Reducir el tiempo de inactividad aumenta la productividad, reduce los costos y disminuye los accidentes. El software de seguimiento del tiempo de inactividad se puede utilizar para ayudar a reducir el tiempo de inactividad. Es imprescindible saber por qué está fallando el proceso para reducir el tiempo de inactividad.
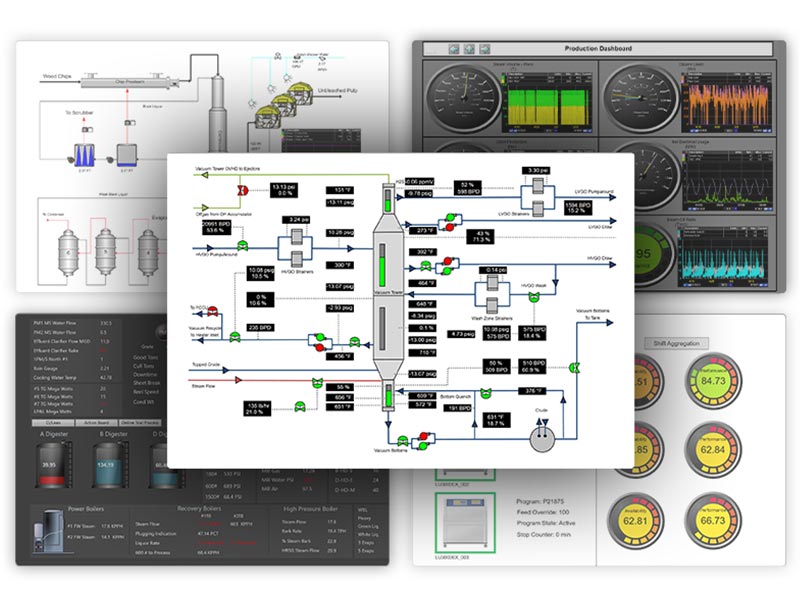
Supervise, informe y analice las pérdidas de producción por tiempo de inactividad no planificado, mala calidad y problemas de rendimiento.
¿Qué es el tiempo de inactividad?
El tiempo de inactividad es cualquier duración en la que un proceso no se está ejecutando. Sin embargo, no todo el tiempo de inactividad se crea por igual. Hay dos tipos de tiempo de inactividad: planificado y no planificado.
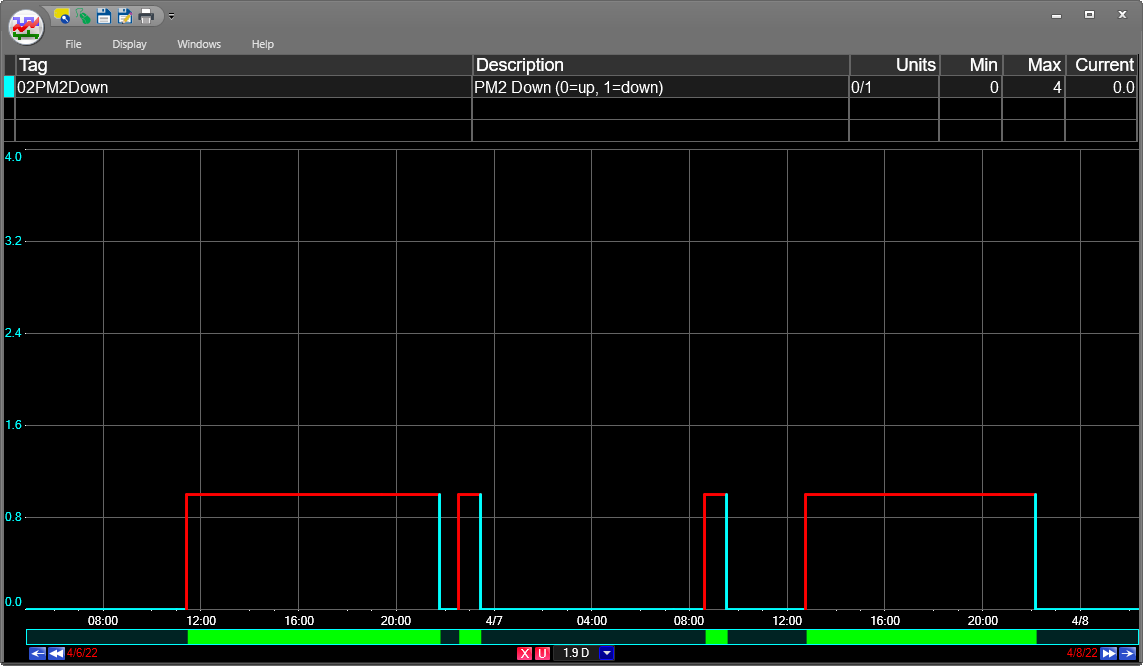
Eventos de tiempo de inactividad representados de manera visual en el software de tendencias de procesos de dataPARC.
