一旦制造过程被 中心线化 且运行相对良好,便到了采取下一步行动的时机-测量并跟踪重要的产品特性。一种跟踪方法是使用过程 控制图。
控制图的主要目的是帮助判断过程是否稳定(在控)或不稳定(失控)。当过程稳定(在控)时,意味着它是可预测的,只受正常随机变异因素的影响。不稳定(失控)的过程同样受到这些常见变异因素的影响,但还受到“特殊”或“可分配”原因的影响。如果您成功地将所有重要过程变量中心线化,并且原材料输入相对一致,那么您的过程应当是稳定(在控)的。
控制图基础
控制图包含一个重要可量化产品特性的时序趋势。除了该特性的个别数据点外,它还包括基于历史数据(当时过程“在控”)计算的三条线:中间的线对应数据的平均值,另外两条线(控制上限和控制下限)分别代表平均值加减 3σ,其中 σ 等于标准差。
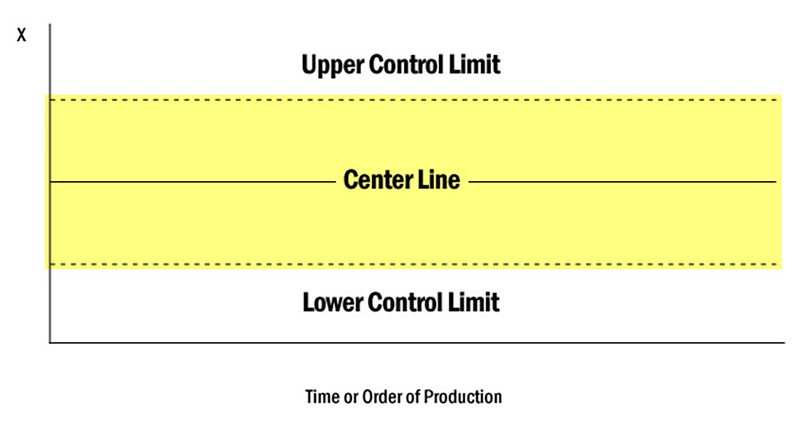
控制图的理论基础
标准差或 σ 表示数据相对于其平均值的分散程度。 Walter A. Shewhart 指出,当过程稳定(在控)时,理论上超过 99% 的工艺值应落在 3σ 控制限内。若某个值超出这些限制,则表明存在异常或特殊原因,需要对过程进行调整或采取纠正措施。数据呈现上升或下降趋势、周期性模式等非随机模式时,也表明存在特殊原因。
已开发出几种不同的“规则”,用于判断过程何时“失控”并存在特殊原因。有时称其为“西方电气规则”,因为它们最初由 Shewhart 在 Western Electric Company 工作期间制定。
清晰示例
为了更好地理解控制图的工作原理,让我们回顾一下 关于中心线化的帖子 中咖啡制作的例子,并设想每次制作一壶新咖啡时,都会在 1 到 10 的范围内评估咖啡浓度。然后将结果绘制在 控制图上,如下所示:
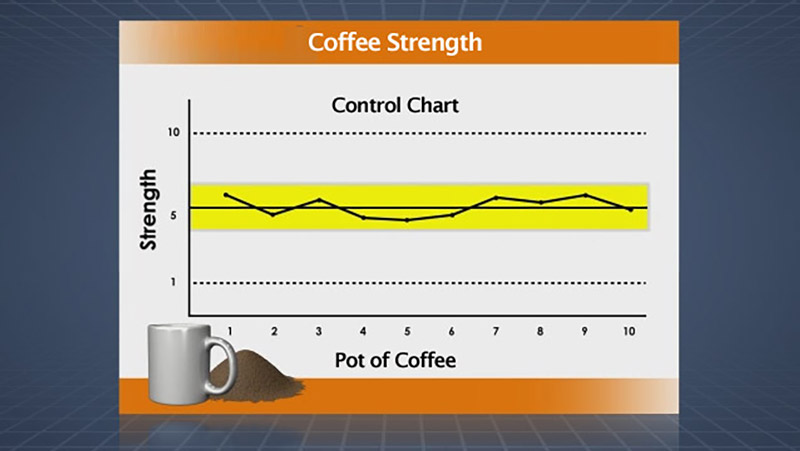
控制图在咖啡生产中的应用
