Manufacturing Root Cause Analysis Tools
Effective Solutions for Root Cause Analysis
Equip your team with powerful diagnostic tools to uncover root causes, resolve recurring issues, and drive continuous improvement. dataPARC’s real-time analysis and visualization capabilities help manufacturing teams troubleshoot faster and make smarter decisions on the plant floor.
Quickly Identify Production Issues with Interactive Visual Dashboards
Uncover hidden process inefficiencies using interactive dashboards and real-time production data. Spot trends, visualize problem areas, and empower teams with actionable insights across the plant.
- Identify patterns and trends in operational data.
- Drill into events and data points for root cause discovery.
- Customize visualizations to meet your specific needs.
- Share visuals across teams to align response.
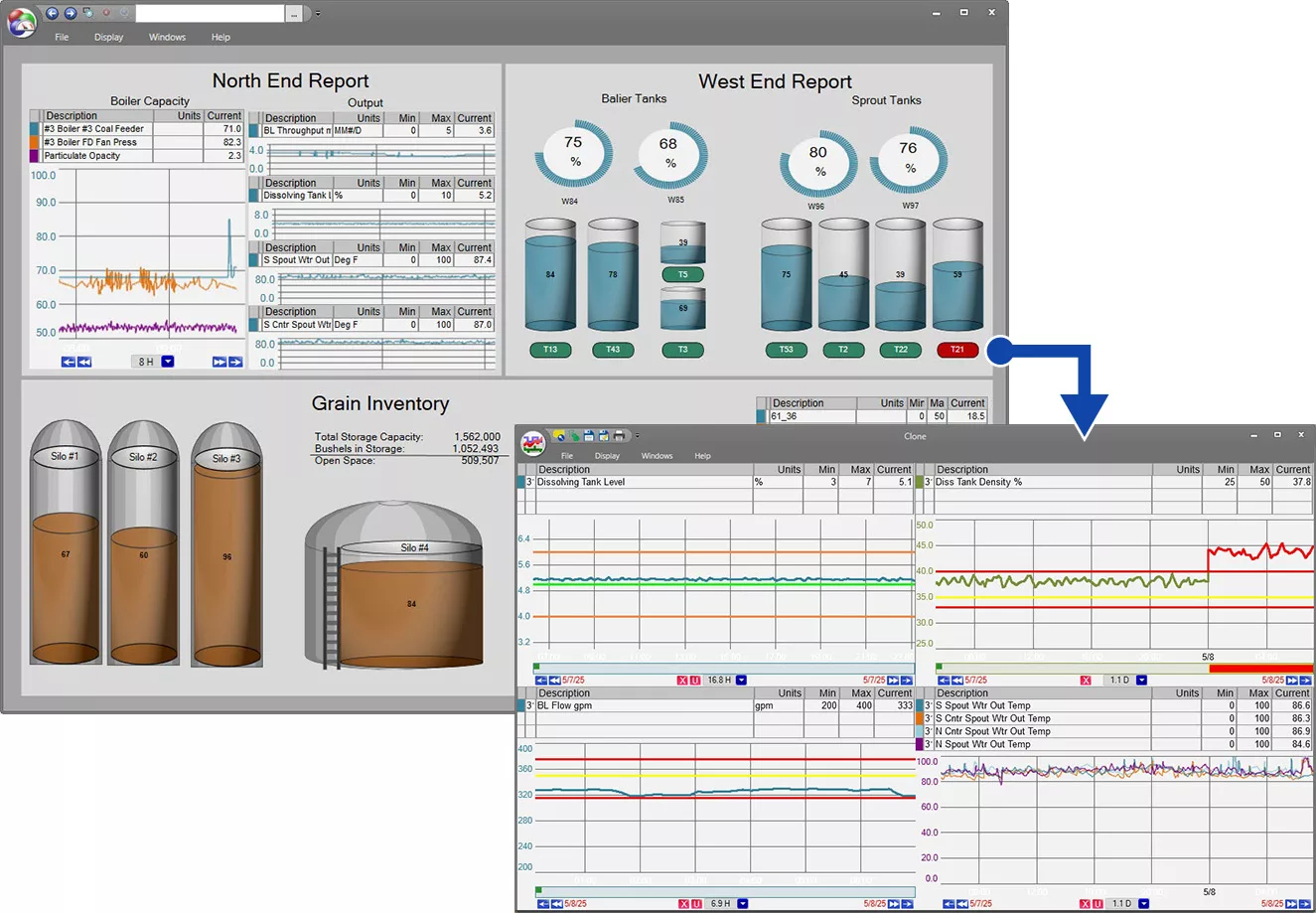
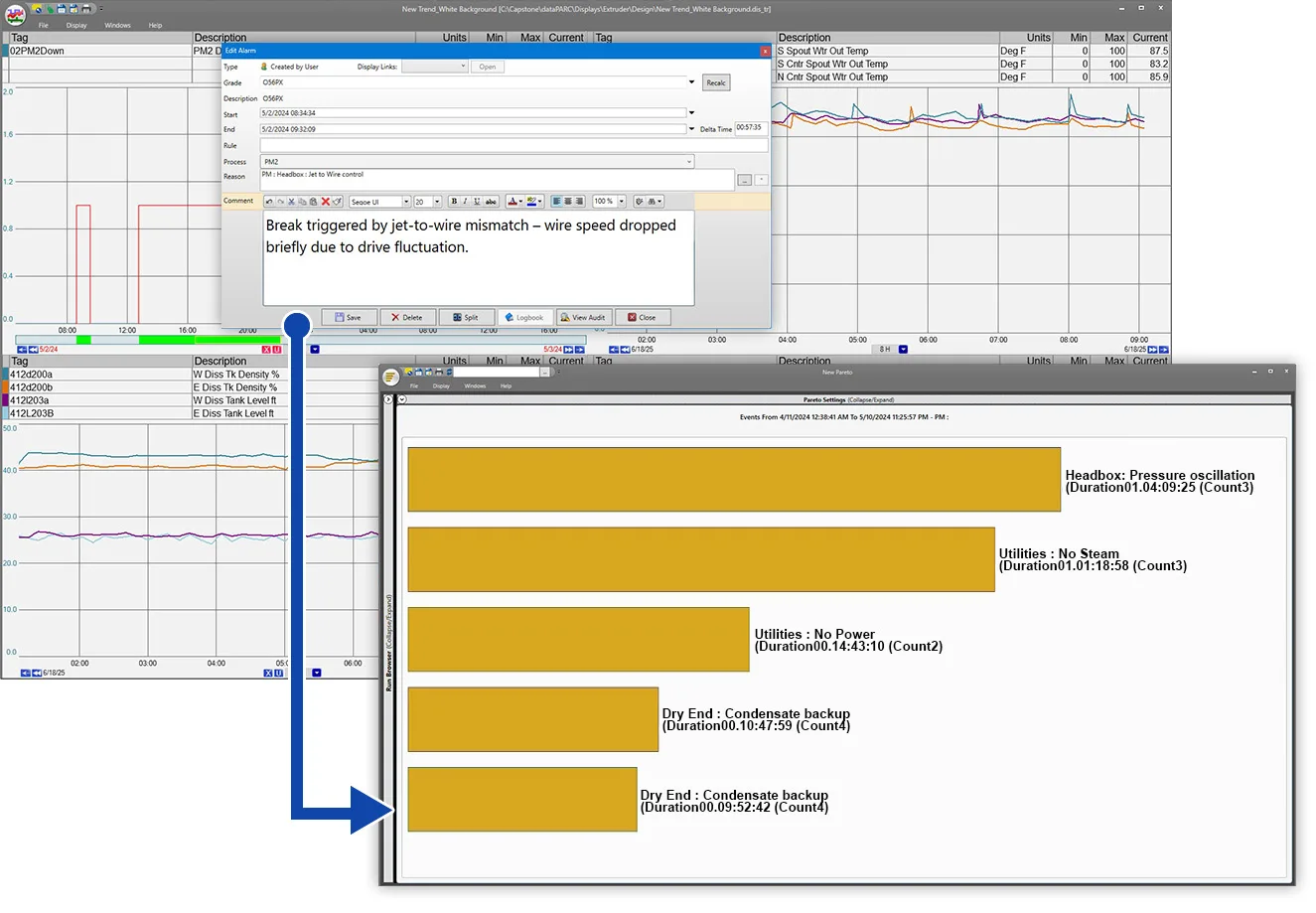
Prioritize Issues Based on Pareto Analysis
Focus your team’s efforts on the problems that matter most. Use Pareto charts to isolate the few root causes responsible for most downtime, so you can allocate resources effectively and drive improvement.