¿Qué es el tiempo de inactividad planificado?
El tiempo de inactividad planificado es cuando la producción programa un tiempo para detener el proceso. El tiempo de inactividad planificado es necesario para el mantenimiento de la maquinaria, al realizar inspecciones, limpiar y reemplazar piezas.
El tiempo de inactividad planificado permite a las operaciones organizar, programar y prepararse para el tiempo de inactividad. Pueden coordinar con los contratistas, pedir piezas y planificar tareas que deben completarse mientras el proceso está inactivo. Los tiempos de inactividad planificados se pueden organizar para que el personal tenga tareas que realizar y las herramientas necesarias a mano.
¿Qué es el tiempo de inactividad no planificado?
El tiempo de inactividad no planificado es cuando la máquina o el proceso están inactivos por cualquier evento no programado. Esto puede deberse a la rotura de una pieza, falta de material, corte de energía, etc. El tiempo de inactividad no planificado es impredecible y debe abordarse cuando se busca reducir el tiempo de inactividad general.
Importancia de reducir el tiempo de inactividad no planificado
El tiempo de inactividad no planificado es significativamente más costoso y peligroso que el tiempo de inactividad planificado. Dado que el tiempo de inactividad no planificado es impredecible y el proceso podría detenerse por numerosas razones, es imposible estar preparado para cada situación.
Esperar a las piezas o al personal necesario para solucionar un problema lleva tiempo y podría implicar que la máquina permanezca parada durante más tiempo. Un tiempo de inactividad más largo significa menos tiempo para fabricar el producto, lo que afecta directamente en el resultado final.
Otro costo atribuido a los tiempos de inactividad no planeados es el producto fabricado que no puede venderse y el material desperdiciado. El tiempo justo antes, en el momento del tiempo de inactividad y la puesta en marcha del proceso, tiende a generar un producto de mala calidad.
El tiempo de inactividad no planificado puede atribuirse a cuasi accidentes o accidentes. Durante el tiempo de inactividad no planificado, el objetivo es que la máquina/proceso vuelva a funcionar lo antes posible. Esta presión puede crear un entorno estresante y caótico, lo que hace que las personas reaccionen en lugar de detenerse a pensar en el mejor plan a futuro.
Reducir el tiempo de inactividad no planificado puede ayudar a reducir los costos operativos generales. También reduce los tiempos en que los empleados se encuentran en situaciones impredecibles, y disminuye la probabilidad de que ocurra un accidente.
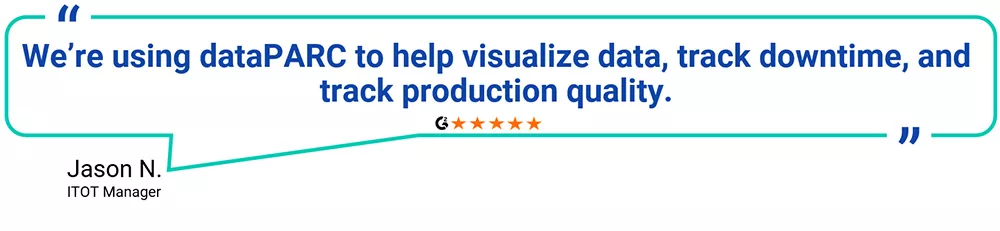
Cómo reducir el tiempo de inactividad
Existen numerosas razones para que se produzca un tiempo de inactividad del proceso y es posible que sea necesario implementar múltiples enfoques en el esfuerzo por reducirlo.