回忆一下,水平中心线代表近期咖啡浓度数值的平均值,上下两条线代表控制上限和控制下限。如果咖啡制作过程稳定,仅受“普通原因”变化的影响,几乎所有的咖啡浓度值应落在两个控制限值之间,随机分布在平均值上下。
若咖啡浓度低于控制下限或高于控制上限,或者咖啡浓度呈上升或下降趋势,这将表明存在“特殊原因”,需要对过程进行调整或采取纠正措施。
在制造过程中使用控制图
有效使用控制图不仅可以进行过程变更,也可以尽量减少过程变更次数。我们来看几个控制图如何帮助维护过程完整性的例子:
实时过程监控
在实时操作中,有效的控制图应清晰地告知工厂操作员过程何时偏离了控制状态,促使操作员对过程进行调整。
利用您工厂的生产信息管理系统 (PIMS) 或 数据可视化软件 设置包含平均值和数据限值的视觉时间趋势图。配置警报或提醒,以便当标签值超出控制限值,或出现“特殊原因”迹象(符合其他西方电气规则之一)时触发提醒。
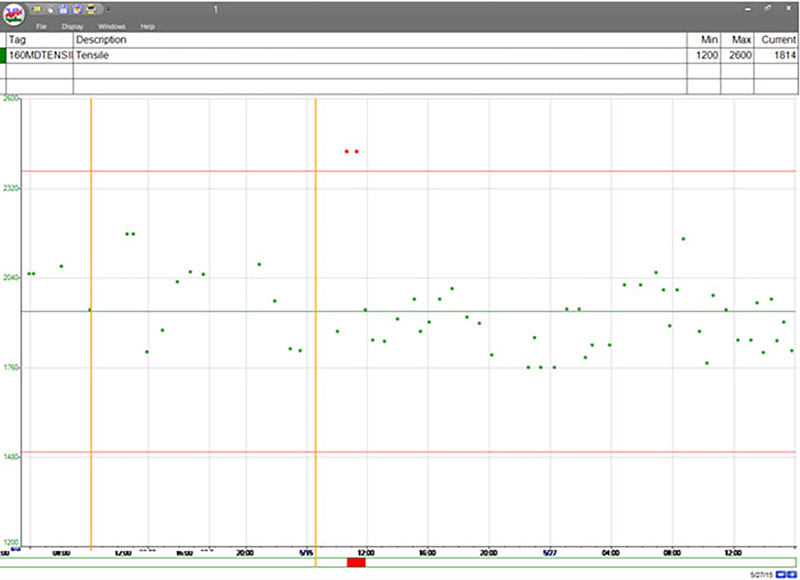
按品种/产品过滤控制图,以获得对单个过程更清晰的认识。
根本原因分析
有效控制图的另一个关键功能是促进根本原因分析活动的开展。许多 PIMS和软件(如 dataPARC 的 PARCview 应用程序)允许用户为失控事件分配标准化原因并添加注释。这些事件随后可用于使用帕雷托图和 KPI 报告 进行分析,以识别易于改善的问题并优化过程。
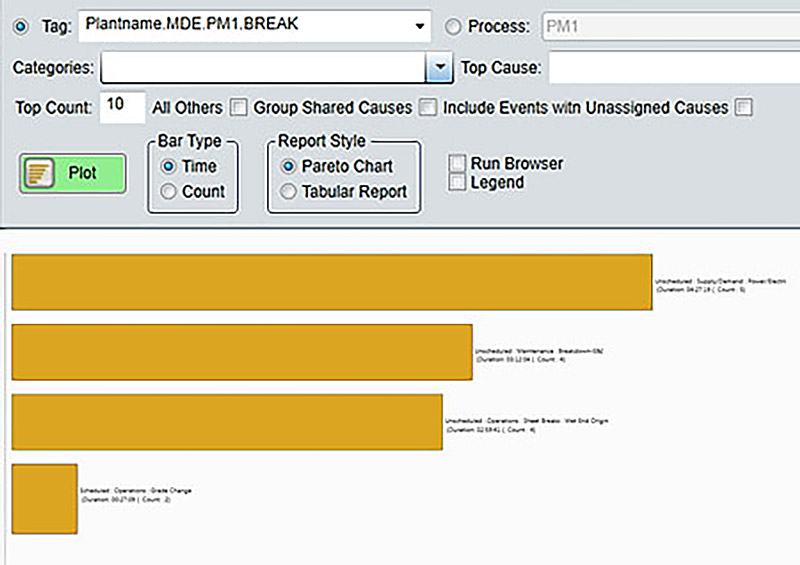
帕雷托图可以与控制图结合使用,以确定生产缺陷的根源。
欲了解更多关于 dataPARC 及其应用程序(包括 PARCalarm 和 PARCpde)如何自动计算特定品种或特定产品的过程标签控制限值并在整个系统中提供这些限值的信息,请访问 dataparc.com。
下载我们的概览数据表
点击以下链接,免费获取有关使用 dataPARC 将关键数据转化为可视化信息以进行及时决策的优势概述。
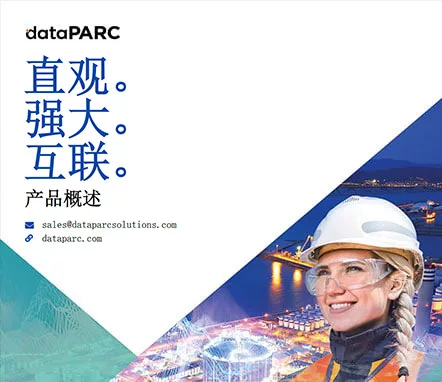