- Analyze frequency and impact of issues
- Focus on the top 20% of problems causing 80% of downtime
- Allocate resources effectively to address critical issues
- Monitor improvements and adjust priorities as needed
Identify Process Deviations with Centerline Displays
Leverage centerline analysis to maintain optimal operational parameters and quickly identify deviations.
- Establish baseline performance metrics
- Monitor deviations from established centerlines
- Implement corrective actions to realign processes
- Prevent recurrence of issues through continuous monitoring
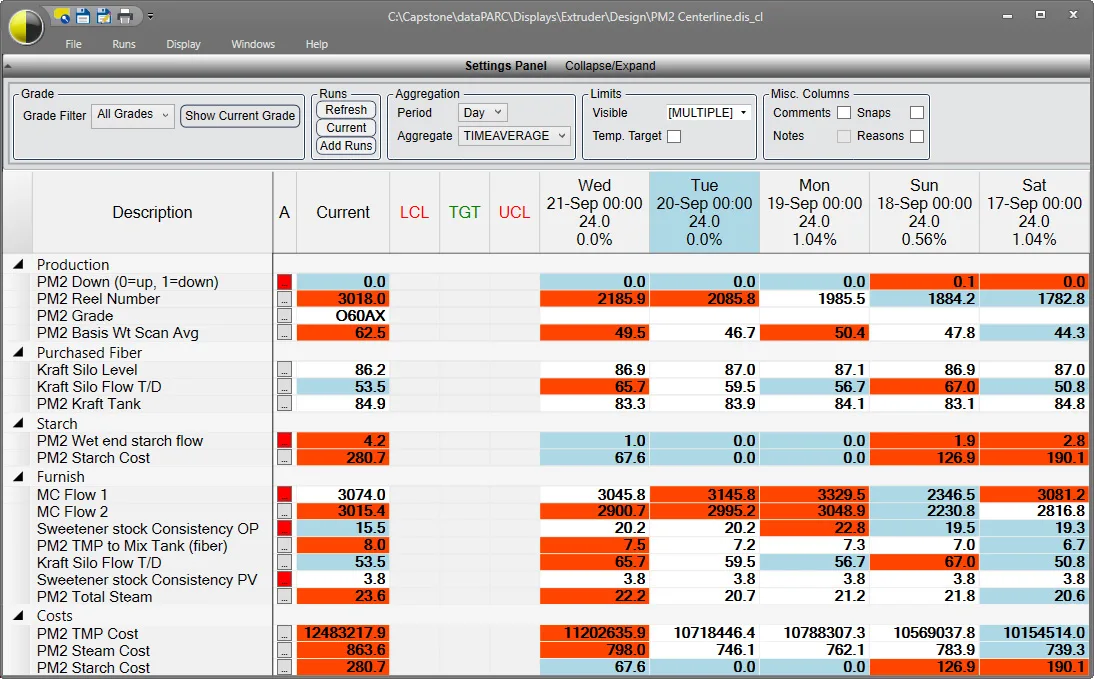
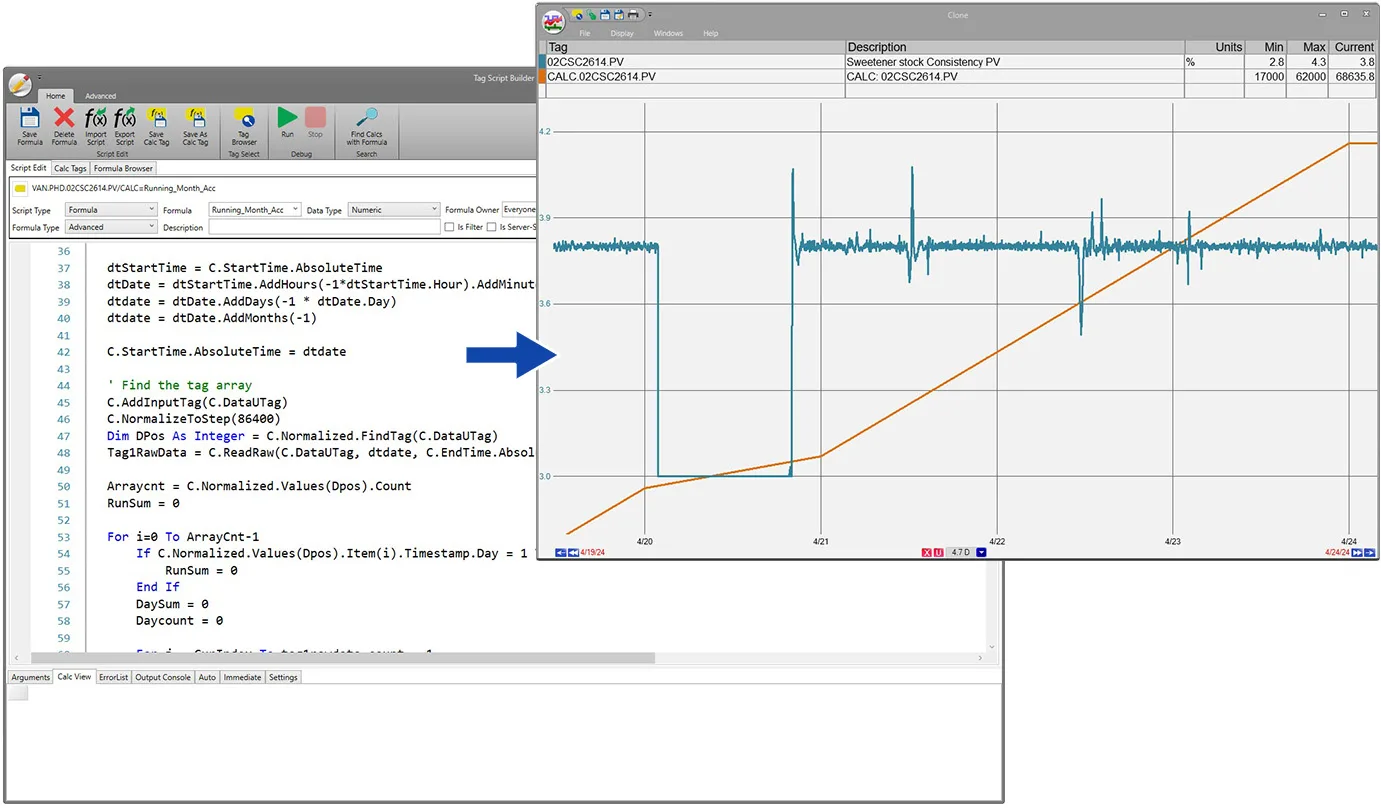
Perform Calculations for Informed Decisions
Perform precise calculations to support your troubleshooting and root cause analysis efforts.
- Calculate key performance indicators (KPIs)
- Use statistical methods to analyze data trends