1. Seguimiento del tiempo de inactividad
Antes de ver los pasos para reducir el tiempo de inactividad, es fundamental realizar un seguimiento. El seguimiento del tiempo de inactividad le permite ver por qué el proceso está fallando y proporciona una métrica que indica si se está mejorando o no.
Los datos recopilados en el seguimiento del tiempo de inactividad se utilizarán para ayudar a reducirlo. Considere recopilar los siguientes datos para cada ocurrencia de inactividad:
- Duración
- Motivo/causa
- Producto en el momento de la inactividad
- Área de proceso
- Turno o cuadrilla
- Comentarios del operador
- Otros atributos tales como ocurrencias ambientales debido al tiempo de inactividad, residuos recolectados durante la duración, problemas de seguridad, etc.
Estos datos se pueden recopilar manualmente; sin embargo, tener un sistema automatizado garantizará que los datos se recopilen para cada evento. Unos datos más coherentes ayudarán a reducir el tiempo de inactividad.
El software de seguimiento del tiempo de inactividad puede automatizar y ayudar a organizar el tiempo de inactividad. Algunas consideraciones al investigar el software de seguimiento del tiempo de inactividad:
- Facilidad de uso
- Captura automáticamente los eventos de tiempo de inactividad
- Registra la causa del tiempo de inactividad y otros datos
- Analiza datos y eventos
- Se integra con los datos del proceso
Hay muchas opciones de software de seguimiento de tiempo de inactividad en el mercado. Algunas son aplicaciones dedicadas al seguimiento del tiempo de inactividad, mientras que otras, como PARCview de dataPARC, pueden ofrecer una suite de herramientas de análisis de fabricación que incluyen un módulo de seguimiento del tiempo de inactividad. La elección correcta es la que se utilizará de manera consistente.
¿Busca mejorar el OEE? Obtenga La guía completa del OEE y obtenga todo lo que necesita para implementar, analizar y mejorar con éxito el OEE en su planta.
2. Monitoreo de la producción
Tener un sistema para monitorear la producción también puede ayudar a reducir el tiempo de inactividad.
Las tendencias visibles del proceso en las estaciones del operador dan una indicación visual de cómo se está ejecutando el proceso a lo largo del tiempo y si las variables están migrando o se mantienen consistentes.
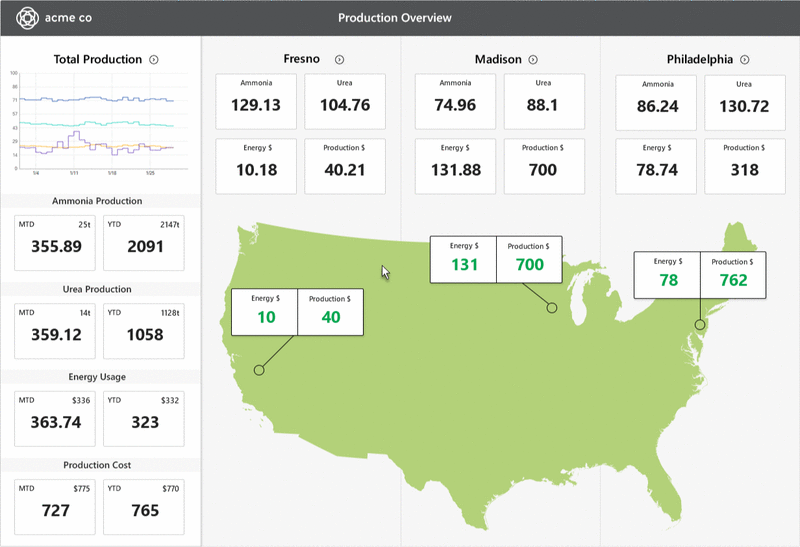
Los dashboards de producción en tiempo real se pueden utilizar para mostrar datos de calidad, con lo cual se transmite información directamente desde el laboratorio a las operaciones. Esto garantiza que el producto esté continuamente dentro del estándar de calidad.
