¿Qué es un gemelo digital en la fabricación de procesos?
En una publicación de blog anterior, explicamos que el lenguaje contemporáneo de la industria o las palabras de moda pueden crear confusión. Un ejemplo de una palabra de moda común en los procesos que puede causar confusión es el concepto de transformación digital de la fabricación o un "gemelo digital". Los clientes preguntan al respecto y los proveedores lo promocionan. Pero, ¿qué es exactamente un gemelo digital? Decidimos comenzar con la definición de Wikipedia:.
"Un gemelo digital es una simulación multifísica, multiescala y probabilística integrada de un vehículo o sistema as-built que utiliza los mejores modelos físicos disponibles, actualizaciones de sensores, historial de flota, etc., para reflejar la vida de su brillante gemelo correspondiente"
"Un gemelo digital es una réplica digital en tiempo real de un dispositivo físico"
De acuerdo con las definiciones, un gemelo digital puede variar desde una pantalla gráfica HMI que muestra datos en tiempo real del verdadero activo, hasta un modelo de simulación fundamental que permite el análisis de escenarios del tipo "qué pasaría si" en tiempo real sobre el activo.
El primer ejemplo es omnipresente y se logra de forma rápida y rentable. El segundo, sin embargo, es altamente especializado y requiere una cantidad considerable de esfuerzo para implementarlo.
Con la tecnología de gemelo digital que ofrece una amplia gama de posibilidades, definir una solución tipo gemelo digital dentro del sector de procesos de fabricación requiere un enfoque centrado. En la fabricación generalizada, los gemelos digitales podrían simplemente reflejar los sistemas físicos. En un proceso de producción, los gemelos digitales pueden diseñarse de manera elaborada para modelar procesos químicos y físicos complejos.
Estos modelos no solo replican un activo físico, sino que también simulan las interacciones entre diferentes variables del proceso en tiempo real. Esta capacidad permite una comprensión y optimización más profundas de los procesos que son críticos en industrias como la química, el petróleo y el gas, y la farmacéutica.
Por lo tanto, la solución específica de gemelo digital elegida debe corresponder directamente a los desafíos y objetivos únicos de la operación. Esto garantiza que la tecnología se aplique de una manera que maximice la eficiencia. Además de mejorar el mantenimiento predictivo y optimizar el rendimiento general de la producción
En lugar de considerar a un gemelo digital como una talla única, hágase esta pregunta: "¿Cuáles son mis necesidades de gemelos digitales?" Este es un caso clásico de no dejar que la tecnología defina su problema, sino dejar que su problema defina la tecnología.
Pasos para incorporar gemelos digitales en industrias de procesos
En muchos escenarios, tanto en la fabricación de procesos como en la industria de procesos en general, el objetivo final es equipar a los operadores de plantas y expertos en la materia con información digital integral. Cuanto más sepan sobre un activo, mejor serán la resolución de problemas y la optimización operativa.
Paso uno: Recopilación y almacenamiento de datos
El paso inicial para optimizar las operaciones a través de gemelos digitales implica una evaluación de datos. Es fundamental conocer las prácticas de recopilación y almacenamiento de datos de su instalación. Es imperativo que su planta esté equipada con un sólido historiador de datos. Uno que sea capaz de capturar y almacenar de forma segura los datos de todos los sensores críticos. Esta tarea fundamental es vital tanto para las plantas de fabricación como para las de la industria de procesos, ya que sustenta toda la infraestructura digital.
