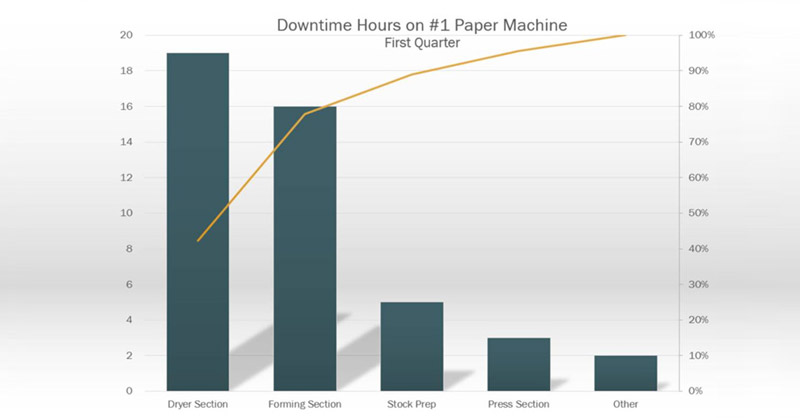
パレートチャートを使用してプロセスの問題を特定し・・・

・・・それらの問題を掘り下げて個々の構成要素を分析する。
デジタルトランスフォーメーションに移行中ですか?製造業でデータドリブンの卓越性を実現するためのステップバイステップガイドである無料のデジタルトランスフォーメーションロードマップを入手できます。
パレートチャートを作成するステップ
パレートチャートを作成するには、以下のステップを実行します。
目的の設定
パレートチャートを作成する最初のステップでは、その目的を設定します。興味がある成果または効果を挙げます。たとえば、製造プロセスではダウンタイム、サービスプロバイダーでは顧客からの苦情、運送会社では出荷の遅延などが考えられます。
原因と測定対象の決定
次に、原因を分類する方法および適切な測定対象を決定する必要があります。一般的な測定対象は、時間、数、頻度、およびコストです。
時間枠の決定
チャートの時間枠を決定します。データを見たいのは、シフトごと、日ごと、週ごと、または月ごとのどれですか。
データの収集
データの収集方法を決定します。手動、表計算ソフトの使用、またはおそらくもっとも便利な方法であるデータヒストリアンの使用を選択できます。データの収集が簡単であるほど、および原因の定義が明確であるほど、良いことです。PIMSおよびデータヒストリアンの中には、ダウンタイムおよび生産ロスの分析に役立つパレート変数を入力できるものもあります。
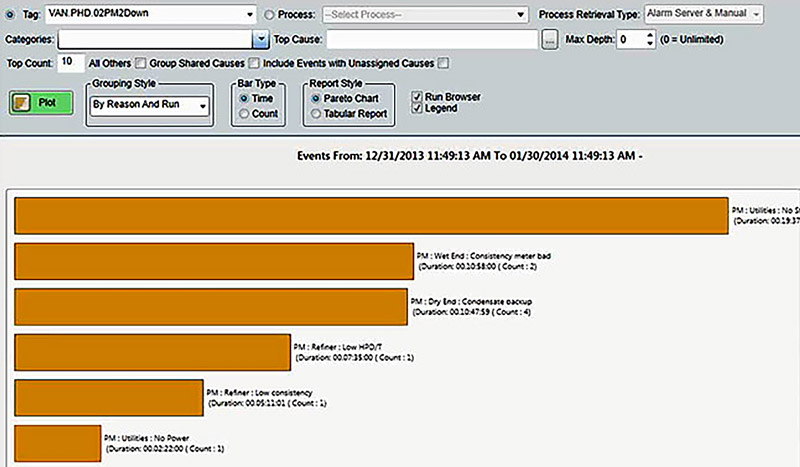
データの分析
選択した時間枠の原因ごとの小計を計算します。必要であれば、原因ごとの寄与率を計算できます。これは、原因ごとの小計をすべての原因の合計で割った値です。測定値スケールの反対側に、割合スケールを描くことができます。
チャートの構築