Las alarmas se pueden usar de forma independiente o junto con tendencias y dashboards para advertir a los operadores cuando se producen condiciones molestas. Esto puede permitirles reaccionar más rápidamente, lo que podría evitar que se produzca un tiempo de inactividad.
3. Creación de un programa de mantenimiento preventivo
El mantenimiento preventivo ocurre durante el tiempo de inactividad planificado o mientras el proceso se está ejecutando. El reemplazo de piezas durante el tiempo de inactividad planificado permite al sitio ordenar las piezas necesarias y asegurarse de que el personal adecuado esté en el sitio para realizar las tareas, lo que ahorra tiempo y dinero.
El mantenimiento regular cuando el proceso está funcionando, como la adición o el cambio de aceites lubricantes y la limpieza pueden ayudar a aumentar la vida útil de las piezas.
Una vez que se crea una programación, se puede realizar un seguimiento para garantizar que se realicen las tareas. MDE (Entrada manual de datos de PARCview) se puede configurar en un horario e integrarse con alertas. Si se omite una tarea, se puede enviar un mensaje de recordatorio al operador o escalarlo a un supervisor.
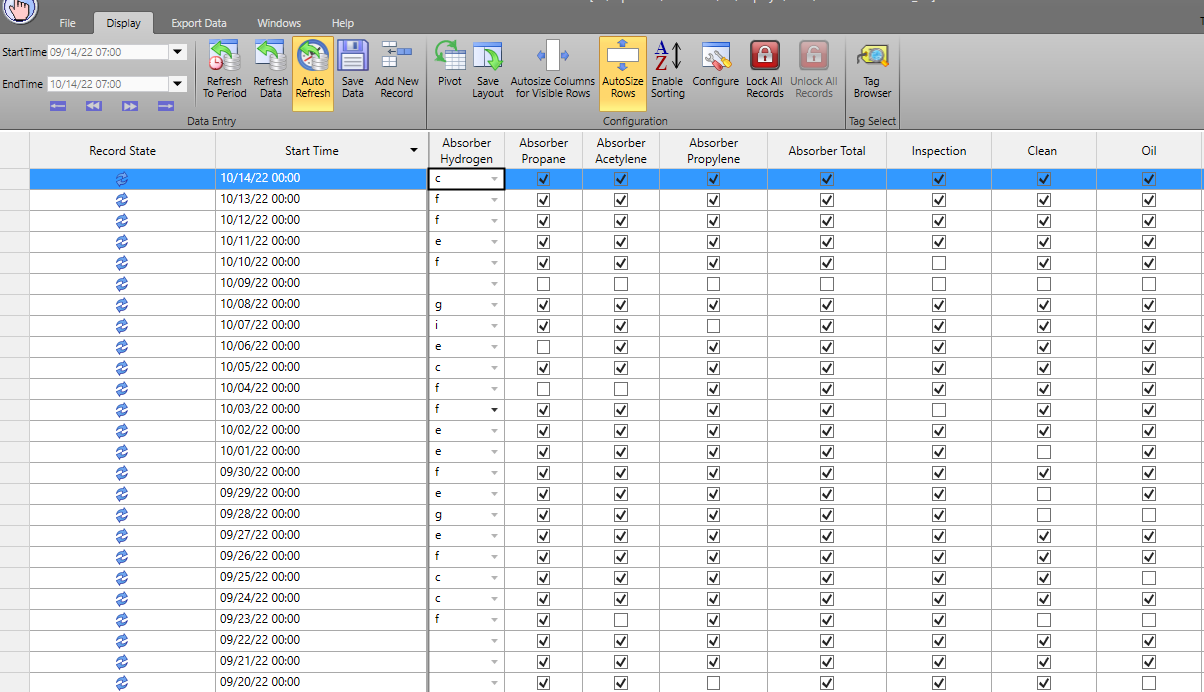
Los datos de mantenimiento se pueden capturar y digitalizar para ayudar a predecir los eventos de tiempo de inactividad para el desarrollo de programas de mantenimiento preventivo.