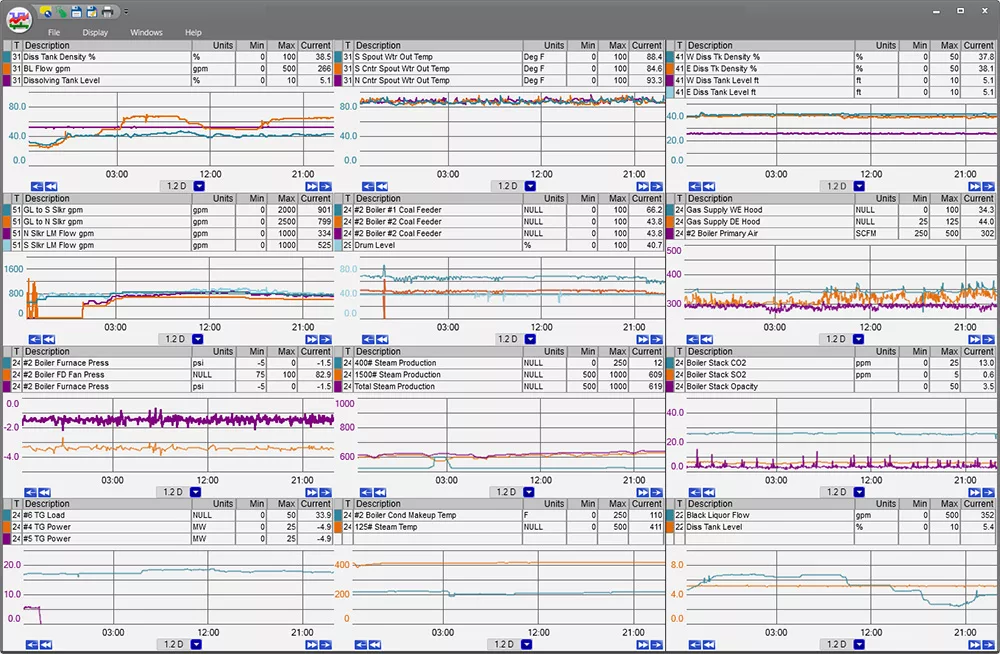
La visualización de tendencias múltiples que muestra datos en tiempo real solo es posible con la recopilación y el almacenamiento de datos. Esta visualización ayuda a realizar un seguimiento del rendimiento a lo largo del tiempo y sirve como la primera etapa para crear gemelos digitales precisos.
- Captura de datos exhaustiva: El historiador de datos no solo debe capturar todos los puntos de datos relevantes, sino que debe hacerlo con alta fidelidad y precisión. Esto incluye flujos de datos continuos de sensores de temperatura, manómetros, medidores de flujo y analizadores químicos, entre otros. La salida de cada sensor debe registrarse con precisión en tiempo real. A continuación, se pueden realizar análisis posteriores basados en conjuntos de datos fiables y completos.
- Escalabilidad y accesibilidad: La solución de almacenamiento de datos debe ser escalable para adaptarse a volúmenes crecientes de datos a medida que se integran nuevos sensores y puntos de datos a lo largo del tiempo. También debería facilitar el acceso a los datos históricos para su análisis. Los operadores e ingenieros pueden recuperar y analizar datos de rendimiento anteriores con rapidez, para identificar patrones, tendencias y anomalías.
- Capacidad de integración: Los historiadores de datos efectivos deben integrarse sin problemas con otros sistemas operacionales, como los sistemas ERP, los sistemas de gestión de mantenimiento y las plataformas analíticas avanzadas. Esta capacidad de integración permite la gestión holística de los datos operativos. Los datos de diversas fuentes se pueden correlacionar y analizar exhaustivamente.
Al garantizar que su instalación recopile y almacene adecuadamente los datos de todos los sensores críticos en un historiador de datos eficiente y seguro, establece una base sólida para aprovechar las tecnologías avanzadas de gemelos digitales. Esto mejora la supervisión y el monitoreo en tiempo real. También aumenta de manera considerable la capacidad de la planta para el mantenimiento predictivo y la optimización operativa.
Paso dos: Contextualización de datos
Ahora que las plantas que han implementado con éxito sistemas integrales de recopilación de datos. El desafío posterior para configurar la fabricación de gemelos digitales radica en la contextualización efectiva de estos datos. La contextualización es más que solo organización de datos; se trata de transformar datos sin procesar en inteligencia procesable. Este proceso implica varios pasos clave, cada uno diseñado para mejorar la accesibilidad y la relevancia de los datos para la toma de decisiones operativas.