X軸に原因、Y軸に測定単位を記載し、チャートを構築します。棒が最も長い原因を端に配置し、残りの棒を降順に並べます(非常に短い棒がいくつもある場合は、「その他」というラベルを付けた1つの短い棒にまとめることができます)。
パレートチャートに累積百分率曲線をプロットすることもよくあります。この曲線を描くには、1番目の棒の場所で、1番目の原因の寄与率を示す点を描きます。2番目の棒の場所で、1番目の原因の寄与率と2番目の原因の寄与率を足した合計を示す点を描きます。3番目の棒の場所で、前の寄与率の合計に3番目の寄与率を足した合計を示す点を描き、以下同様に続けます。最後の点は、割合スケールで100%になるはずです。最後に、すべての点を線で結んで、累積百分率曲線を作成します。
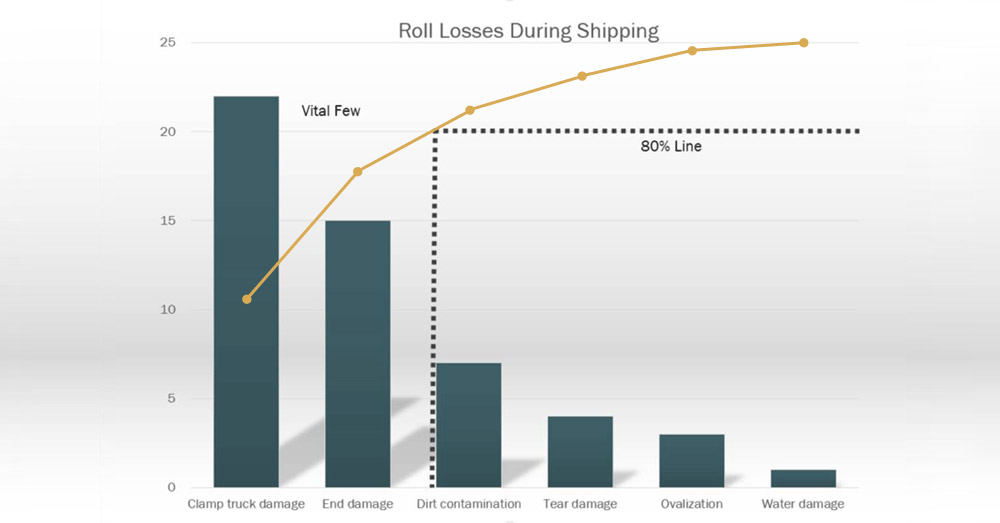
パレートチャートを使用して「重要な少数要素」を特定し、改善作業を方向付ける。
80/20の法則を適用する場合、この時点で割合スケールの80%からX軸に平行に線を引き、累積百分率曲線と交わるところで止めます。この点より左にある原因が問題の80%を引き起こす原因(「重要な少数要素」)であり、右にある原因は重要度が低い原因です。これにより、問題に対して最も大きい影響を与える可能性がある原因に、改善作業を集中させることができます。
OEE: 完全ガイド
総合設備効率の導入、分析、および向上を成功させるために必要なすべてのリソースがここにあります。
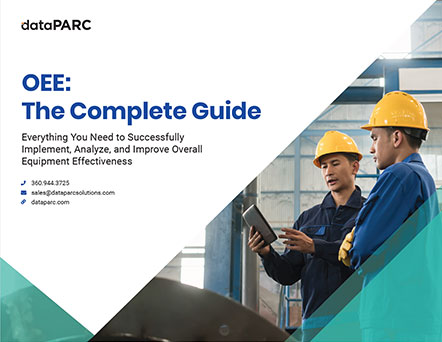
製品概要資料
dataPARCの製品概要をダウンロードするには、以下のリンクをクリックしてください。この資料では、dataPARCを使用して重要なデータを視覚的情報に変換することで、迅速な意思決定をサポートするメリットが詳しく説明されています。
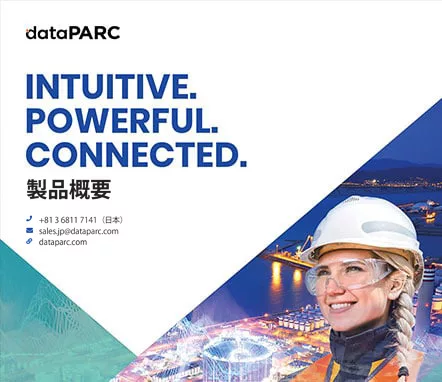