El registro de datos de mantenimiento preventivo permite a los sitios analizarlos junto con el tiempo de inactividad y los datos de proceso. Las correlaciones pueden aparecer y ayudar a impulsar el mantenimiento necesario, además de reducir el tiempo de inactividad.
4. Proporcionar apoyo en la toma de decisiones del operador
Los eventos de inactividad no planificados son inevitables y no se pueden eliminar completamente, por lo que una prioridad para reducir el tiempo de inactividad también debería ser reducir la duración cuando se produce un evento de inactividad.
Crear herramientas y guías de solución de problemas para que los operadores las utilicen en caso de una caída ayudará a que el proceso vuelva a funcionar más rápidamente.
Para que el proceso se lleve a cabo, los operadores deben saber por qué se detuvo en primer lugar. Proporcionar a los operadores los recursos necesarios para encontrar la causa raíz es clave para resolver el problema rápidamente.
Los dashboards de procesos, el análisis de tendencias de los 5 por qués (5-Why) y los flujos de trabajo pueden ayudar a determinar la causa raíz.
Las tendencias, los dashboards y las líneas centrales pueden llamar la atención sobre los cambios significativos en el proceso. La visualización de Centerline de dataPARC es un informe tabular con estadísticas basadas en ejecuciones. Este formato ayuda a garantizar que el proceso sea coherente y pueda señalar variables que se ejecutan fuera de las condiciones o límites operativos anteriores.
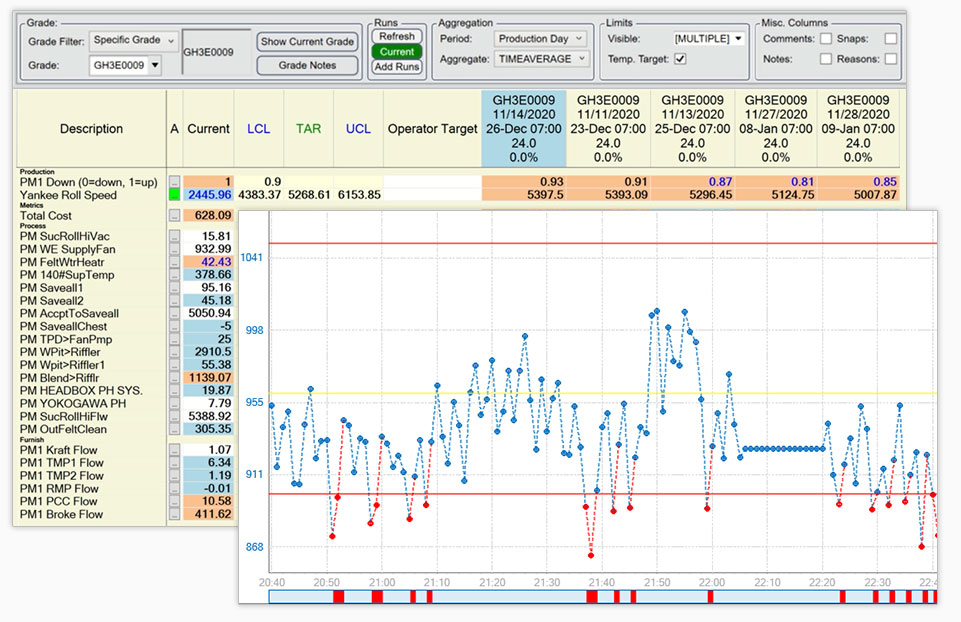
Las líneas centrales (Centerlines) probaron la detección temprana de fallas y las advertencias de desviación del proceso, por lo que los operadores pueden responder rápidamente para reducir los eventos de tiempo de inactividad no planificados.