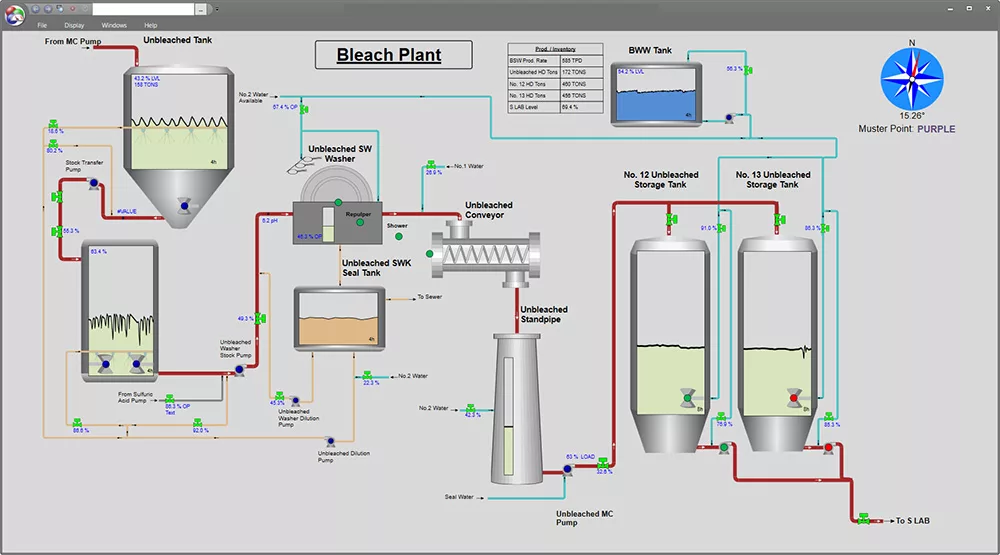
Los diagramas de procesos ilustran cómo se contextualizan los datos para proporcionar una representación clara y visual de operaciones complejas. Al integrar los datos en tiempo real en las imágenes del proceso, los operadores pueden comprender mejor el rendimiento y tomar decisiones informadas.
- Organización específica del activo: El primer paso en la contextualización es categorizar los datos según activos específicos. Esto es necesario para crear gemelos digitales. Los datos deben ser específicos del activo. Esto significa que todos los puntos de datos relacionados con una máquina, línea de producción o sistema en particular se agrupan. Esta organización permite un monitoreo y análisis más fácil del rendimiento, las necesidades de mantenimiento y la eficiencia operacional de cada activo.
- Filtración y agregación de datos: Una vez organizados, los datos deben filtrarse y agregarse para eliminar el ruido y resaltar las tendencias importantes. El procesamiento de datos puede implicar descartar lecturas atípicas que podrían sesgar el análisis. Si bien la agregación podría significar resumir los datos por hora en promedios o turnos diarios. Estos procesos son cruciales para destilar las grandes cantidades de datos recopilados en formas que sean manejables y significativas.
- Mejora de la accesibilidad: El siguiente aspecto de la contextualización es garantizar que los datos sean fácilmente accesibles en el entorno virtual. Tener que capturar datos solo para tenerlos en silos anula la utilidad de la visibilidad en tiempo real. Esto implica implementar interfaces fáciles de usar que permitan a los operadores, ingenieros y administradores recuperar e interpretar datos rápidamente en función de sus funciones y necesidades específicas. Las herramientas de visualización eficaces, como los dashboards y los gráficos interactivos, pueden ayudar a crear una representación digital de la planta o el activo de la fábrica.
- Integración significativa: Más allá de los puntos de datos individuales, la contextualización también implica integrar datos en todos los sistemas para proporcionar una visión holística de las operaciones. Esto podría significar vincular los datos de salida de producción con las mediciones de control de calidad o correlacionar los registros de mantenimiento con las métricas de rendimiento del equipo. Dicha integración es crucial en entornos de procesos donde las operaciones dependen en gran medida de la comprensión precisa de cómo interactúan varios parámetros del proceso
Al contextualizar los datos de manera efectiva, las plantas pueden garantizar que su gran cantidad de información no solo se almacene. Se utiliza activamente para mejorar la toma de decisiones y la eficiencia operacional. En entornos de procesos, donde las interdependencias de las variables son complejas y el costo de los errores puede ser elevado, la capacidad de interpretar y actuar rápidamente sobre datos precisos y contextualizados es invaluable
Paso tres: Integración de datos digitales adicionales
Más allá de los conocimientos inmediatos proporcionados por los datos de los sensores en tiempo real, en la fabricación inteligente existe una gran reserva de "datos digitales" que. Cuando se aprovechan estos datos del mundo real, pueden amplificar de manera considerable las capacidades operativas. Tanto el sector de fabricación como el de servicios públicos dentro de la industria de procesos pueden beneficiarse. Esto incluye fuentes de datos tanto fuera de línea como históricas que enriquecen las interpretaciones de datos en tiempo real.