- Model scenarios to predict potential outcomes
- Validate findings with accurate data analysis
Get to the Bottom of Recurring Problems with 5 Why Analysis
Apply the 5 Why analysis method to uncover the root causes of complex problems.
- Guide operators and engineers through a structured root cause process
- Capture reasoning and assign accountability
- Develop corrective actions aligned to true root cause
- Prevent recurrence with institutional knowledge
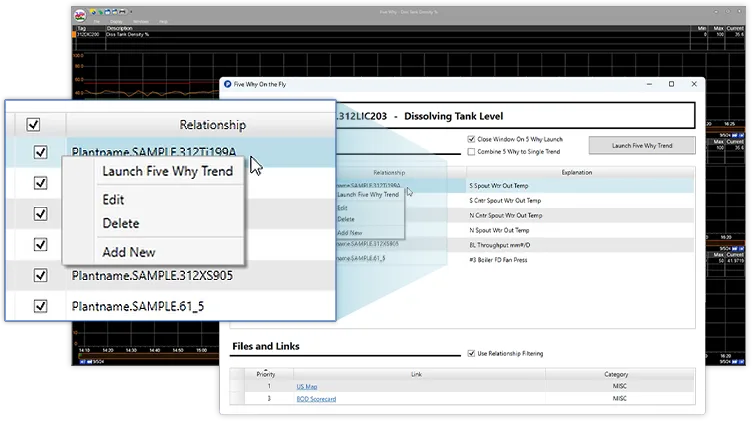
Featured Case Study
Kapstone Paper
The global containerboard market is highly competitive, making process optimization essential to a paper mill’s survival. KapStone’s technical team turned to dataPARC to help them centerline their process, identify golden runs, and reduce costs.
Powering Practical Analytics Solutions for 25+ Years
We mostly use dataPARC for troubleshooting and predictive maintenance.