Un flujo de trabajo o un análisis de los 5 por qués (5-Why) preconfigurado también pueden ayudar a señalar la causa raíz y la solución sugerida.
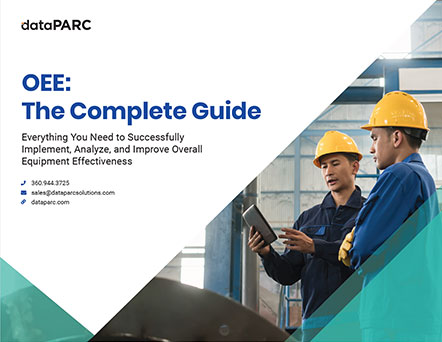
Todo lo que necesita para implementar, analizar y mejorar con éxito la eficacia general del equipo.
5. Realización del análisis DMAIC
Las sugerencias anteriores son puntos de partida para reducir el tiempo de inactividad. Si se implementan, se puede utilizar el proceso DMAIC (Definir, Medir, Analizar, Mejorar, Controlar). Es una herramienta fundamental de Lean Manufacturing y se puede utilizar para ayudar a reducir el tiempo de inactividad.
Definir
Primero, el proceso, cuando el proceso se considera inactivo, y se debe definir una lista de posibles razones.
Para cada proceso, determinar cómo se identifica: está o no en ejecución.
Para muchos softwares de seguimiento de tiempo de inactividad, se necesita una etiqueta/variable para indicar cuándo se considera que el proceso está inactivo. Si no existe una etiqueta específica, considere una utilidad que alimente el proceso, como vapor, agua o presión. Siempre que haya un valor claro que indique que el proceso se está ejecutando o no, se puede usar esa variable.
También es necesario hacer una lluvia de ideas sobre una lista de posibles razones del tiempo de inactividad antes de realizar un seguimiento de los eventos. Esta lista/árbol de razones puede compartirse o ser única para cada área de proceso.
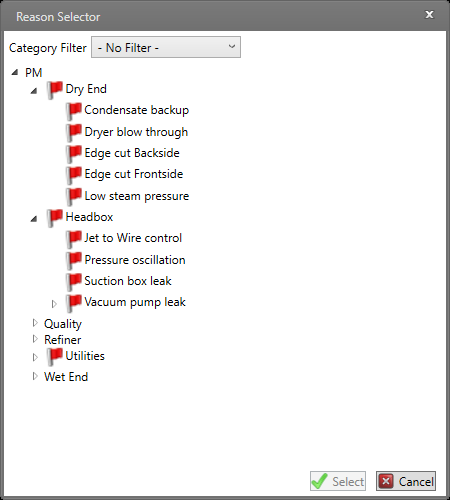
Asignar razones a los eventos de tiempo de inactividad proporciona datos que se pueden utilizar para reducir el tiempo de inactividad en el futuro.
Estas razones deben incluir causas planificadas y no planificadas. Durante la fase de análisis, las razones planificadas se pueden filtrar para centrarse en el tiempo de inactividad no planificado. Para obtener más información sobre cómo crear un árbol de razones, consulte los 5 pasos para aprovechar el potencial de sus datos.
Medir
Medir y asignar una razón al tiempo de inactividad es un paso crítico para poder reducirlo. Tener un software robusto de seguimiento del tiempo de inactividad ayudará a que la medición de dicho tiempo sea más fácil. Asegúrese de capturar el quién, qué, cuándo, dónde y por qué del evento de tiempo de inactividad.
Una vez que el software de seguimiento del tiempo de inactividad registra el evento de tiempo de inactividad, se puede asignar un motivo.