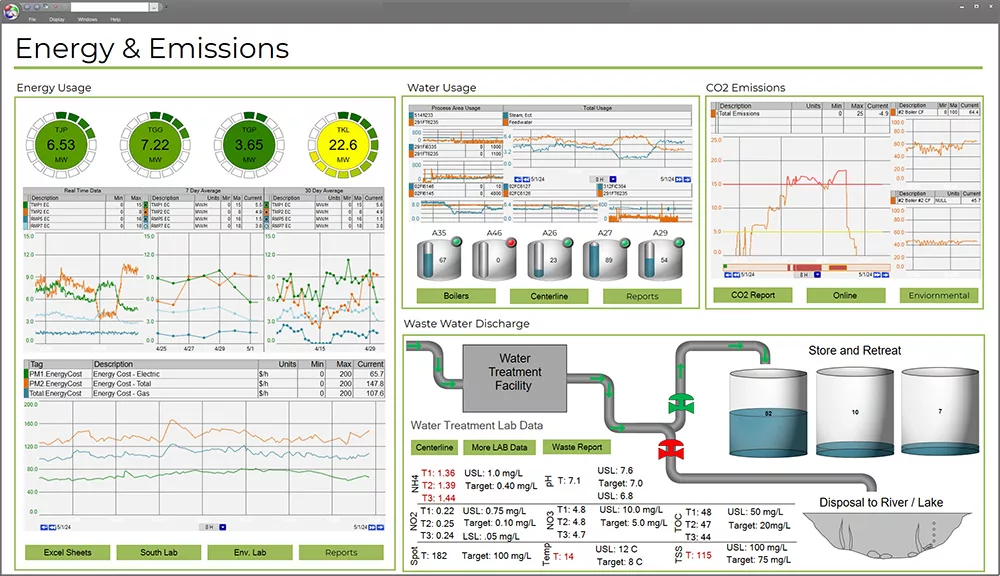
Los gráficos generales pueden mostrar procesos integrados y datos de laboratorio en una sola pantalla. Esto proporciona una visión holística de la eficiencia operacional, lo que permite el monitoreo y la toma de decisiones en tiempo real tanto para la gestión de la energía como para el cumplimiento ambiental
- Integración de datos sin conexión: Los sistemas tales como los Sistemas de gestión de información de laboratorio (LIMS) desempeñan un papel fundamental en la gestión de datos de laboratorio y de calidad, que son cruciales para validar la calidad del producto y el cumplimiento de los estándares de la industria. Estos sistemas recopilan y almacenan lotes de datos de diversas pruebas y procesos. Se dispone de un registro histórico detallado que se puede analizar para identificar tendencias, anomalías o áreas de mejora. Por ejemplo, correlacionar los datos de LIMS con los datos de producción puede ayudar a identificar las causas fundamentales de los problemas de calidad. Puede agilizar las operaciones y mejorar la consistencia del producto.
- Vinculación de contenido digital con activos físicos: La integración de estos gemelos digitales y datos con activos físicos a través de plataformas avanzadas permite una estrategia operativa más cohesionada. Por ejemplo, cuando una máquina alerta sobre una necesidad de mantenimiento, el sistema puede sugerir automáticamente los SOP relevantes. O puede profundizar en los registros de mantenimiento históricos, lo que facilita una toma de decisiones más rápida e informada. Además, los materiales de capacitación se pueden adaptar a los desafíos operativos específicos identificados a través del análisis de datos, apoyando el aprendizaje y la mejora continua.
Al aprovechar todo el espectro de datos digitales disponibles, las empresas de fabricación de la industria de procesos pueden transformar sus operaciones. Reducción de costos y ahorro de tiempo. Este enfoque aumenta la eficiencia y la eficacia del día a día. También puede fomentar una cultura de mejora continua e innovación, lo que en última instancia conduce a la excelencia operativa sostenida.