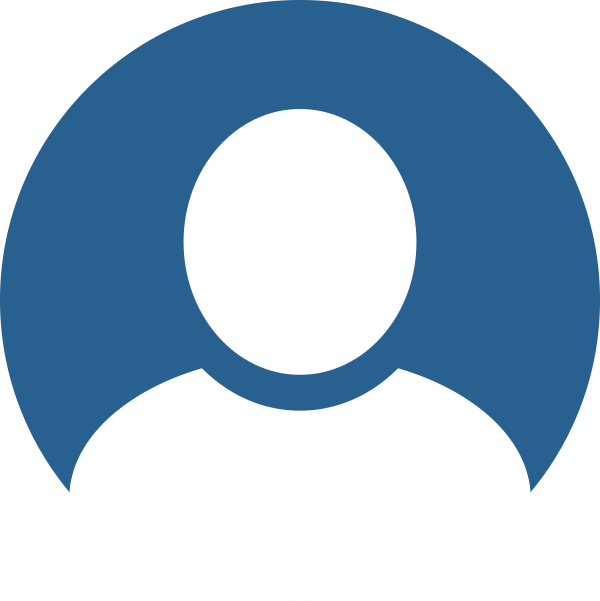
Anthony G
Instrumentation and Controls Technician
My favorite troubleshooting tool.
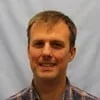
David C.
Controls & Automation Engineer
(I use dataPARC for) Root cause of deviation, optimizing process and understanding dynamics so we can control process variability.

Pami Singh
Director Process Optimization
The World’s Largest Manufacturers Depend on dataPARC
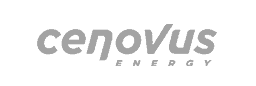
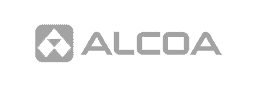
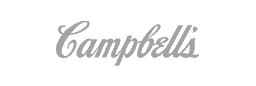
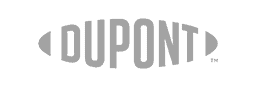
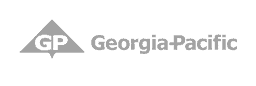
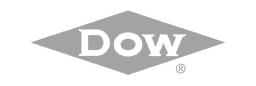
Beyond Troubleshooting
Tackle common manufacturing challenges with PARCview’s out-of-the box functionality.
OEE Tracking
Analyze production loss from unplanned downtime, poor quality, and performance issues.
Quality Control
Real-time quality control tools for continuous or batch manufacturing processes.
Additional Features
dataPARC is a flexible industrial analytics toolkit built upon the promise of easy data acquisition & integration. dataPARC’s core building blocks can be used to build any applications to meet your needs.
Dynamic Alarms & Notifications
Use dataPARC’s rule-based alarm engine to build smart alarm definitions that reliably detect compliance events, including data loss, real time, and aggregate exceedance of regulation limits. Forward alarm event data to PARCview’s Logbook, and send notifications via email or SMS.
Custom Report Builder
PARCview’s highly configurable scripting and scheduling application can schedule and deliver recurring reports or other key data to management and other decision-makers. Create event-triggered reports, dashboard report delivery, & scheduled reports.
Excel Add-In
Designed to automate common or tedious Excel tasks and make it easy to build reusable reports, PARCxla enables users to spend more time making important decisions and less time wrestling with data.
Manual Data Entry
PARCgraphics Designer’s form-based MDE tools offer a platform for constructing custom data entry screens. Enter data against a record from anywhere within the dataPARC environment, across multiple MDE pages, PCs, and locations.
Batch Analysis Tools
Arrange multiple batches by product into a comparison or consecutive view. Search for historical batches based on identifying information, such as batch ID or product label. Determine variability at any point in the batch using Run Trend analysis.
Control Charts
Build control charts (x-bar, range, standard deviation, etc.) from existing sources or PARCview formulas. Define simple min/max limits, choose from Western Electric Rules or custom logic. Limits can be managed natively in dataPARC or imported from a 3rd party database.
Download Our Overview Datasheet
Click the link below to receive a FREE overview on the benefits of using dataPARC to transform critical data into visual information for timely decision-making.
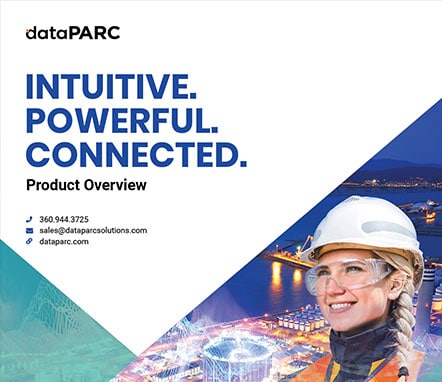