Algunos sistemas pueden asignar automáticamente motivos basados en un código de error de la máquina. Los usuarios pueden verificar el motivo o seleccionarlo en el árbol de motivos predefinido.
Puede ser útil capturar información adicional para la fase de análisis. Puede considerar permitir que los usuarios escriban comentarios de forma libre además de la razón predefinida para explicar mejor por qué ocurrió un evento de tiempo de inactividad. Si se utiliza PARCview, el campo de evidencia se puede configurar para capturar otros datos importantes del proceso durante la duración del evento.
Analizar
Ahora que se registra y categoriza el tiempo de inactividad, se puede analizar. Los diagramas de Pareto son útiles cuando se analizan eventos de tiempo de inactividad. Los datos se pueden graficar en un pareto por duración o recuento de eventos.
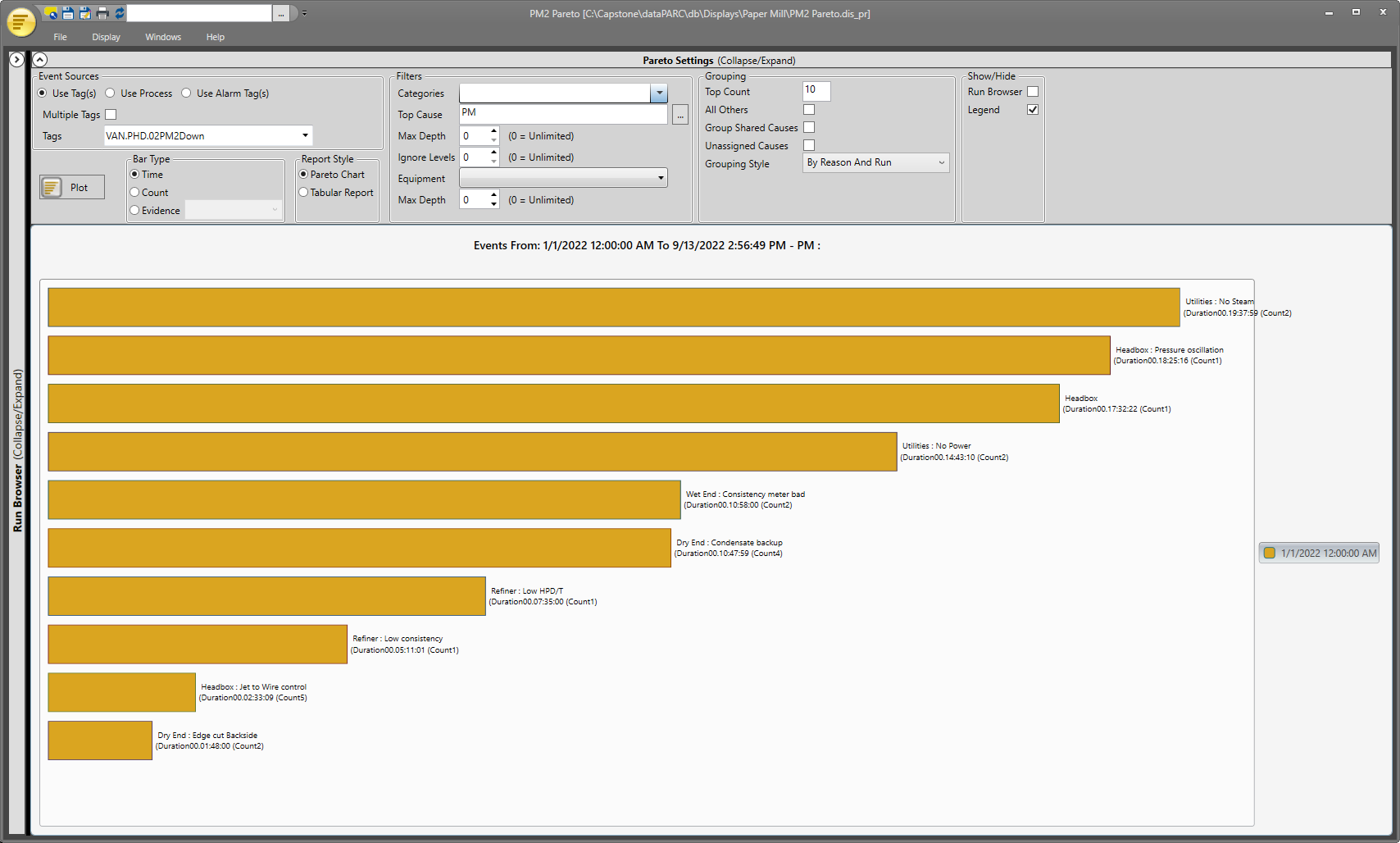
Los diagramas de Pareto pueden ayudarlo a analizar los eventos de tiempo de inactividad y conocer las causas más importantes del tiempo de inactividad.