Siguiendo estos pasos, las plantas mejoran la gestión de activos mediante la fabricación de gemelos digitales. Continúan impulsando avances significativos en la eficiencia y efectividad operacional.
Ejemplos de la industria de procesos de gemelos digitales
Un cliente de la industria del papel con el que hemos trabajado se ha aprovechado de expertos centralizados en la materia para sus operaciones unitarias.
Hay varios procesos complicados y distintos que se requieren para convertir una astilla de madera en un producto terminado. No es factible contar con un experto en cada una de estas operaciones en cada sitio. El proceso de evaporación es un buen ejemplo. Consume mucha energía y en muchos lugares es un cuello de botella de producción.
Para garantizar el éxito, el cliente creó un modelo de la información necesaria para cada evaporador. En este caso, la información incluía los sospechosos habituales de datos históricos y de calidad de laboratorio, organizados en una estructura de activos. También incluía un conjunto común de contenido para cada sitio, utilizado de manera central por el SME (experto en la materia) y en el sitio:
- Gráfico de proceso de alto rendimiento
- Descripción detallada de la tendencia
- Condiciones específicas de operación
- Notificaciones automatizadas
De particular valor fue el Gráfico de proceso de alto rendimiento. Es una representación exacta de cada sitio, creada mediante el uso de diagramas de flujo de procesos, pantallas del operador y P&ID. Esta representación detallada permitió al SME (experto en la materia) remoto comunicarse con los equipos de operaciones y mantenimiento en el sitio de manera efectiva.
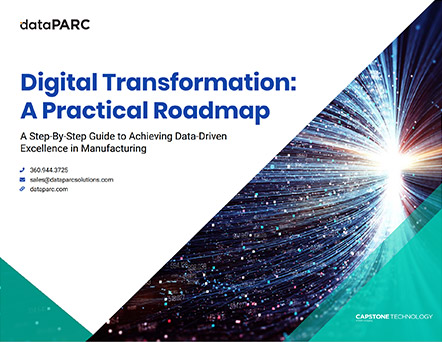
¿Integración de datos de IT y OT en su planta? Deje que nuestra hoja de ruta de transformación digital lo guíe.
En muchos casos, este gráfico contenía la información normalmente representada en 10 a 12 pantallas DCS y se visualizaba de manera óptima con un monitor 4K. La combinación de las herramientas de análisis de datos adecuadas y el acceso a este "gemelo digital" permitieron que el monitoreo remoto tuviera éxito. La empresa pudo aprovechar la infraestructura existente sin costosos gastos de extracción y reemplazo, lo cual era fundamental dada su variedad de sistemas (múltiples proveedores para historiadores y laboratorios/calidad).
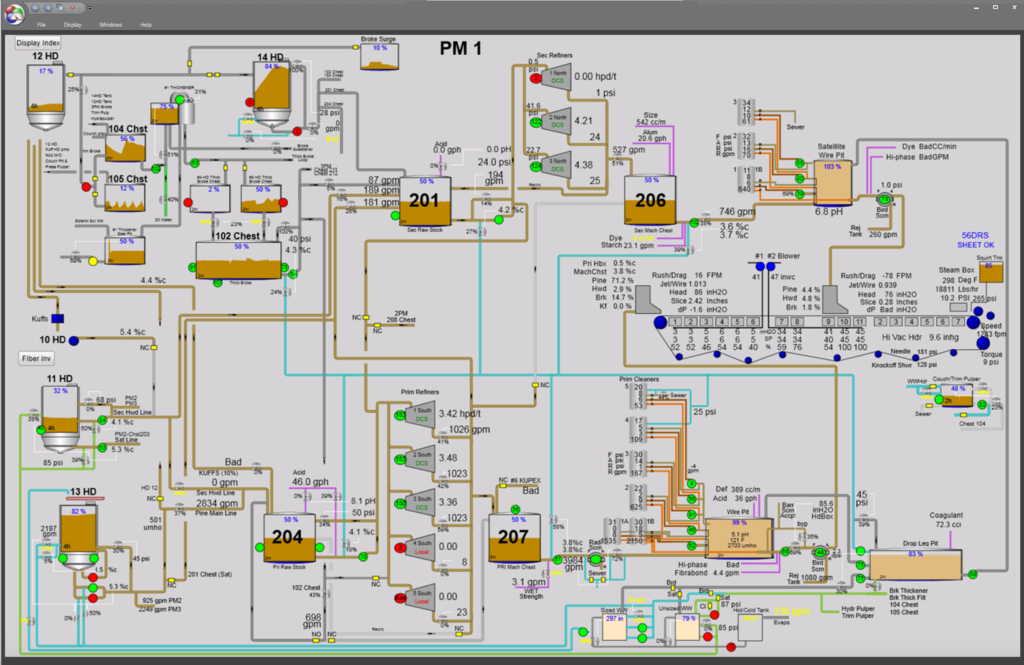
Las pantallas generales integrales sustituyen a varias pantallas DCS en un monitor 4K. Esta es una ventaja clave de los gemelos digitales, que permite una mayor visibilidad operativa. Los operadores pueden monitorear varios procesos simultáneamente y tomar decisiones más informadas basadas en datos en tiempo real.