Tenga en cuenta otros datos clave del proceso, como las preocupaciones de seguridad, los riesgos ambientales o el material desperdiciado, además de la duración de los eventos para ayudar a determinar qué causa del tiempo de inactividad será más beneficiosa para abordarla y reducirla.
No siempre es el motivo con la mayor cantidad de minutos totales el que debería abordarse.
Tomemos, por ejemplo, un evento que causó 15 horas de inactividad pero se debió a una parte débil; es poco probable que vuelva a suceder frente a una causa que ocurre mensualmente pero que solo da como resultado unos 75 minutos de inactividad en cada evento. Será más beneficioso mejorar el evento recurrente.
Mejorar
Cuando busque formas de reducir una causa de tiempo de inactividad, busque cómo evitar que ocurra el evento en primer lugar y cómo hacer que el proceso vuelva a funcionar cuando ocurra el evento. Ambos enfoques son necesarios para reducir el tiempo de inactividad.
Piense en la frecuencia de las inspecciones, las limpiezas, cuánto duran las piezas y si se puede programar su reemplazo en lugar de esperar a que fallen mientras el proceso se está ejecutando. Consulte el programa de mantenimiento preventivo y actualícelo según sea necesario.
Determine la mejor manera de reducir las causas de tiempo de inactividad más impactantes o reducir el efecto. Una matriz de pagos puede ayudar a señalar las soluciones más impactantes y menos costosas.
Control
Continúe midiendo y analizando el tiempo de inactividad para asegurarse de que los artículos que se han reducido no comiencen a aparecer de nuevo. Repita el ciclo y señale otro motivo. Se pueden crear flujos de trabajo y SOP (procedimientos operativos estándar) para ayudar a mantener el control.
Conclusión
Para reducir el tiempo de inactividad no planificado se requieren varios enfoques; encontrar las herramientas y el software adecuados para el seguimiento y la supervisión son la clave para reducir el tiempo de inactividad. Los datos son necesarios para impulsar la mejora, tanto para evitar que ocurran eventos futuros como para reducir la duración cuando el proceso se interrumpe.
Un software de seguimiento del tiempo de inactividad puede ayudar a guardar, organizar y revisar los eventos de tiempo de inactividad, lo que le permite reducir de manera más efectiva el tiempo de inactividad en su proceso de fabricación. PARCview de dataPARC integra el seguimiento del tiempo de inactividad y el monitoreo de procesos en un programa fácil de usar.
OEE: La guía completa
Todos los recursos que necesita para implementar, analizar y mejorar con éxito la efectividad general del equipo.
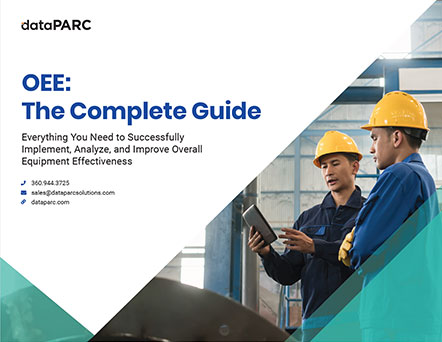