En un ejemplo específico, tenían contaminación por condensado en el back-end. Debido a una pantallas de tendencias completa, todo en uno, el operador detectó un cambio que ocurrió en el front-end mientras que la contaminación ocurrió en el back-end.
El operador encontró algo relacionado con el problema, pero no entendía por qué. Esta discusión surgió en una sesión de capacitación para operadores. Con la pantalla gráfica completa, todo en uno, fue fácil demostrar por qué el cambio que el operador observó en el front-end del conjunto era un problema en el back-end del conjunto.
Una vez que el operador entendió la interacción, inmediatamente supo cómo solucionar el problema, lo que requirió apagar el activo. Fue un gran ejercicio de capacitación para todos en la clase y se necesitó una combinación de personas además de un "gemelo digital" para resolver el problema rápidamente.
Gemelo digital para transmitir conocimientos y procesos heredados
Otra área sobre la que se nos pregunta cada vez más son las herramientas digitales para capturar el conocimiento inherente de la fuerza laboral. El desafío podría ser la llamada "fuga de cerebros" creada por una ola de trabajadores jubilados, el deseo de mover eficientemente a los trabajadores de un sitio a otro u otras razones convincentes.
La oportunidad de transmitir de manera eficiente el conocimiento de su operador más experimentado o experto en la materia a todos en la planta ofrece un valor significativo. Esto puede venir en forma de una capacitación más rápida para los nuevos empleados y un menor número de llamadas al SME (experto en la materia) que está de guardia disfrutando de sus vacaciones.
Como mínimo, tiene una fuerza laboral más feliz y, en última instancia, su planta funciona de manera mucho más eficiente con una fuerza laboral feliz. De cualquier manera, ¡es una victoria!
Como ejemplo, recientemente tuvimos un cliente que implementó una iniciativa que llamaron "5 por qué". Descubrieron que consistentemente se resolvería un problema en su proceso, pero se perdería el conocimiento sobre la solución.
La operadora en servicio la primera vez sabía inherentemente cómo resolver el problema, pero ese conocimiento no era conocido por nadie más. Entonces, cuando el problema volviera a ocurrir, no se resolvería con prontitud.
Para resolver esto, ahora tiene una capacidad que permite a cualquier persona en la planta crear relaciones de tags y vincular recursos externos (SOP, capacitación, páginas de intranet, etc.) y luego acceder fácilmente a estas relaciones. El resultado es un conocimiento viviente para el proceso.
Beneficios del uso del gemelo digital para la industria de procesos
En resumen, la entrega de un gemelo digital es un concepto interesante. Los usuarios han estado aprovechando esta capacidad durante veinte años.
La resolución de problemas no es nueva, pero la reducción de costos y la innovación continua hacen que sea cada vez más fácil para las plantas aprovechar el gemelo digital y funcionar de manera más eficiente con una mayor rentabilidad.
¿Tiene curiosidad por saber qué puede hacer un gemelo digital por su negocio? Contáctenos hoy y exploraremos las posibilidades del gemelo digital que dataPARC puede ofrecerle en sus instalaciones.